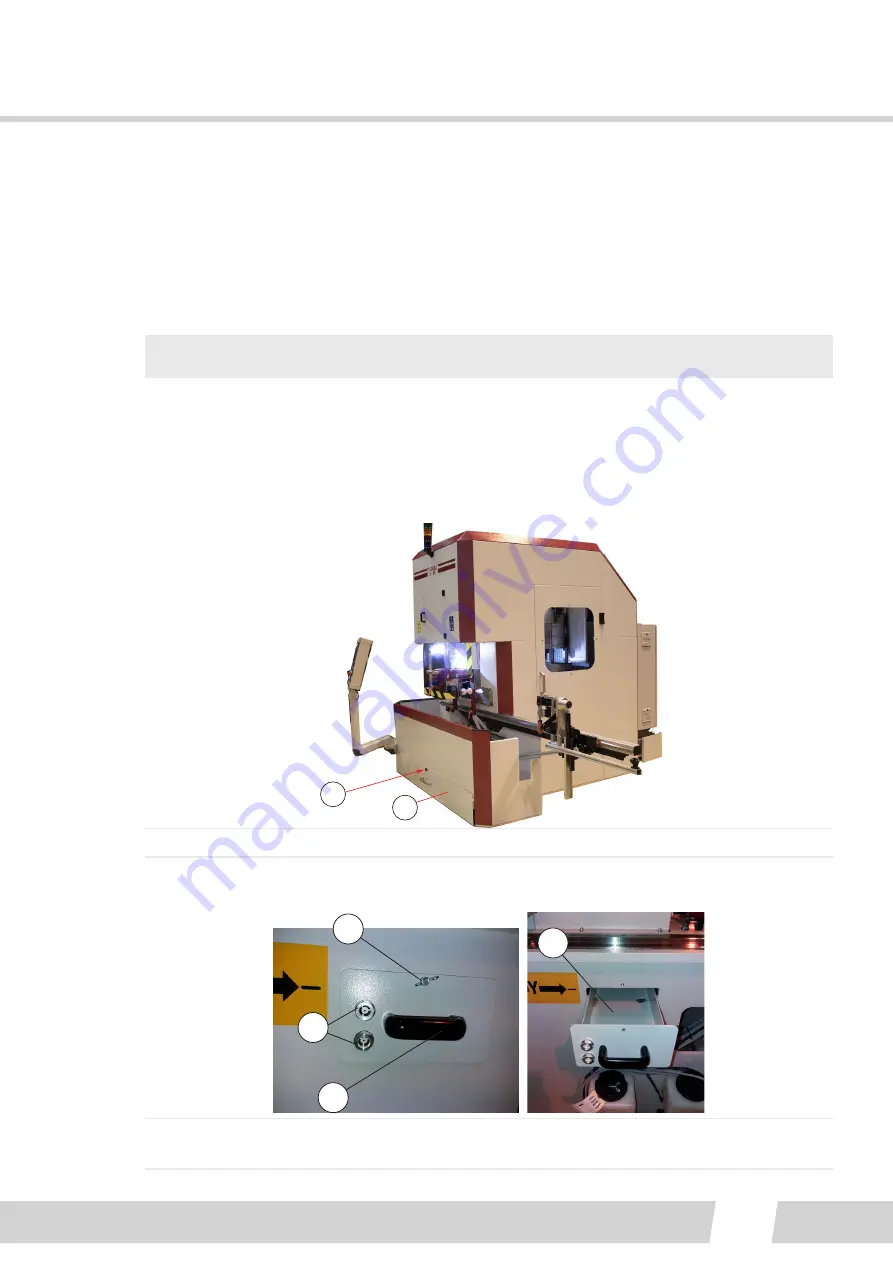
COLLARING MACHINE
77
S-80
8.5. SCREWJACK AND BALL SCREW DRIVE MAINTENANCE
The Z and GSZ series ZIMM Screw Jack are sealed and are filled with high-quality
synthetic low-viscosity grease; from size 250 kN they are filled with synthetic oil. Under
normal operating conditions the gearbox is lubricated for life.
Lubricate the screw jack ball crew drive of X, Y, Z movements every three (3) months
(when interval is 2 shift operation and 5 days / week).
For detailed maintenance instructions for Zimm screwjacks and accessories, refer
to separate manual.
8.6. OIL COLLECTORS
Check the large chip tray and oil and debris collecting tray daily, and empty when
required.
The large chip tray is positioned in front of the machine, under the clamps
. To open the
tray, release locking from the knob and pull out the tray. The tray has wheels under it.
2
1
1. Large chip tray, 2. Locking knob
The oil and debris collecting tray is positioned on the left side of the machine frame,
under the tool magazine.
The tray has oil level sight glasses on the front panel.
1
2
3
4
Oil and debris bin under the tool magazine: 1. Winged locking screw, 2. Oil sight glass, 3.
Handle, 4. Bin.