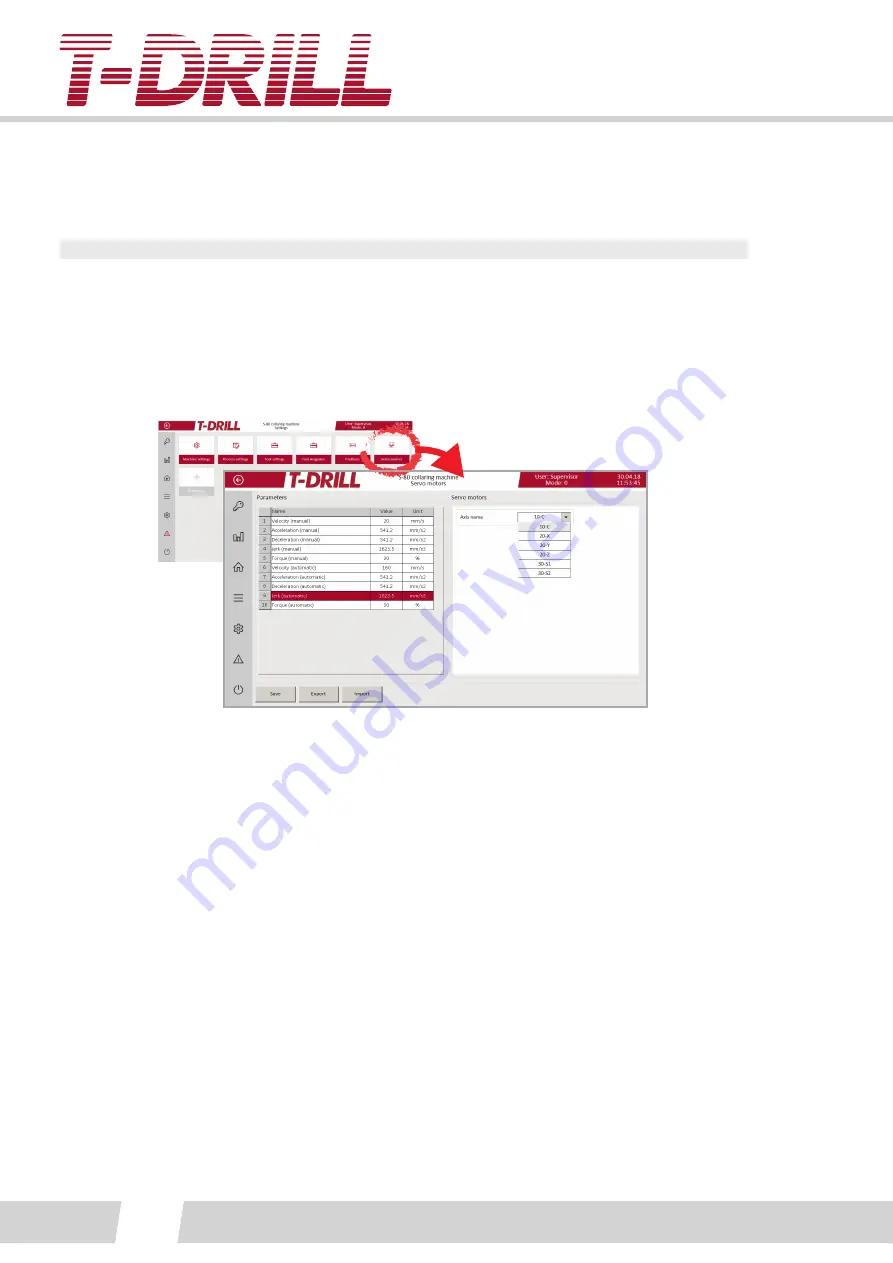
INSTRUCTION MANUAL
66
8.2. COLLARING UNIT MAINTENANCE AND ADJUSTMENT
Setting of the reference for X, Y and Z-axis, and collaring center point
This setting is only required if the spindle or servo cylinders have been changed.
The reference setting tool is fixed to the main frame. Set the reference zero point to
which all distances are compared to.
Switch the machine to MANUAL from the control panel switch. Place the positioning peg
into the milling tool adapter. Place the milling tool adapter to the machine chuck.
Set all torque and speed values to minimum to avoid collision and breakage from the
servo screen:
Instruction:
X- and Y-axis reference. Lower down the positioning peg very close to the surface of the
reference setting point tool using manual screen functions.
Attach a small dial gauge (with magnetic leg) to the spindle axle, and position the peg to
the center of the reference setting tool:
See photo. Point the gauge tip to ref. tool body. Rotate the spindle with hand, drive
sideways using manual screen functions and slow speed. (The dial gauge allowed reading
difference is 0.01mm).
Set the reference to the machine program from the “Reference” screen.
Position the Z-axis using the same fixed reference tool, remove tool holder and peg first.
Set the torque (manual) to zero, and the spindle will drop down on its own. Let it go
down to the surface of the reference tool. Rotate the spindle counter surfaces against the
reference tool surfaces.
Set the reference to the machine program from the “Reference” screen.