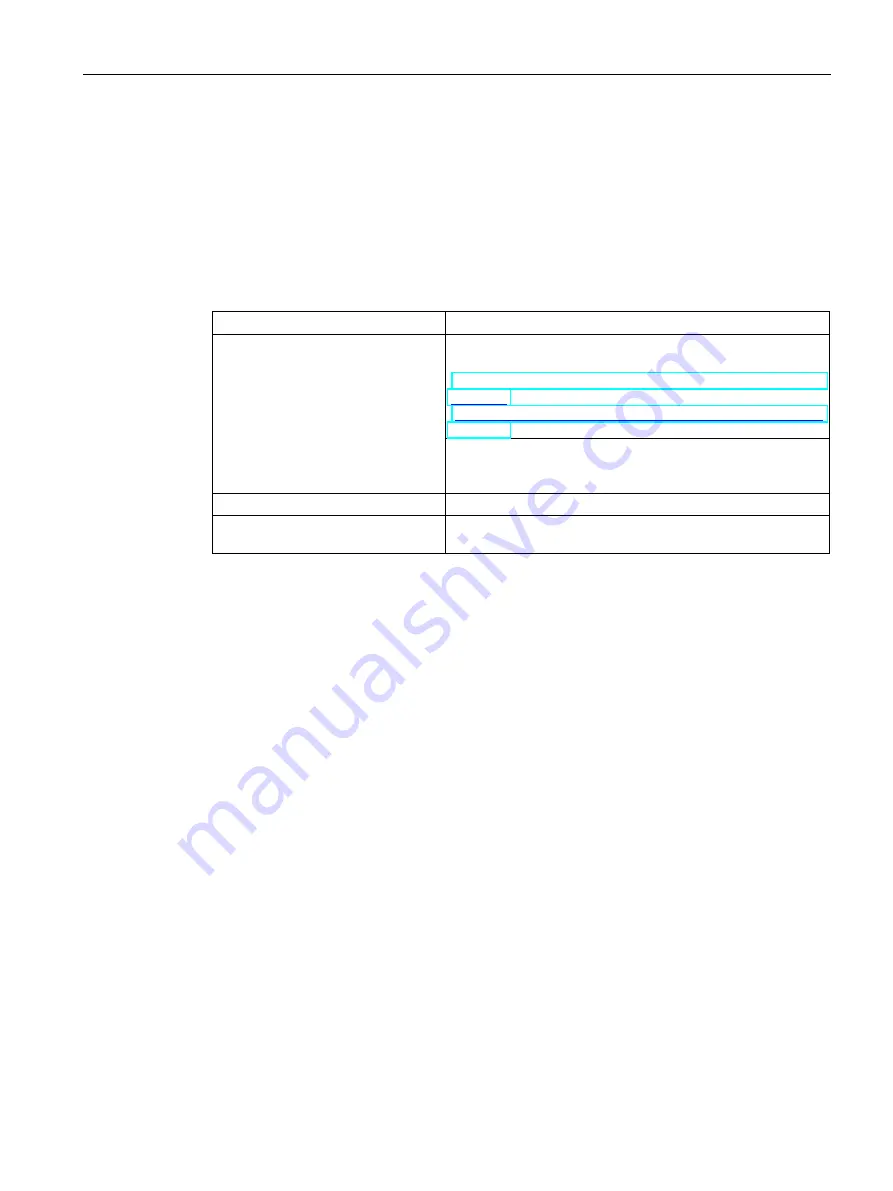
Application planning
3.3 Hardware configuration
Distributed I/O system
System Manual, 12/2016, A5E03576849-AG
41
3.3
Hardware configuration
Maximum mechanical configuration
As soon as one of the following rules applies, the maximum configuration of the ET 200SP
has been reached:
Table 3- 3
Maximum mechanical configuration
Properties
Rule
Number of modules
Maximum of 12/30/32/64 I/O modules (depending on the CPU
used/the interface module used; see CPU
http://support.automation.siemens.com/WW/view/en/9046643
) and interface module
http://support.automation.siemens.com/WW/view/en/5568331
) manuals)
For every 6 F-modules F-RQ 1x24VDC/24..230VAC/5A
(6ES7136-6RA00-0BF0), the maximum configuration is re-
duced by 1 module.
Number of motor starters
Maximum of 31 motor starters
Backplane bus length of the
ET 200SP
maximum 1 m mounting width (without CPU/interface module,
including server module)
Electrical maximum configuration for I/O modules
The number of operable I/O modules of a potential group is limited by the following factors:
●
Power consumption of the I/O modules
●
Power consumption of the components supplied via these I/O modules
The maximum current carrying capacity of the terminals on the BaseUnit L+/M is 10 A.
Current carrying capacity refers to the current load via the power bus and the infeed bus of
the ET 200SP station. Consider the current carrying capacity when using a motor starter.
Maximum electrical configuration for motor starter power bus (24 V DC)
To determine the current requirement of an individual motor starter via the power bus, take
account of the following parameters:
●
Current consumption via DC infeed in the ON state
●
Current consumption via DC infeed when switching on (40 ms peak load)
●
Increased power consumption through fan operation
●
Current requirement via encoder supply of the connected DI module
The maximum current carrying capacity of the 24 V potential group is 7 A across the entire
permissible temperature range.
Summary of Contents for Simantic ET200SP
Page 1: ......