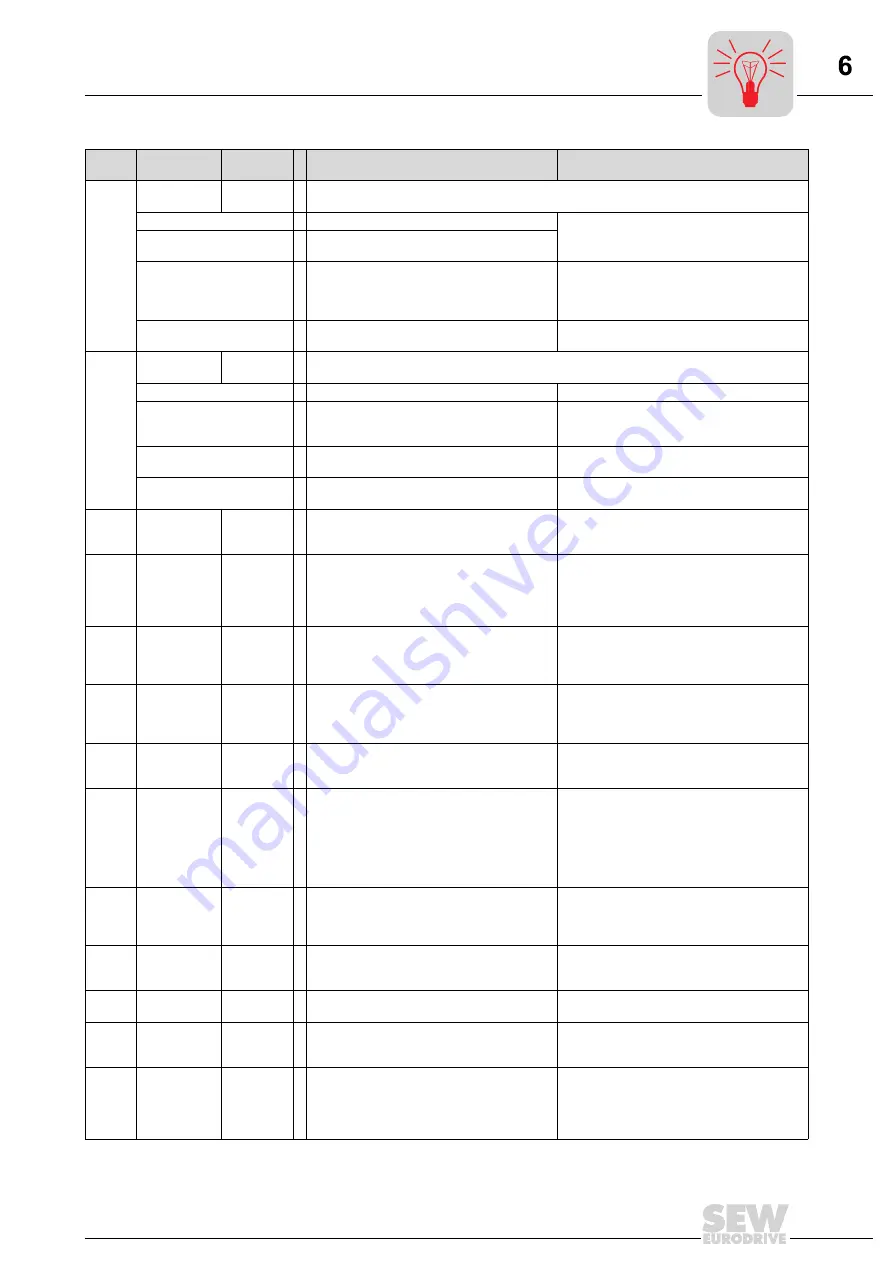
MOVIDRIVE
®
MD_60A Operating Instructions
75
Fault messages and list of faults
70
Timeout DPx-
SSI
No
response
Coded fault; only with DPA11A.
Code 1: SSI interface fault.
SSI module defective.
Inform SEW Service if fault cannot be reset or
if it occurs frequently.
Code 2: Communication
fault of SSI interface.
SSI module defective.
Code 3: Parity or power
failure fault from SSI
encoder.
•
Encoder cable disrupted
•
Electrical power supply disrupted
•
Incorrect setting of machine parameters
•
Check encoder cable
•
Check electrical power supply
•
Check machine parameters and correct if
necessary
Code 4: Lag error in SSI
module
Data transfer between encoder and DPA11A
disrupted.
Check connection cable and associated
shield.
71
Timeout DPx-
CAN
No
response
Coded fault; only with DPA11A.
Code 1: Timeout CAN.
CAN bus communication interrupted.
Check the CAN bus connection.
Code 2: CAN receive buffer
full.
Systematic program error caused by
excessively frequent writing of CAN bus
interface of an inverter.
Reduce write accesses to inverter concerned
in user program.
Code 3: CAN controller
overflow.
CAN controller malfunction.
Inform SEW Service if fault cannot be reset or
if it occurs frequently.
Code 4: CAN controller
error.
Malfunction on the CAN bus. Possibly, no
nodes are present.
Check wiring and user program.
72
Index overrun
No
response
Only with DPx11A:
Fault with indexed variable index. Offset
variable Cxx greater than C99 selected.
Correct user program.
73
Unauthorized
command
No
response
Only with DPx11A:
Command was transmitted which cannot be
carried out in current status of inverter. For
example, transmitting the SAVE command
during a positioning process.
Check user program.
74
Range limit
No
response
Only with DPx11A:
Calculated setpoint position in increments
greater than 230 and therefore located outside
range limit.
Check user program.
77
IPOS control
word
No
response
Only in IPOS operating mode:
•
Attempt was made to set an invalid
automatic mode (via external control).
•
P916 = BUSRAMP set.
•
Check serial connection to external
control.
•
Check write values of external control.
•
Set P916 correctly.
78
IPOS SW limit
switches
No
response
Only in IPOS operating mode:
Programmed target position is outside travel
range delimited by software limit switches.
•
Check user program
•
Check position of software limit switches
81
Start condition
Immediate
switch-off
Only in "VFC hoist" operating mode:
Current during premagnetization phase could
not be injected into motor at a high enough
level:
•
Motor rated power too small in relation to
inverter rated power.
•
Motor cable cross section too small.
•
Check startup data and repeat startup
procedure if necessary.
•
Check connection between inverter and
motor.
•
Check cross section of motor cable and
increase if necessary.
82
Output open
Immediate
switch-off
Only in "VFC hoist" operating mode:
•
Two or all output phases interrupted.
•
Motor rated power too small in relation to
inverter rated power.
•
Check connection between inverter and
motor.
•
Check startup data and repeat startup
procedure if necessary.
84
Motor
protection
Emergency
stop
•
Motor utilization too high.
•
Reduce load.
•
Extend ramps.
•
Observe longer pause times.
85
Copy
Immediate
switch-off
Fault when copying parameters.
Check connection between inverter and PC.
88
Flying start
Immediate
switch-off
Only in "VFC n-CTRL" operating mode:
Actual speed > 5000 rpm when inverter
enabled.
Enable only at actual speed
≤
5000 rpm.
92
DIP work area
Emergency
stop
Only with DIP11A option:
Drive has moved beyond the permitted work
area of the absolute encoder. Setting of
encoder type/work area DIP parameters may
be incorrect.
Check position offset and zero offset
parameters.
Fault
code
Description
Reaction
P Possible cause
Measure
Summary of Contents for MOVIDRIVE MD*60A Series
Page 3: ...MOVIDRIVE MD_60A Edition 09 2001 Operating Instructions 1053 2617 EN ...
Page 4: ...SEW EURODRIVE ...
Page 100: ...10 2000 ...
Page 101: ...10 2000 ...