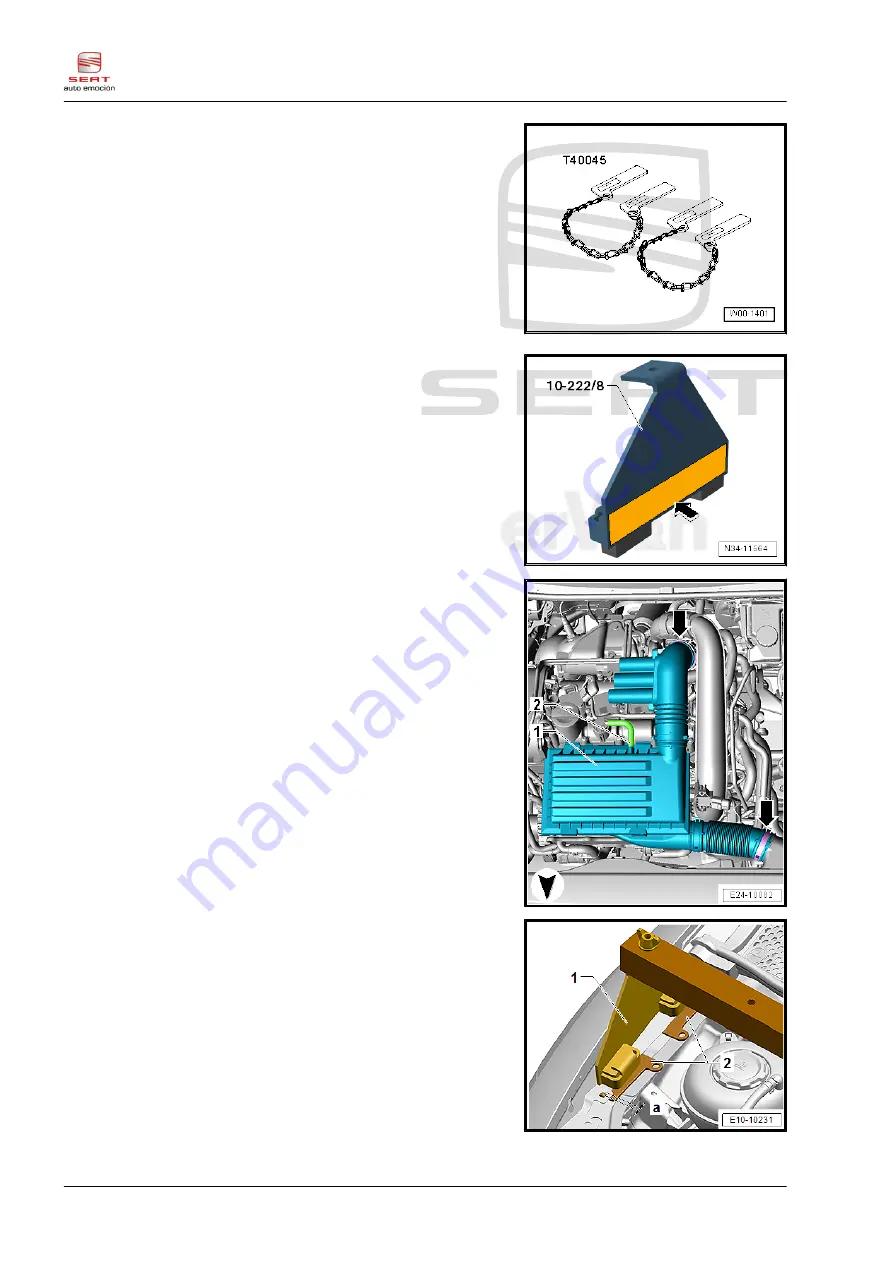
Protected by copyright. Copying for private or commercial purposes, in part or in whole, is not
permitted unless authorised by SEAT S.A. SEAT S.A does not guarantee or accept any liability with
respect to the correctness of information in this document. Copyright by SEAT S.A.
♦ Gauge - T40045-
To prevent damage to edges of wings, cover lower areas of both
adapters - 10 - 222 A /8- with woven adhesive tape -arrow- ⇒
Electronic Parts Catalogue (ETKA) .
Work sequence
– Separate the air hose -2- from the air filter housing.
– Carefully remove the air filter housing -1- from the retaining
bolts in an upward motion, sequentially.
– Loosen the brackets -arrow- for the air duct hose.
– Disconnect the air filter housing -1- with the air duct hoses.
• Insert and align the gauges - T40045- -2- as shown in the il‐
lustration in the front longitudinal members right and left. When
doing so, observe the height -a-.
• Attach the adapter - 10 - 222 A /8- -1- on left and right onto
longitudinal members as shown in illustration.
León 2013 ➤ , León ST 2013 ➤
4-cylinder petrol engine (1.2 l direct injection, 4 V, turbocharger, EA211) - Edition 02.2017
28
Rep. gr.10 - Removing and installing engine