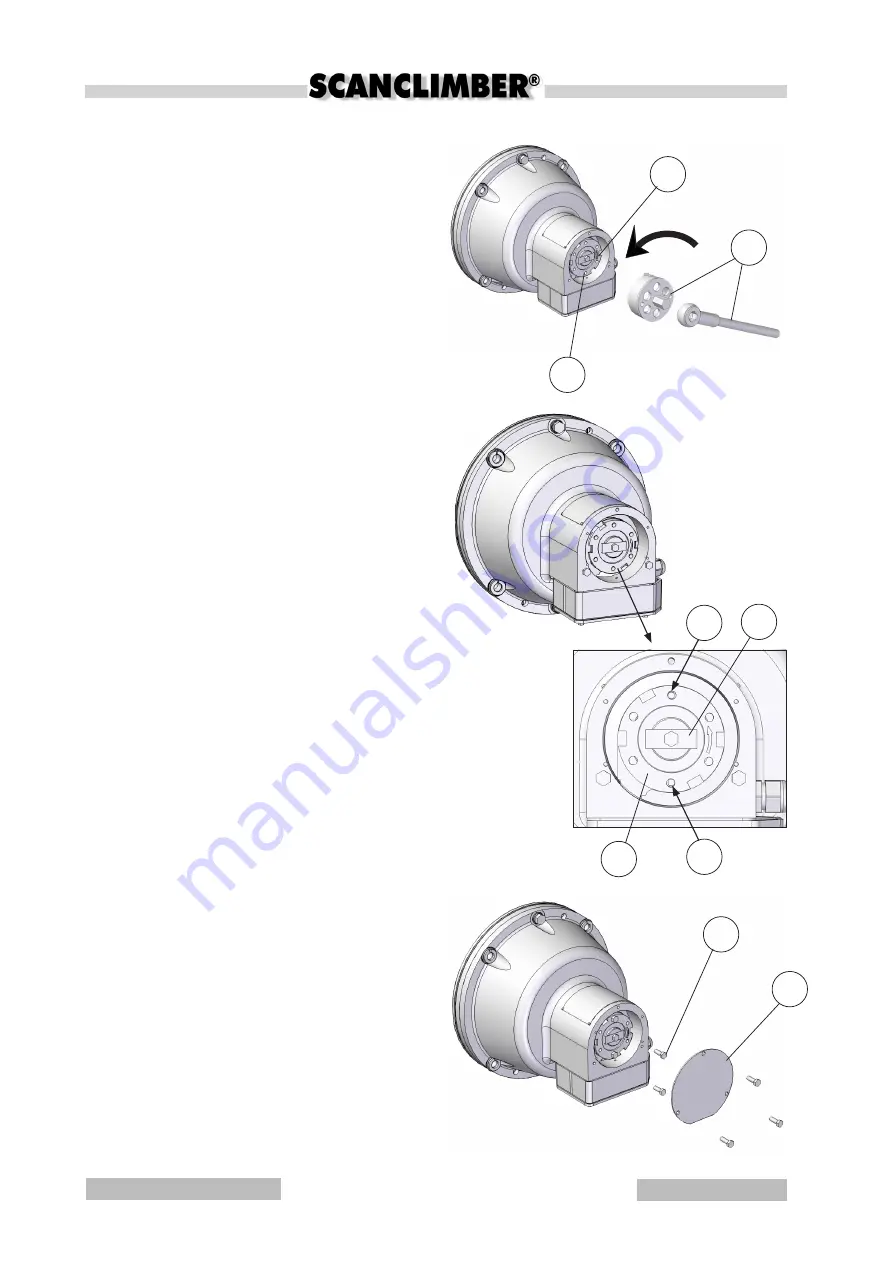
24
V115E_09.20
Service and maintenance
Series-65H Hoist Pos 5
5
6
4
4
5
2
3
3
3
6. Install the two screws (3).
7. Mount the cover (2)
4. Rotate the bronze nut (4) coun-
ter clockwise (unscrew) until it rests
against the top plate(5). Do not bend
the plate. Use the special key(6).
5 Rotate the bronze nut (4) by hand to
align the two screw (3).
Summary of Contents for 65H Series
Page 2: ...2 T a b l e o f C o n t e n t s Series 65H Hoist Pos 0 V115E_09 20...
Page 10: ...G e n e r a l i n f o r m a t i o n 2 V115E_09 20 Series 65H Hoist Pos 1...
Page 26: ...G e n e r a l i n f o r m a t i o n 18 V115E_09 20 Series 65H Hoist Pos 1 4450 L L1 L2 TWIN...
Page 34: ...G e n e r a l i n f o r m a t i o n 26 V115E_09 20 Series 65H Hoist Pos 1...
Page 36: ...S a f e t y i n s t r u c t i o n s 2 V115E_09 20 Series 65H Hoist Pos 2...
Page 46: ...S a f e t y i n s t r u c t i o n s 12 V115E_09 20 Series 65H Hoist Pos 2 MAX 1000 kg TH_10E...
Page 54: ...S a f e t y i n s t r u c t i o n s 20 V115E_09 20 Series 65H Hoist Pos 2 Tx527...
Page 55: ...21 S a f e t y i n s t r u c t i o n s V115E_09 20 Series 65H Hoist Pos 2...
Page 82: ...O p e r a t i n g i n s t r u c t i o n s 24 V115E_09 20 Series 65H Hoist Pos 3...
Page 84: ...2 V115E_09 20 T r o u b l e s h o o t i n g Series 65H Hoist Pos 4...
Page 124: ...10 V115E_09 20 Service and maintenance Series 65H Hoist Pos 5...
Page 144: ...30 V115E_09 20 Service and maintenance Series 65H Hoist Pos 5 Picture 3c Picture 3b...
Page 154: ...40 V115E_09 20 Service and maintenance Series 65H Hoist Pos 5...
Page 156: ...Inspection forms V115E_09 20 Series 65H Hoist Pos 8 SC HOIST INSPECTION FORMS...
Page 164: ...Inspection forms V115E_09 20 Series 65H Hoist Pos 8 SC HOIST INSPECTION FORMS...