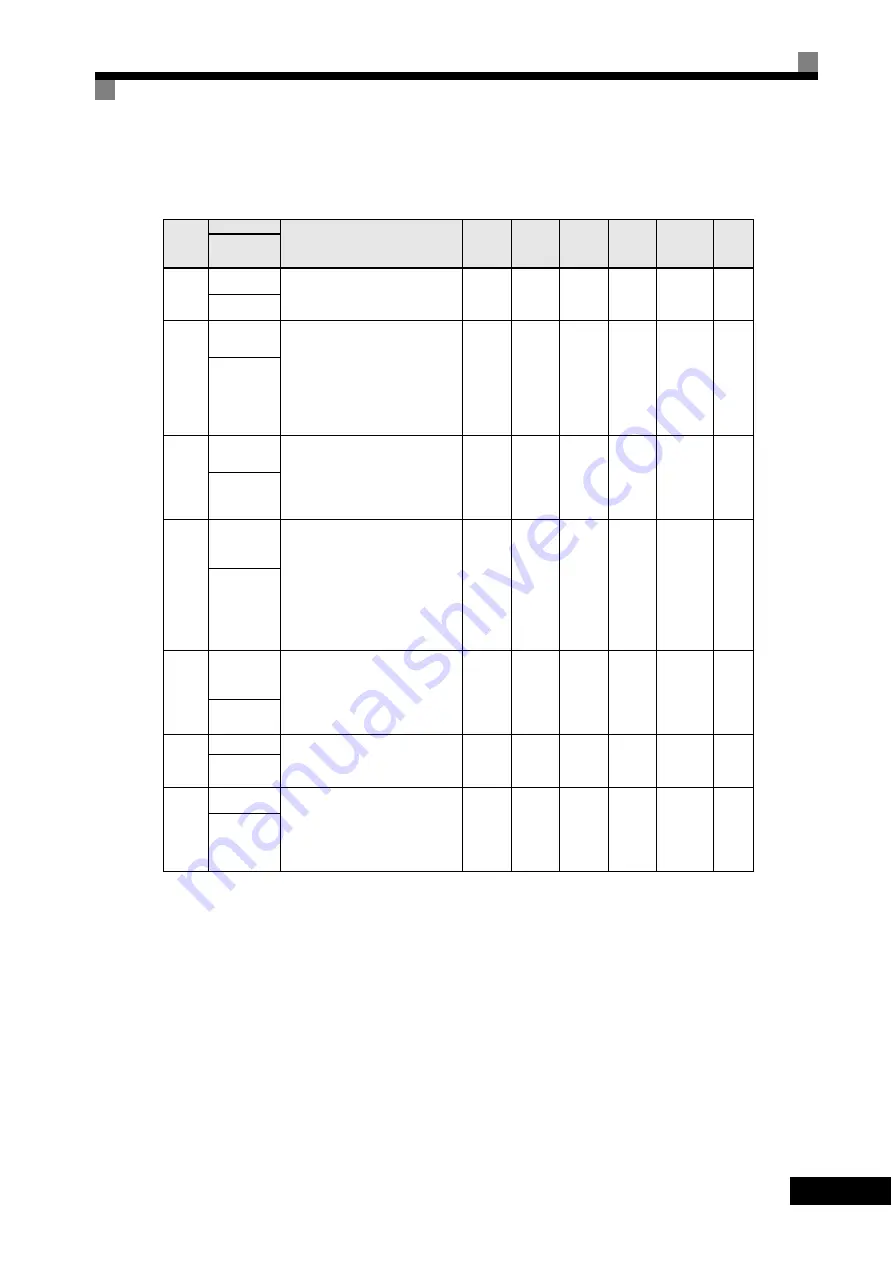
Parameter Tables
5
-
25
RS-422A/485 Communications: H5
* Set H5-01 to 0 to disable Inverter responses to RS-422A/485 communications.
Parame-
ter
Number
Name
Description
Setting
Range
Factory
Setting
Change
during
Opera-
tion
Access
Level
RS-422A/
485
Register
Page
LCD
Display
H5-01
Station
address
Set the Inverter's node address.
0 to 20
*
1F
No
A
425H
6-54
Serial Comm
Adr
H5-02
Communica-
tion speed
selection
Set the baud rate for 6CN RS-
422A/485 communications.
0: 1200 bps
1: 2400 bps
2: 4800 bps
3: 9600 bps
4: 19200 bps
0 to 4
3
No
A
426H
6-54
Serial Baud
Rate
H5-03
Communica-
tion parity
selection
Set the parity for 6CN RS-422A/
485 communications.
0: No parity
1: Even parity
2: Odd parity
0 to 2
0
No
A
427H
6-54
Serial Com Sel
H5-04
Stopping
method after
communica-
tion error
Set the stopping method for com-
munications errors.
0: Deceleration to stop using
deceleration time in C1-02
1: Coast to stop
2: Emergency stop using decele-
ration time in C1-09
3: Continue operation
0 to 3
3
No
A
428H
6-54
Serial Fault Sel
H5-05
Communica-
tion error
detection
selection
Set whether or not a communica-
tions timeout is to be detected as a
communications error.
0: Do not detect.
1: Detect
0 or 1*
1
No
A
429H
6-54
Serial Flt Dtct
H5-06
Send wait time
Set the time from the Inverter
receiving data to when the
Inverter starts to send.
5 to 65
5 ms
No
A
42AH
6-54
Transmit Wait-
TIM
H5-07
RTS control
ON/OFF
Select to enable or disable RTS
control.
0: Disabled (RTS is always ON)
1: Enabled (RTS turns ON only
when sending)
0 or 1
1
No
A
42BH
6-54
RTS Control
Sel