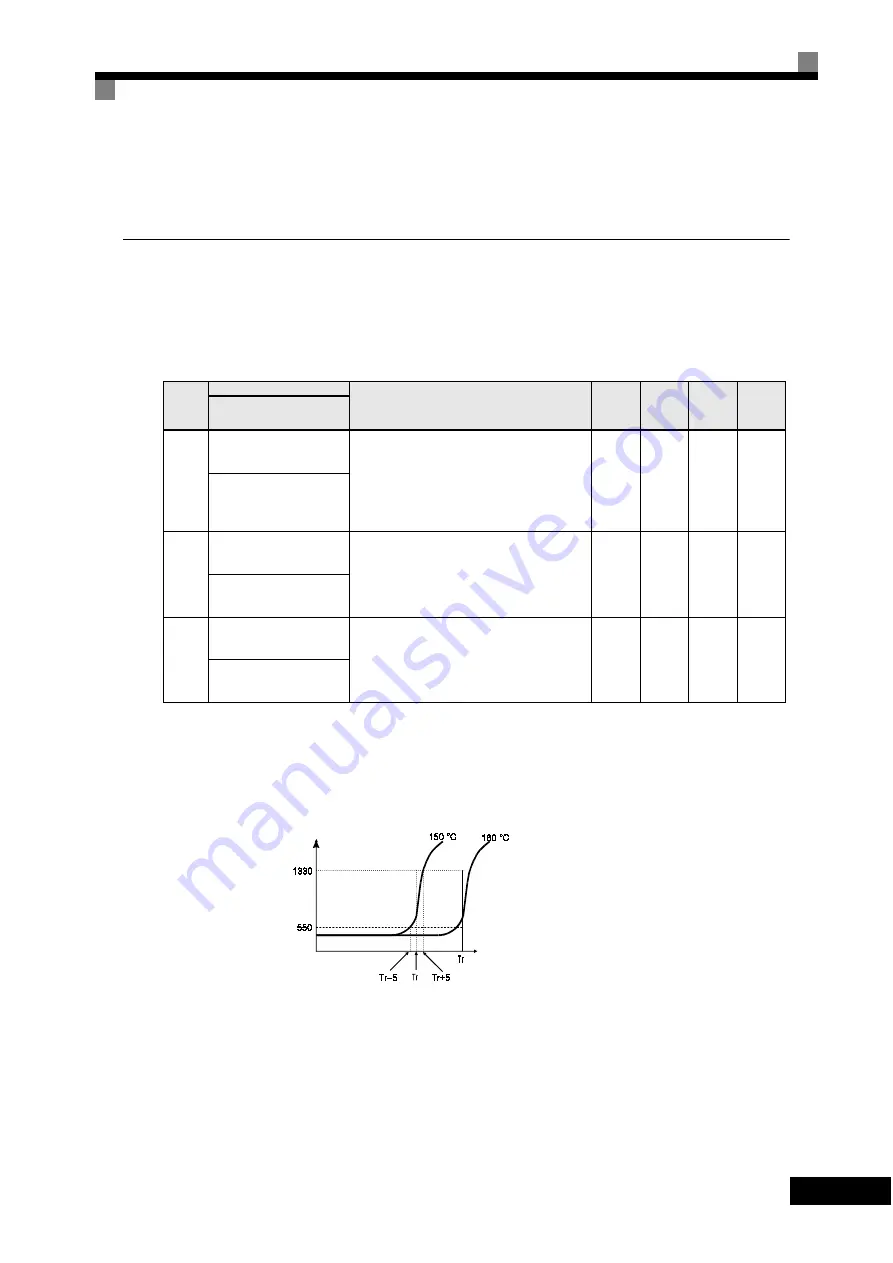
Machine Protection
6
-
35
motor overload pre-alarm will be enabled. If the electronic thermal value reaches minimum 90% of the over-
load detection level, the output terminal that has been set will be turned ON.
Motor Overheating Protection Using PTC Thermistor Inputs
Perform motor overheating protection using the thermistor temperature resistance characteristics of the PTC
(Positive Temperature Coefficient) built into the windings of each motor phase.
Related Parameters
PTC Thermistor Characteristics
The following diagram shows the characteristics of the PTC thermistor temperature to the resistance value.
Fig 6.27 PTC Thermistor Temperature-Resistance Value Characteristics
Param-
eter-
Number
Name
Description
Setting
Range
Factory
Setting
Change
during
Opera-
tion
Access
Level
LCD Display
L1-03
Alarm operation selection dur-
ing motor overheating
Set H3-09 to E and select the operation when the input
motor temperature (thermistor) input exceeds the alarm
detection level (1.17 V).
0: Decelerate to stop
1: Coast to stop
2: Emergency stop using the deceleration time in C1-09.
3: Continue operation (OH3 on the Digital Operator
flashes).
0 to 3
3
No
A
Mtr OH Alarm Sel
L1-04
Motor overheating operation
selection
Set H3-09 to E and select the operation when the motor
temperature (thermistor) input exceeds the operation
detection level (2.34 V).
0: Decelerate to stop
1: Coast to stop
2: Emergency stop using the deceleration time in C1-09.
0 to 2
1
No
A
Mtr OH Fault Sel
L1-05
Motor temperature input filter
time parameter
Set H3-09 to E and set the primary delay time parameter
for motor temperature (thermistor) inputs in seconds.
0.00 to
10.00
0.20 s
No
A
Mtr Temp Filter
Resistance (Ohms)
Class F Class H
Tr: Temperature threshold value
Temperatue