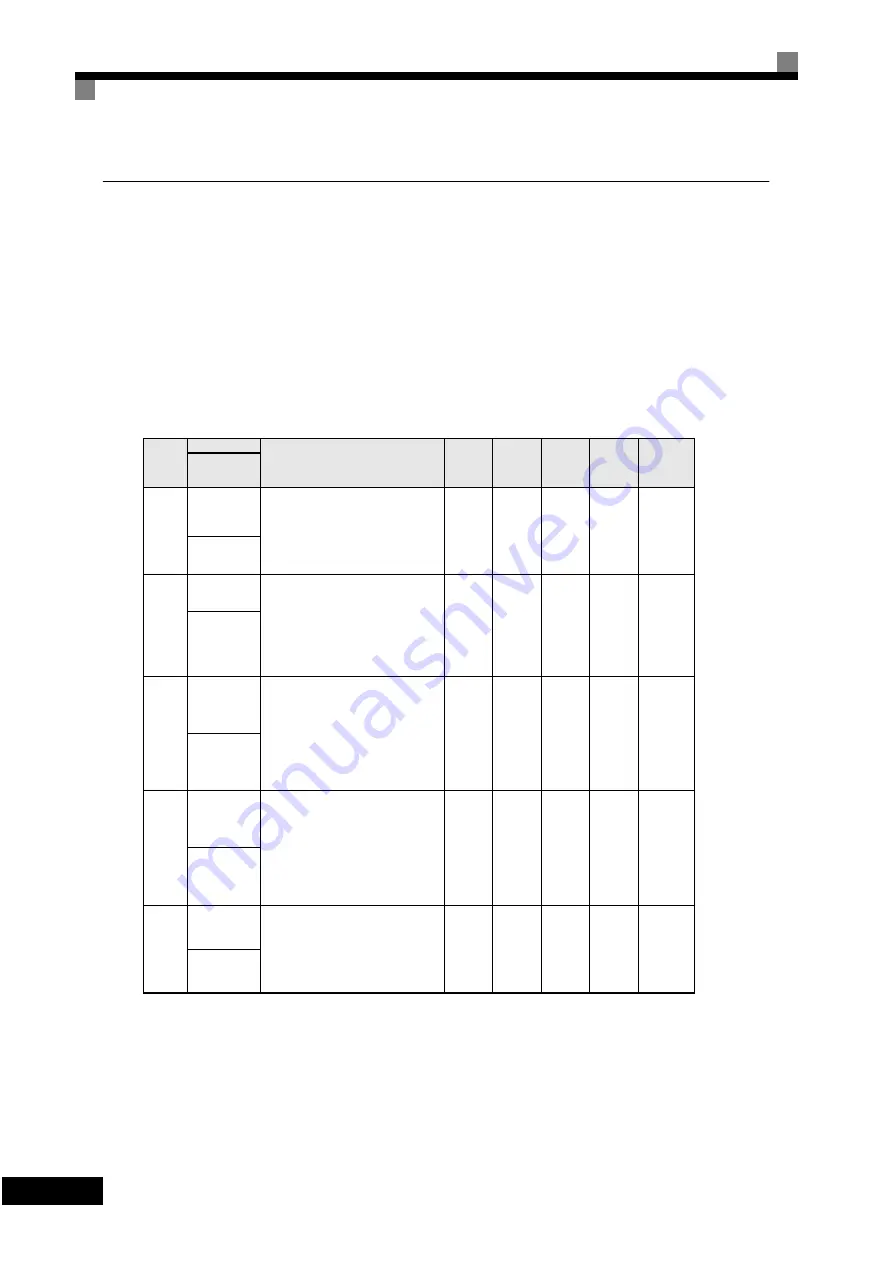
6
-14
Using Highslip braking
When the system is operating, the Inverter is delivering an amount of electrical energy to the motor, this
energy is transformed into mechanical and thermal energy.
As a generator, the motor efficiency is still high. Most of the energy returns to the Inverter as current flow.
This regenerated current is stored in the DC bus capacitors, increasing the DC bus voltage. If the regenerated
energy is bigger than the Inverter losses (10% or less) the DC bus will increase to a level where the braking
resistor starts working. If no braking resistor is installed the DC voltage will increase up to a level where the
Inverter operation will be stopped and an overvoltage (OV) is shown.
Related parameters
Param-
eter-
Number
Name
Description
Setting
Range
Factory
Setting
Change
during
Opera-
tion
Access
Level
RS-422A/
485
Register
LCD
Display
n3-01
High-slip brak-
ing decelera-
tion frequency
width
Sets the frequency width for
deceleration during high-slip
braking in percent, taking the
Maximum Frequency (E1-04) as
100%.
1 to 20
5%
No
A
588H
HSB Decel
Width
n3-02
High-slip brak-
ing current
limit
Sets the current limit for decelera-
tion during high-slip braking in
percent, taking the motor rated
current as 100%. The resulting
limit must be 150% of the Inverter
rated current or less.
100 to
200
150%
No
A
589H
HSB Current
Ref
n3-03
High-slip brak-
ing stop dwell
time
Sets the dwell time for the output
frequency for FMIN (1.5 Hz) dur-
ing V/f control.
Effective only during deceleration
for high-slip braking.
0.0 to
10.0
1.0 s
No
A
58AH
HSB Dwel-
Tim@Stp
n3-04
High-slip brak-
ing OL time
Set the OL time when the output
frequency does not change for
some reason during deceleration
for high-slip braking.
30 to
1200
40 s
No
A
58BH
HSB Ol Time
H1-01
-
H1-05
Terminal sel
S3-S7
Multifunction Digital Inputs
0 to 77
No
A
400H
to
404H
Terminal sel
S3-S7