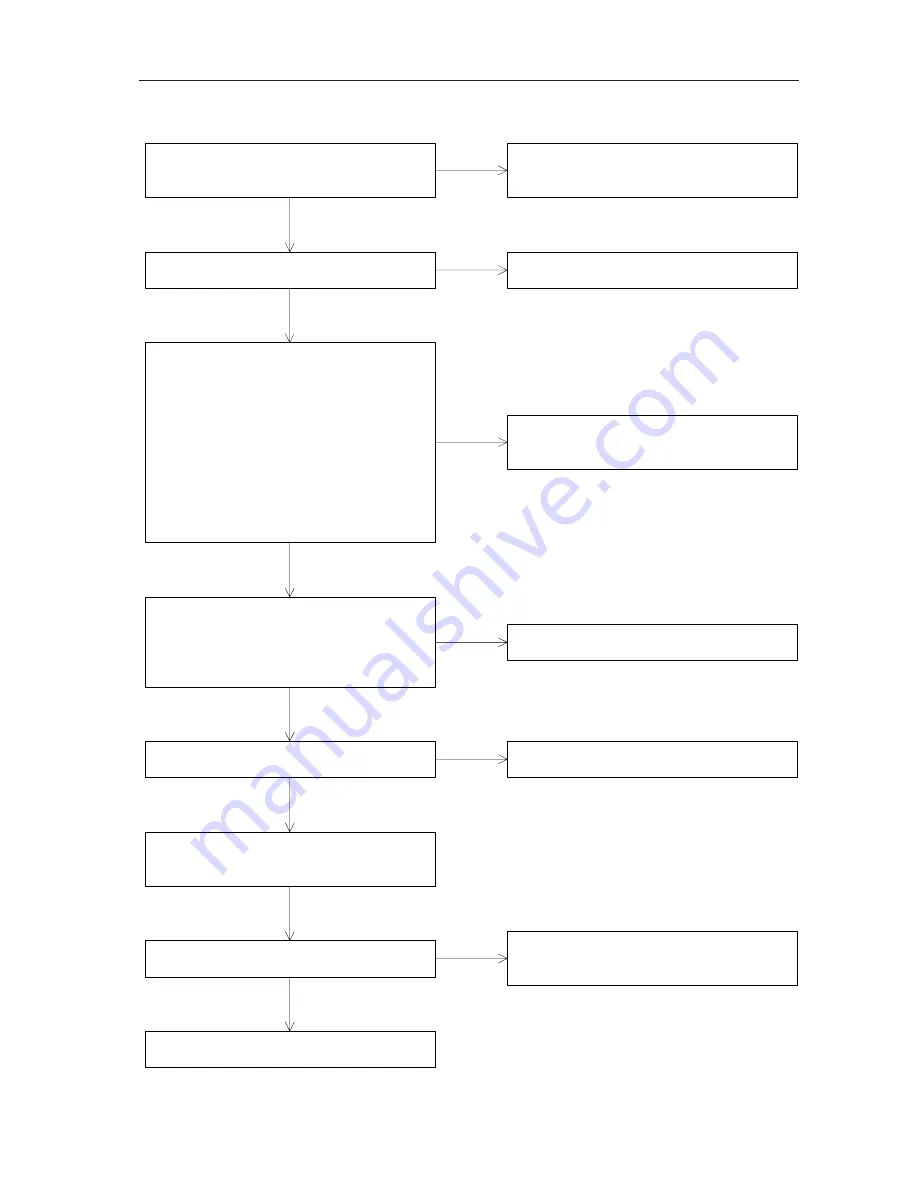
4 - 23
LLE11ARDA001A/E
Replace the CA23 cable (40350-CA23) with the new
one.
Deos the CA23 cable (40350-CA23) break?
Is there a continuity between the following connectors
on the BA06 board (40350-BA06)?
P601(J1) connector - P606(J6) connector
7
-
1 pins
8
-
2 pins
9
-
3 pins
10
-
4 pins
11
-
5 pins
12
-
6 pins
P601(J1) connector - P608(J8) connector
13(14)
-
1 pins
18
-
2 pins
Is the voltage between the 2-GND of the P608(J8) as
described below when shading the sensor of the CA41
cable (40350-CA41)?
The sensor is shaded.
:DC 0V
The sensor is not shaded.
:DC+5V
Does the CA12 cable (40350-CA12) with the new one.
Replace the BA06 board (40350-BA06) with the new
one.
(See 6.1.6.)
Replace the CA41 cable (40350-CA41) with the new
one.
Replace the CA12 cable (40350-CA12) with the new
one.
No
Yes
Yes
Yes
No
No
No
Yes
Replace the BA02 board (40350-BA02) with the new
one.
(See 6.1.2.)
Replace the BA01 board (40350-BA01) with the new
one.
(See 6.1.1.)
Is the symptom improved?
No
Yes
Is the voltage between the 13-15 (14-16) pins of the
P211(J11) connector on the BA02 board (40350-
BA02) DC+5V?
Replace the BA02 board (40350-BA02) with the new
one.
(See 6.1.2.)
Yes
No
Completion
4.3.3.12 412-Drill R Initialize error is displayed.
Summary of Contents for ME-1000
Page 8: ...1 2 LLE11ARDA001A E...
Page 12: ...3 2 LLE11ARDA001A E...
Page 120: ...7 34 LLE11ARDA001A E...
Page 121: ...8 1 LLE11ARDA001A E 8 SUPPLEMENT 8 1 Wiring Diagram...
Page 122: ...8 2 LLE11ARDA001A E 8 2 Connector Cable...
Page 123: ...8 3 LLE11ARDA001A E...
Page 125: ...8 5 LLE11ARDA001A E 8 4 Labels Top view Processing chamber...
Page 126: ...8 6 LLE11ARDA001A E Rear view or...