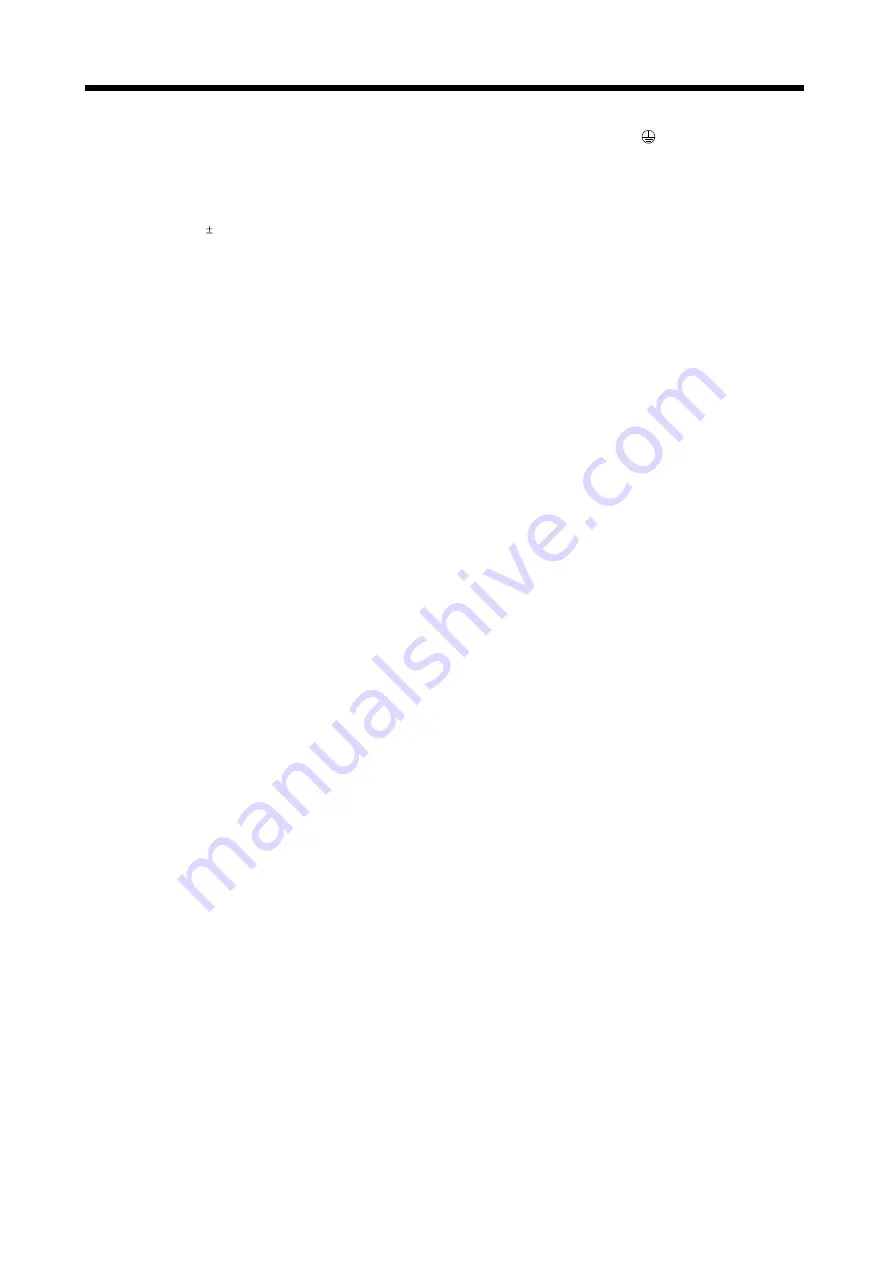
3 - 5
3. SIGNALS AND WIRING
Note 1. To prevent an electric shock, always connect the protective earth (PE) terminal (terminal marked ) of the servo amplifier main
circuit power connector (CNP1) to the protective earth (PE) of the control box.
2. Connect the diode in the correct direction. If it is connected reversely, the servo amplifier will be faulty and will not output
signals, disabling the emergency stop and other protective circuits.
3. The forced stop switch (normally closed contact) must be installed.
4. Supply 24VDC 10% 200mA current for interfaces from the outside. 200mA is the value applicable when all I/O signals are used.
The current capacity can be decreased by reducing the number of I/O points. Refer to section 3.8.2 (1) that gives the current
value necessary for the interface.
5. When starting operation, always switch on the forced stop (EM1) or the forward/reverse rotation stroke end (LSP, LSN).
(Normally closed contacts)
6. Trouble (ALM) turns on in normal alarm-free condition. (Normally closed contact) When this signal is switched off (at occurrence
of an alarm), the output of the programmable controller should be stopped by the sequence program.
7. The pins with the same signal name are connected in the servo amplifier.
8. This length applies to the command input pulses in the open collector system. The wirings can be extended up to 10m when
using positioning modules with the differential line driver type.
9. Use MRZJW3-SETUP221E (C4 or later).
10. This diagram shows sink I/O interface. For source I/O interface, refer to section 3.8.3.
11. The assigned signals can be changed using the settings of parameter No. PD03 to PD14.
12. The assigned signals can be changed using the settings of parameter No. PD15 to PD18.
13. Select the number of I/O points of the programmable controllers in accordance with the system.
14. Select it within X0 to X7.
15. When a command cable for connection with the controller side malfunctions due to disconnection or noise, a position mismatch
can occur. To avoid position mismatch, it is recommended that Encoder A-phase pulse and Encoder B-phase pulse be checked.
Summary of Contents for MELSERVO-JN Series
Page 31: ... 22 MEMO ...
Page 49: ...2 6 2 INSTALLATION MEMO ...
Page 181: ...5 30 5 DISPLAY AND OPERATION SECTIONS MEMO ...
Page 199: ...6 18 6 GENERAL GAIN ADJUSTMENT MEMO ...
Page 303: ...11 46 11 OPTIONS AND PERIPHERAL EQUIPMENT MEMO ...
Page 351: ...12 48 12 SERVO MOTOR MEMO ...
Page 445: ...13 94 13 POSITIONING MODE MEMO ...