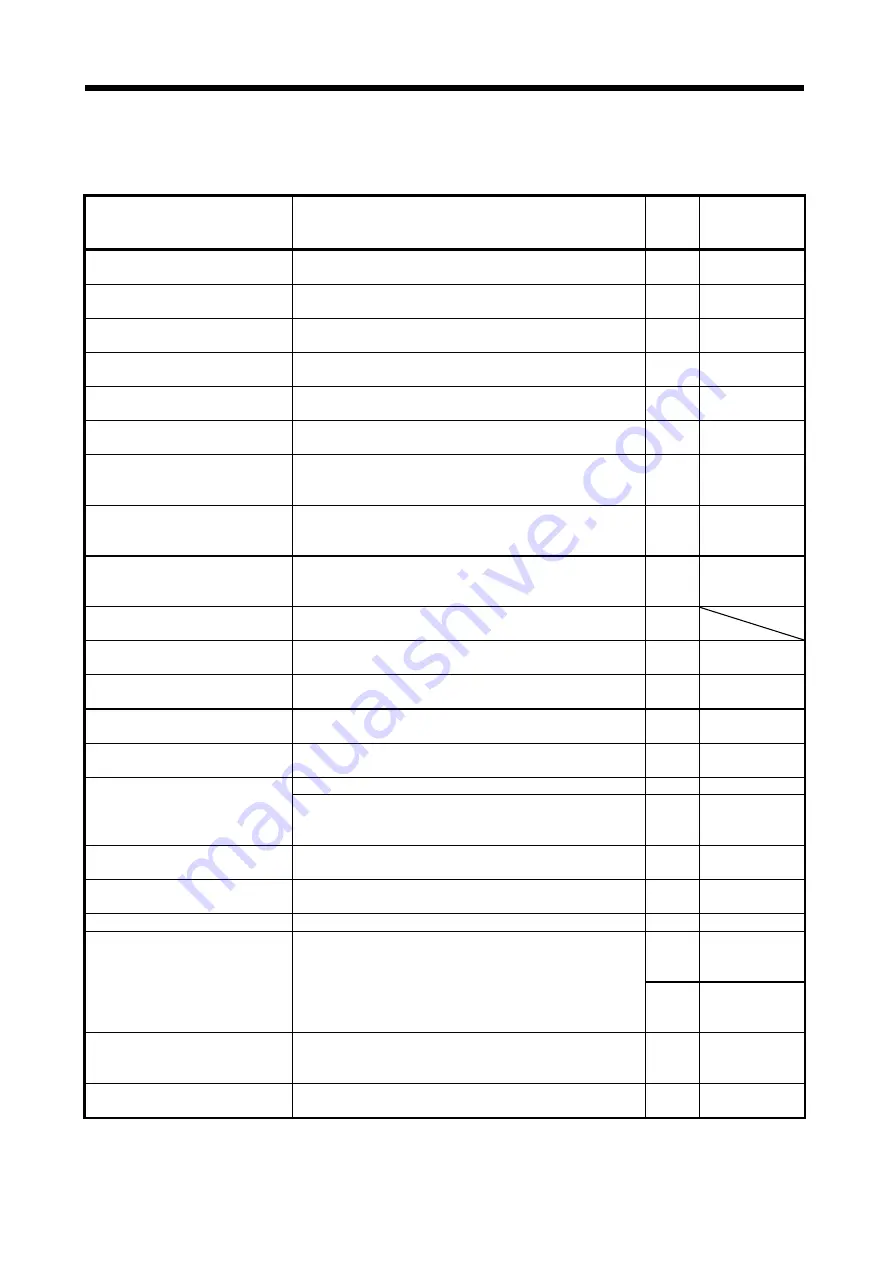
1 - 8
1. FUNCTIONS AND CONFIGURATION
1.4 Function list
The following table lists the functions of this servo. For details of the functions, refer to the reference field.
Function
Description
(Note 1)
Control
mode
Reference
Position control mode
This servo is used as position control servo.
P
Section 3.2.1
Section 3.6.1
Internal speed control mode
This servo is used as internal speed control servo.
S
Section 3.2.2
Section 3.6.2
Internal torque control mode
This servo is used as internal torque control servo.
T
Section 3.2.3
Section 3.6.3
Position/internal speed control
change mode
Using input device, control can be switched between position
control and internal speed control.
P/S Section 3.6.4
Internal speed/internal torque control
change mode
Using input device, control can be switched between internal
speed control and internal torque control.
S/T
Section 3.6.5
Internal torque/position control
change mode
Using input device, control can be switched between internal
torque control and position control.
T/P
Section 3.6.6
Positioning mode
(Point table method) (Note 2)
Positioning operation is performed by selecting 7 point tables
which are set in advance, in accordance with the set value.
Select the point table using an external input signal.
CP
Section 13.3
Positioning mode
(Program method) (Note 2)
Positioning operation is performed by selecting a program from
8 programs which are created in advance.
Select the program using an external input signal.
CL
Section 13.4
Home position return mode (Note 2)
Dog type, count type, data set type, stopper type, home position
ignorance, dog type rear end reference, count type front end
reference, dog cradle type
CP/CL Section 13.6
High-resolution encoder
The servo motor is equipped with high-resolution encoder of
131072 pulses/rev.
P, S, T
CP/CL
Gain changing function
Gains can be changed using an input device or gain changing
conditions (servo motor speed, etc.)
P, S
CP/CL
Section 7.3
Advanced vibration suppression
control
This function suppresses vibration of an arm end or residual
vibration.
P
CP/CL
Section 7.2.4
Adaptive filter II
This function sets the filter characteristics automatically by the
one-touch tuning to suppress vibration of a mechanical system.
P, S
CP/CL
Section 7.2.2
Low-pass filter
This function is effective for suppressing high-frequency resonance
which occurs as the servo system response is increased.
P, S
CP/CL
Section 7.2.5
Electronic gear
Input pulses can be multiplied by 1/50 to 500.
P
Section 4.1.7
Position command can be multiplied by 1/131 to 1000.
Electronic gear setting range can be changed by changing the
number of virtual pulses per servo motor revolution.
CP/CL Section 13.7.1 (3)
One-touch tuning
The gain of the servo amplifier can be adjusted by the push
button on the front panel.
P, S
CP/CL
Section 6.1
Auto tuning
This function optimizes the servo gain automatically as load
applied to the servo motor shaft changes.
P, S
CP/CL
Section 6.3
Position smoothing
Smooth acceleration is enabled in response to input pulse.
P
Section 4.2.3
S-pattern acceleration/
deceleration time constant
Smooth acceleration and deceleration are enabled.
S, T
Section 4.3.2
Parameter
No. PC03
CP/CL
Section 13.7.3 (2)
Parameter
No. PC03
Regenerative option
Regenerative option is used when the built-in regenerative
resistor of the servo amplifier does not have sufficient
regenerative capability for the regenerative power generated.
P, S, T
CP/CL
Section 11.2
Alarm history clear
This function clears alarm history and the number of tough drive
performed.
P, S, T
CP/CL
Parameter
No. PC11
Summary of Contents for MELSERVO-JN Series
Page 31: ... 22 MEMO ...
Page 49: ...2 6 2 INSTALLATION MEMO ...
Page 181: ...5 30 5 DISPLAY AND OPERATION SECTIONS MEMO ...
Page 199: ...6 18 6 GENERAL GAIN ADJUSTMENT MEMO ...
Page 303: ...11 46 11 OPTIONS AND PERIPHERAL EQUIPMENT MEMO ...
Page 351: ...12 48 12 SERVO MOTOR MEMO ...
Page 445: ...13 94 13 POSITIONING MODE MEMO ...