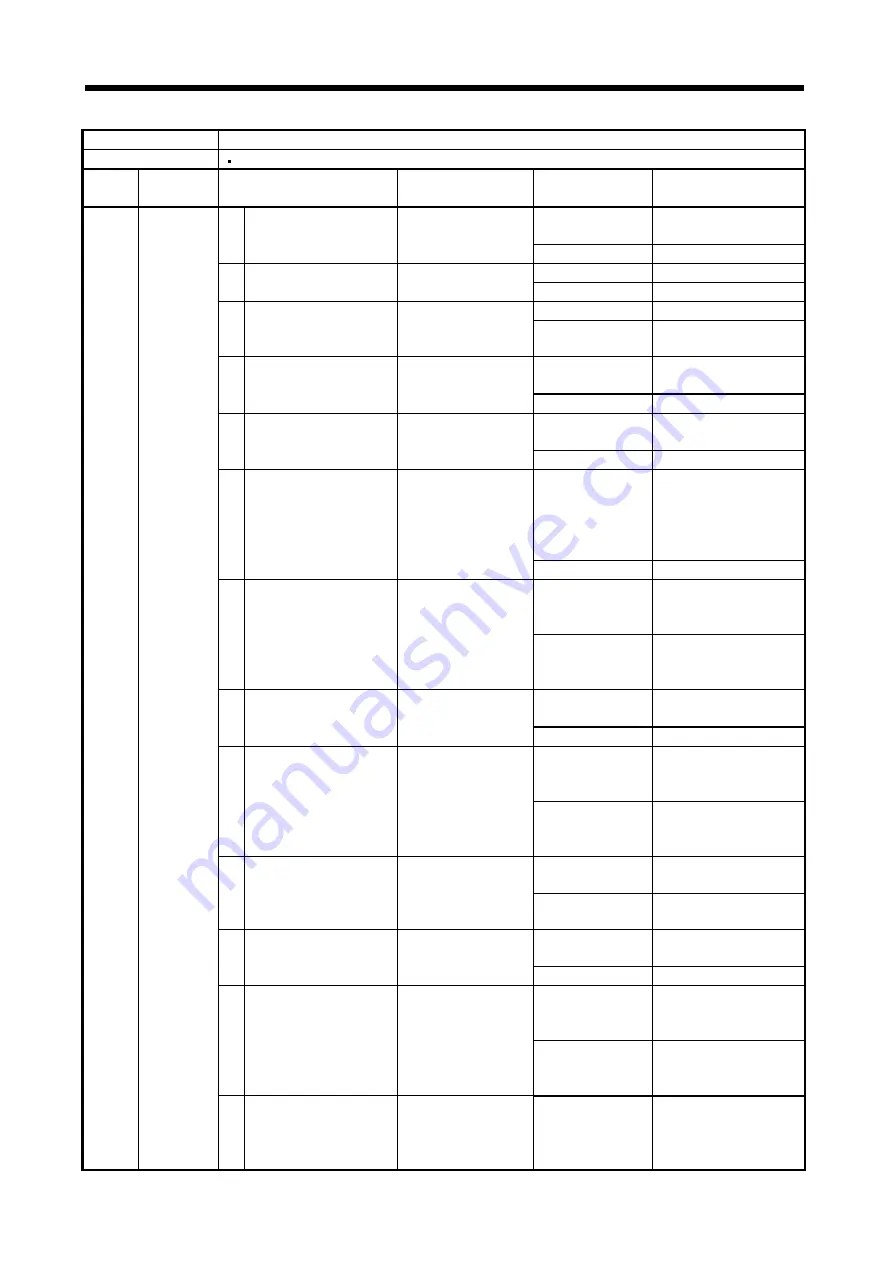
8 - 21
8. TROUBLESHOOTING
Alarm No.: A.52
Name: Error excessive
Description
The droop pulse between the command position and the current position exceeds the alarm level.
Detailed
display
Detailed
Name
Cause
Checking method
Result
Action
52.3
Droop
pulses
excessive
1) Servo motor power cables
are not connected.
(missing phase)
Check the wiring.
Not connected
(missing phase).
Correct the wiring.
No error.
Check 2).
2) Incorrect connection with
the servo motor
Check the wiring of U,
V and W.
Incorrect connection. Correct the wiring.
Correct connection. Check 3).
3) Incorrect connection of the
encoder cable
Check if the encoder
cable is connected
correctly.
Incorrect connection. Correct the wiring.
Correct connection. Check 4).
4) Torque limit value is small. Check the torque limit
value.
Torque limit value is
small.
Increase the torque limit
value.
Normal range
Check 5).
5) The work collided against
the structural part.
Check if the work
collided against the
structural part.
Collided.
Check the operation
pattern.
Did not collide.
Check 6).
6) Torque shortage
Check if the torque is
saturated.
Saturated
Reduce load.
Check operation pattern.
Replace the servo motor
to one that provides larger
output.
Not saturated
Check 7).
7) Servo motor cannot be
started due to torque
shortage caused by power
supply voltage drop.
Check the value of
status display Pn (bus
voltage).
The value is "1"
(undervoltage) or
"2" (low voltage).
Check the power supply
voltage.
The value is "4"
(high voltage) or "5"
(overvoltage).
Check 8).
8) Acceleration/deceleration
time constant is short.
Check if the alarm occurs
after the deceleration time
constant is increased.
Alarm does not
occur.
Check operation pattern.
Alarm occurs.
Check 9).
9) Gain adjustment is not
made well.
Check the load to
motor inertia moment
ratio.
Load to motor inertia
moment ratio is
normal.
Use the manual mode to
make gain adjustment.
Load to motor
inertia moment ratio
is not normal.
Check 10).
10) Estimation of the load to
motor inertia moment ratio
is not estimated well.
Check if the alarm
occurs after changing
the load to motor inertia
moment ratio manually.
Alarm does not
occur.
Check the load to motor
inertia moment ratio.
Alarm occurs.
Check 11).
11) Position loop gain value is
small.
Check if the alarm
occurs after the position
loop gain is changed.
Alarm does not
occur.
Check the position loop
gain.
Alarm occurs.
Check 12).
12) Servo motor is rotated by
external force.
Measure the actual
position on the servo
lock status.
The servo motor is
rotated by an
external force.
Check the machine.
Servo motor is not
rotated by an
external force.
Check 13).
13) Encoder faulty
Check if the alarm
occurs after replacing
with the servo
operating normally.
Alarm does not
occur.
Replace the servo motor.
Summary of Contents for MELSERVO-JN Series
Page 31: ... 22 MEMO ...
Page 49: ...2 6 2 INSTALLATION MEMO ...
Page 181: ...5 30 5 DISPLAY AND OPERATION SECTIONS MEMO ...
Page 199: ...6 18 6 GENERAL GAIN ADJUSTMENT MEMO ...
Page 303: ...11 46 11 OPTIONS AND PERIPHERAL EQUIPMENT MEMO ...
Page 351: ...12 48 12 SERVO MOTOR MEMO ...
Page 445: ...13 94 13 POSITIONING MODE MEMO ...