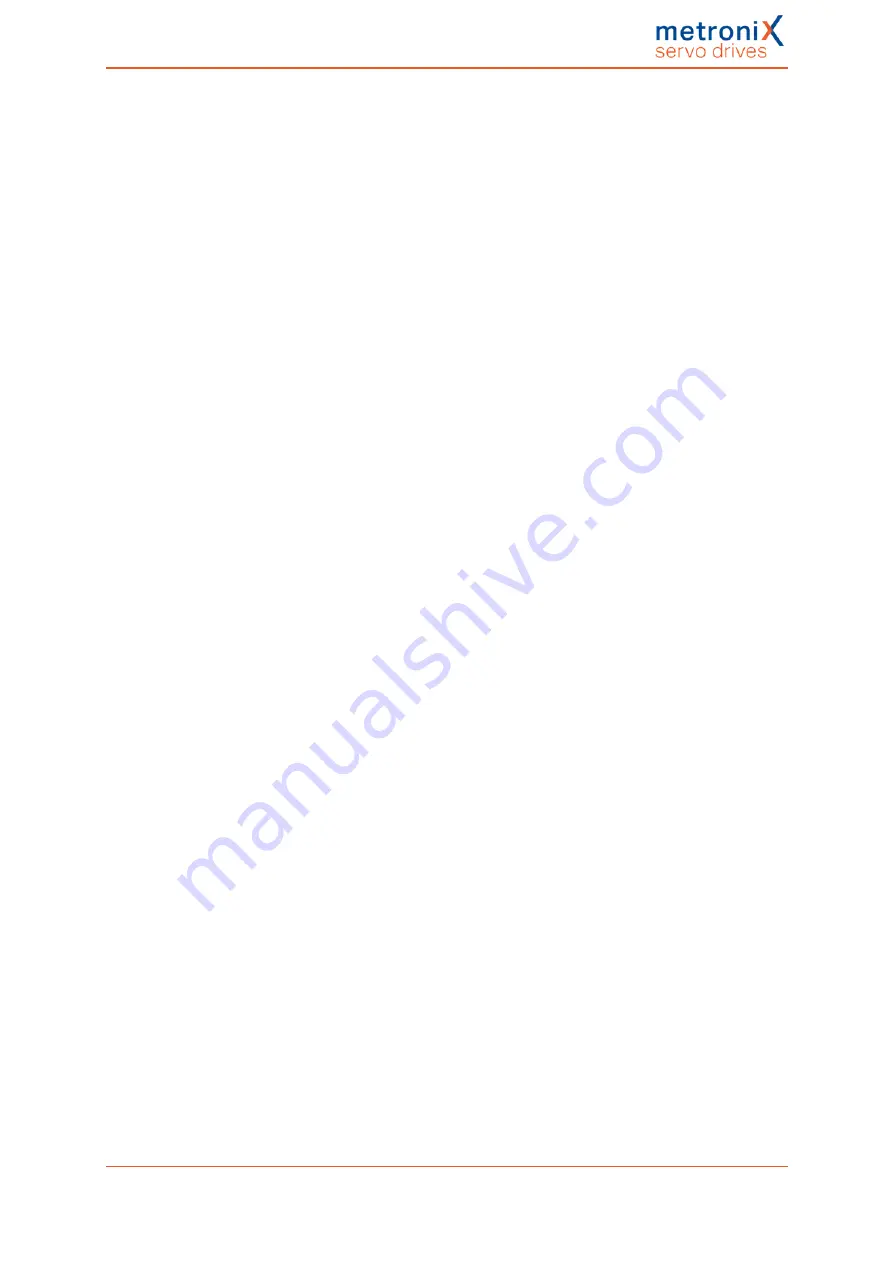
6 Applications
The adaptation to the desired system of units can then be realised by way of the display
units. It is important to select appropriate combinations.
Typical configurations of two encoders (drive/output):
l
Resolver/incremental encoder
l
Resolver/analogue SINCOS encoder
l
Resolver/serial encoder
l
EnDat, Hiperface encoder/incremental encoder X1
If a serial encoder with a parameter set (EnDat/Hiperface) is used at the output, the
commutation data of the encoder parameter set will be suppressed when the firmware is
started. Instead, the commutation data for the main encoder taken from the internal
parameter set of the servo drive will be used.
There must be no slack play between the drive and output. If possible, preloaded
transmissions should be used.
6.3.2
Synchronisation/parameterisation of the master
In master-slave mode, the master emulates an incremental encoder which is described by
the parameters in the menu
Operating mode/Incremental encoder emulation
.
6.3.3
Synchronisation/parameterisation of the slave
In synchronisation mode, the slave must be informed that the angle encoder information
will be provided via the master frequency input X1. This can be done in the command
window where the option
Synchronised
(for position- and speed-synchronous
applications) or
Flying saw
(only flying saw) must be selected:
To fine-tune the synchronous application, click the
Synchronisation wizard
button and
follow the instructions. The settings can also be made manually. The following parameters
must be checked:
l
Selection of the correct encoder configuration under
Operating mode/Encoder
selection
l
Selection of the correct encoder parameters under
Parameters/Device
parameters/Angle encoder settings
l
Selection of the correct setpoint management (e.g. for speed-controlled operation)
under
Operating mode/Setpoint selection
l
Selection of the correct position sets (for flying saw: synchronous or not) under
Parameters/Positioning/Destination parameters
Product manual BL 4000-C
Page 106 of 298