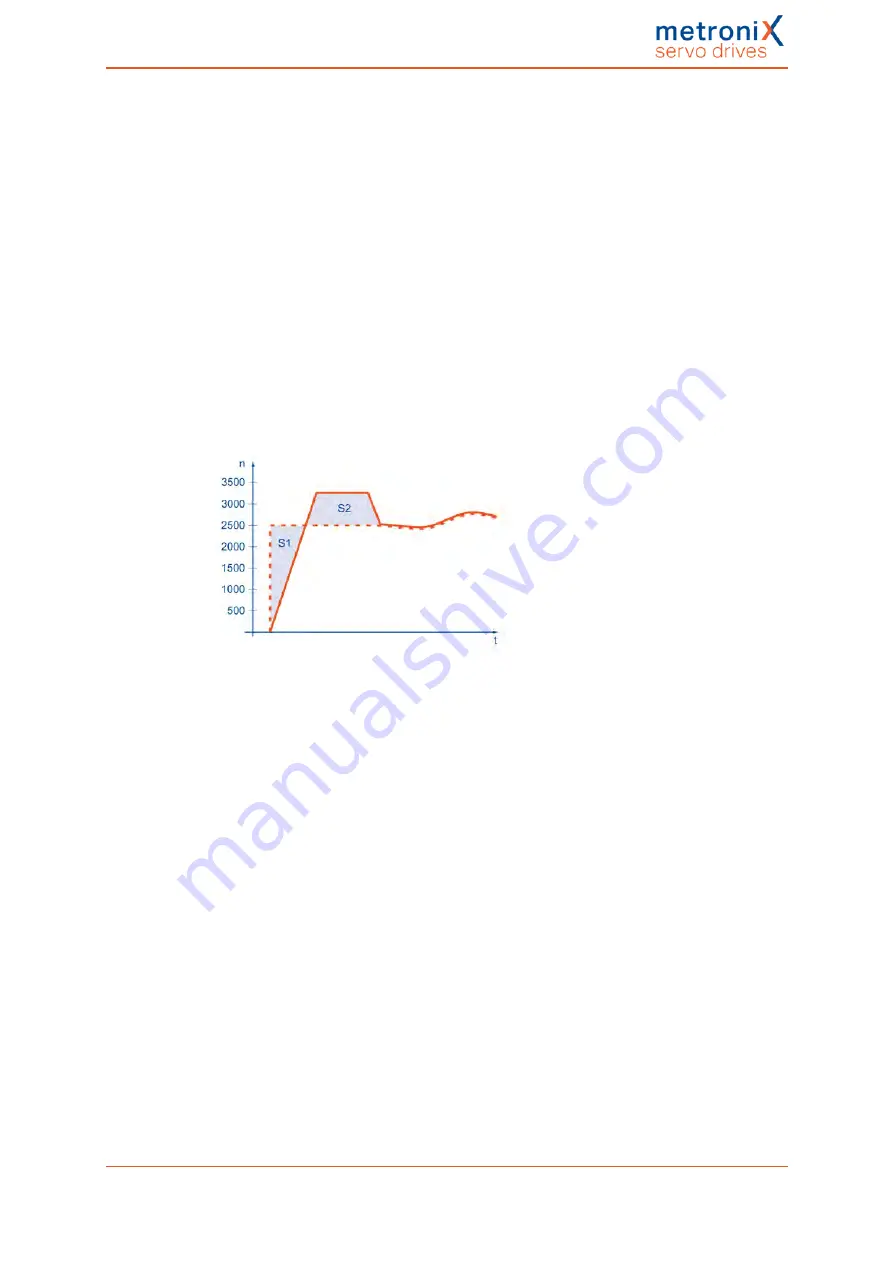
6 Applications
6.4.1
Conventional synchronisation
An external setpoint position can be specified for the servo drive via the master frequency
input. This position will be converted by way of a certain factor (electronic transmission) in
the synchronisation unit.
In the
Synchronised
mode (command window), this setpoint is directly supplied. The
synchronisation activation and deactivation is possible at any time by applying or
removing the synchronous position signal. However, if the synchronisation is activated or
deactivated while the motor is running, the abrupt setpoint change causes a rather strong
jerk. The maximum acceleration that occurs during this process is limited only by the
maximum motor current. The resulting thrust can lead to strong oscillations which may
damage the system. Since the servo drive can follow the abrupt setpoint change only
slowly, rather large, temporary following errors result. This is why activating the
synchronisation while the motor is running is not permissible in most cases.
In the
Flying saw
mode, the synchronisation activation and deactivation is performed
during a positioning run. As a result, there will be no abrupt setpoint change.
Figure 61: Synchronisation process
The servo drive follows the synchronous position signal with a delay in compliance with
the acceleration and maximum excess speed specified in the position set. This leads to a
position difference (area S1) that the servo drive makes up for in a controlled and defined
manner and without a following error (area S2).
In addition, relative or absolute distances S can be taken into consideration for the
positioning process. In this case, the following is true for S2: S2 = S1 + S
Product manual BL 4000-C
Page 109 of 298