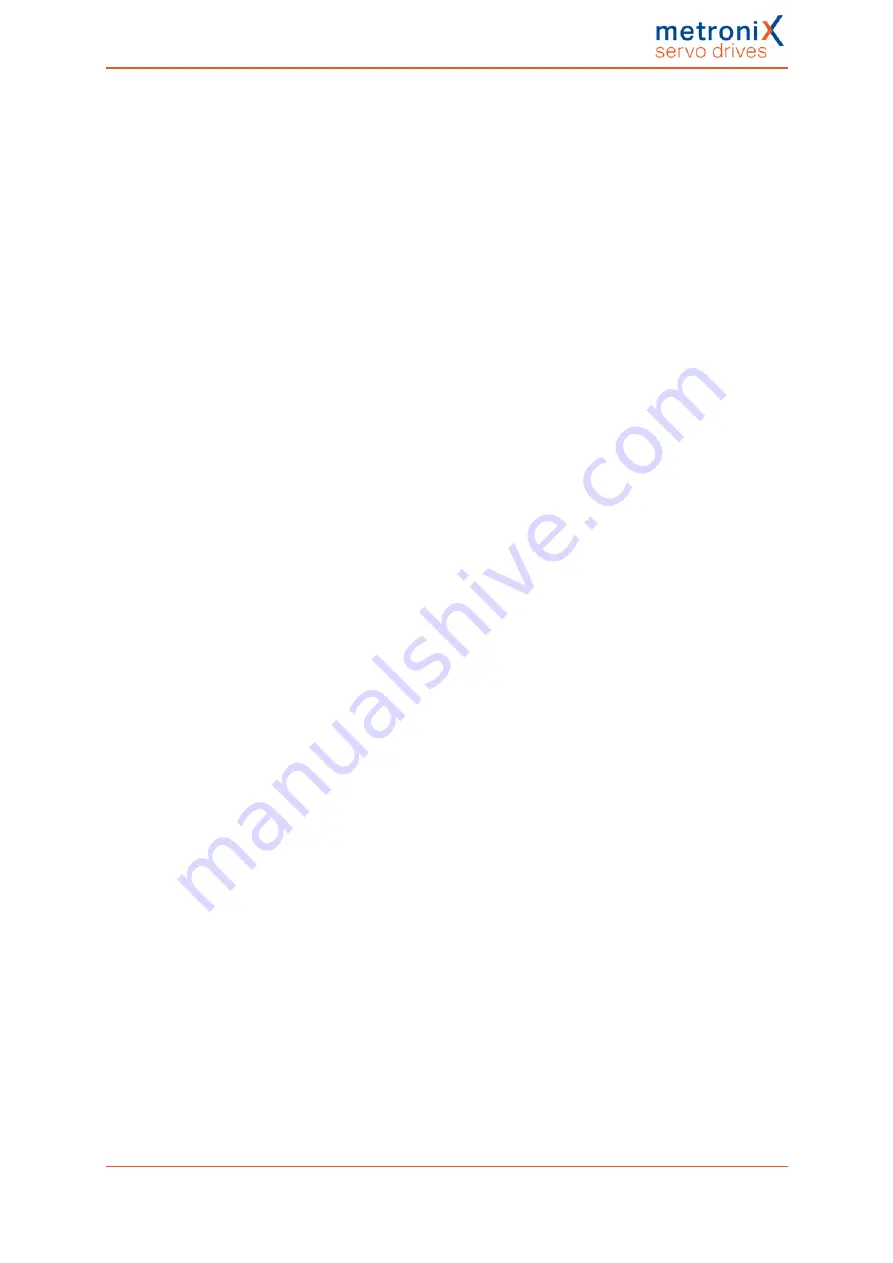
7 Additional settings
7.6
Parameterisation of the motor and output
stage
7.6.1
Methods for analysing motor problems
In most cases, motor problems are indicated by noise and poor concentricity. In a first
step, the internal oscilloscope should be used to analyse the current ripple, for example at
100 rpm. A little ripple caused by unbalance must always be expected due to the design of
the motor (10-20%). Good motors with a sinusoidal EMF show hardly any visible current
ripple at all.
Insidious winding defects can be detected by way of the following methods:
l
Measure the ohmic resistance and inductance of the armature winding. To do so,
simply disconnect the motor connector from the servo drive and connect the
measuring instrument to the cable at the motor side. The values should be nearly
identical (max. difference 10%). If the resistance values differ strongly from one
another, the winding is damaged, and the motor must be replaced. The design and
rating of the drive must also be verified.
l
A so-called coast-down test can be performed to see whether the EMF (induced
voltage of the 3 phases) is sinusoidal and symmetric. To do so, connect an
external oscilloscope with differential voltage probes to the motor phases.
Accelerate the drive to approx. 3,000 rpm, and then switch the power section to
passive, e.g. by activating the STO function or by switching off the mains power
supply. As a result, the motor supplies an induced voltage (oscilloscope) that
should match the specifications on the data sheet. It must be identical for all of the
phases.
For an optimum configuration and adaptation of the control system to the mass that needs
to be moved, a high force/mass ratio would be beneficial. As this ratio is not ideal in the
case of so-called direct drives, the control quickly becomes instable.
Direct drives (examples):
l
A torque motor without a transmission connected to a heavy, large-diameter rotary
table.
l
A motor shaft that is directly coupled to a load with a high mass. A gear on a motor
shaft that engages with a toothed rack to move a large slide.
When adapting the control system in such a case, the following is recommended:
l
Use an encoder with a high resolution.
l
Increase the gain of the speed controller up to the oscillation limit.
l
Decrease the gain and correction speed of the position controller.
l
Decrease the acceleration values of the position set.
l
Activate and adapt the torque feedforward of the position set.
Product manual BL 4000-C
Page 153 of 298