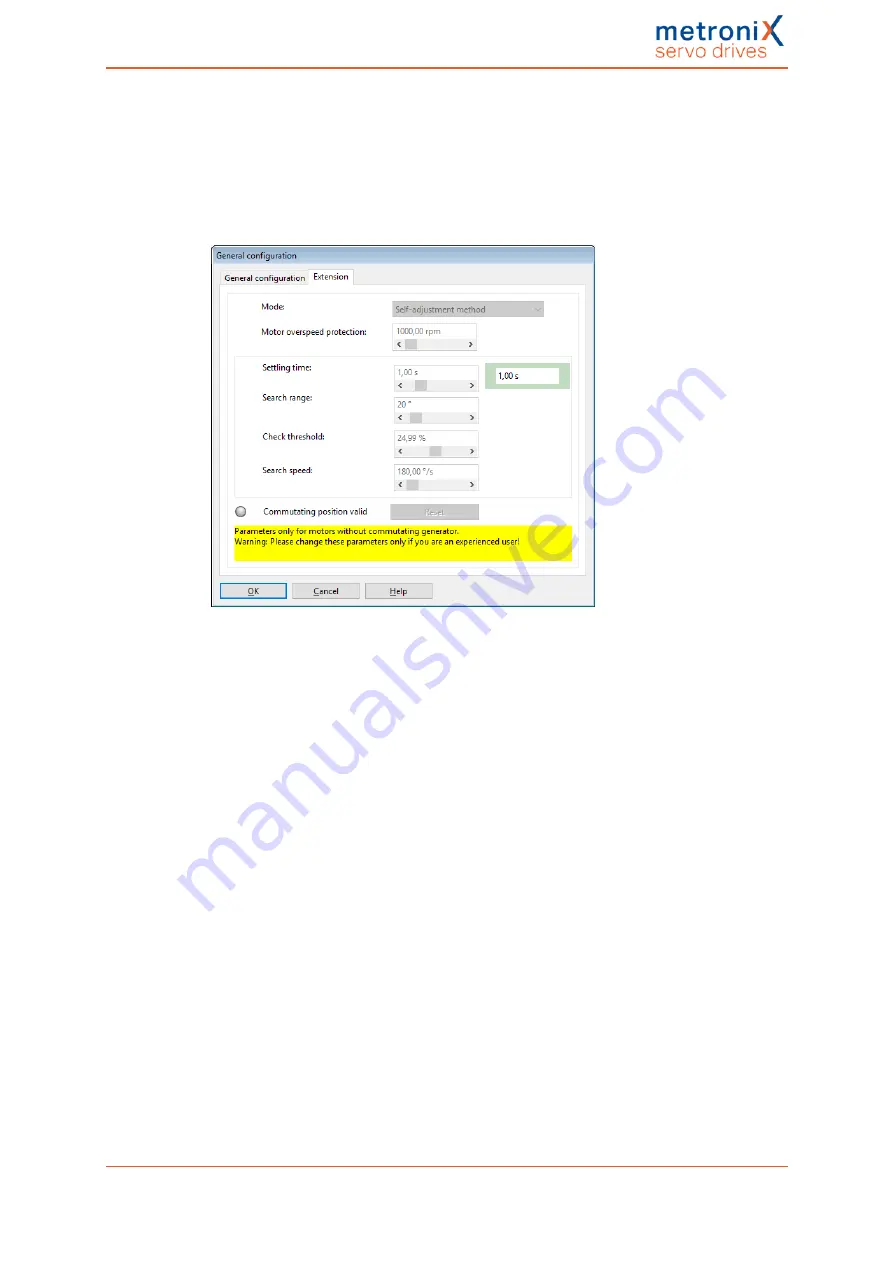
4 Quick-start guide
In the case of the encoders mentioned hereinabove, it is only necessary to adjust the
offset angle during the commissioning process.
If you do not have a motor with commutation signals, the commutation position must be
determined. This will be done whenever the servo drive is started. There are different
methods to choose from. They differ from one another by the specific required movement
and by the specific boundary conditions, e.g. the physical characteristics of the drive.
Figure 10: "General configuration" window - "Extension" tab
Self-adjustment method
With this method, the drive moves over the double search range in a controlled manner.
Depending on the initial position, the drive may jerk. This method is not suitable for vertical
axes.
Reaction method (recommended)
This method is suitable for all types of drives without a braking system. It is suitable for
horizontal and vertical applications. Only minimal mobility (the system is more or less
motionless) is sufficient for determining the commutation position.
Saturation method
This method is not suitable for air-core drives. It requires a braked drive as the drive must
be absolutely motionless during the determination of the commutation position. It is
suitable for horizontal and vertical applications.
Commutation position valid
LED
It indicates that the determination of the commutation position has been successful. This
status will be reset, e.g. if an angle encoder error occurs.
It is only relevant for motors with angle encoders without any commutation signal.
Product manual BL 4000-C
Page 43 of 298