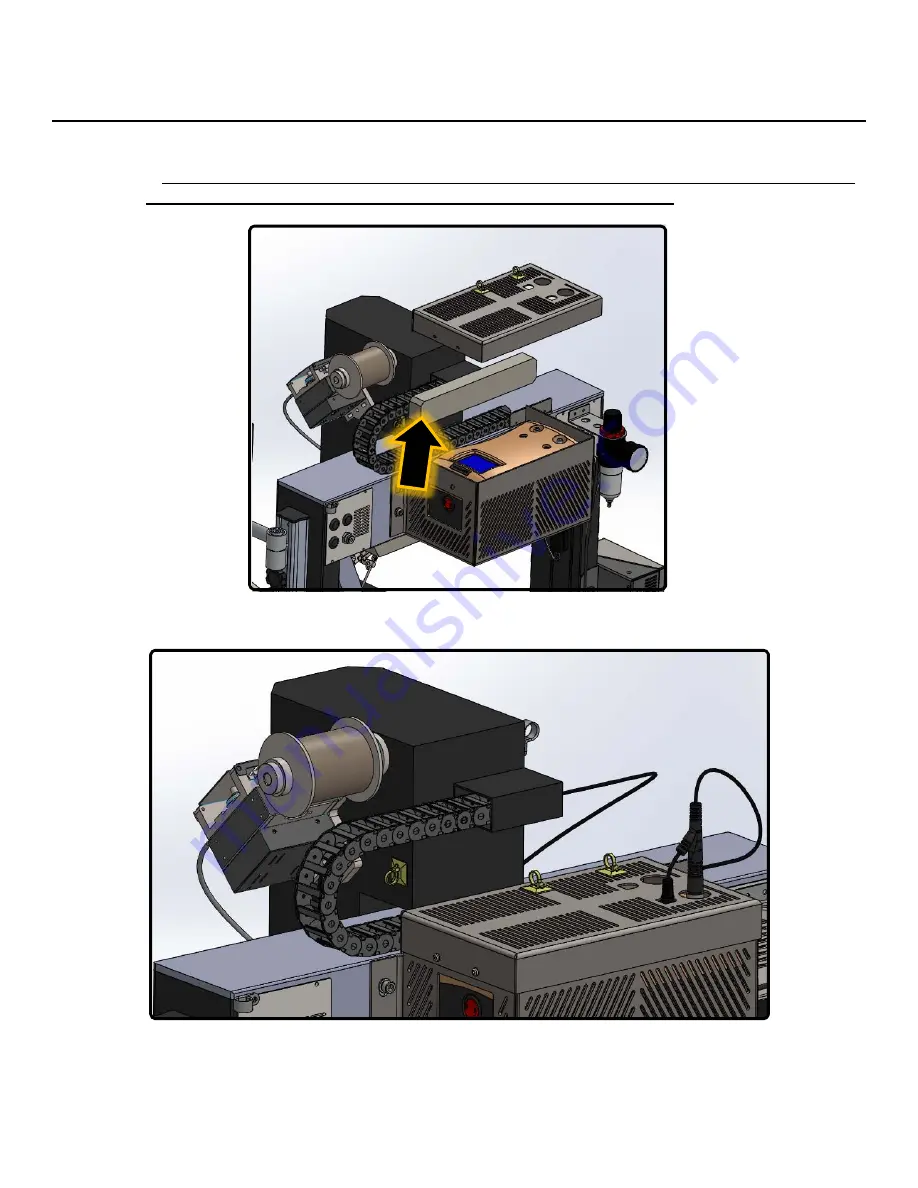
USER MANUAL, RSS-1000-CVSI
7000-5970
Rev.
A
page
19
of
396
7.5. Connection Validation Housing
7.5.1. Warning: Failure to remove foam from Connection Validation Housing may result
in the overheating of the Connection Validation Power Supply
8. Replace Connection Validation Housing Cover once foam is removed
Unboxing Complete!
Summary of Contents for RSS-1000-CVSI
Page 21: ...USER MANUAL RSS 1000 CVSI 7000 5970 Rev A page 21 of 396 ROBOT BASE CONNECTIONS N ...
Page 52: ...USER MANUAL RSS 1000 CVSI 7000 5970 Rev A page 52 of 396 2 Tap the Power Button ...
Page 55: ...USER MANUAL RSS 1000 CVSI 7000 5970 Rev A page 55 of 396 2 Tap the Power Button ...
Page 224: ...USER MANUAL RSS 1000 CVSI 7000 5970 Rev A page 224 of 396 5 5 Spiral 1 2 3 8 9 4 7 6 5 ...