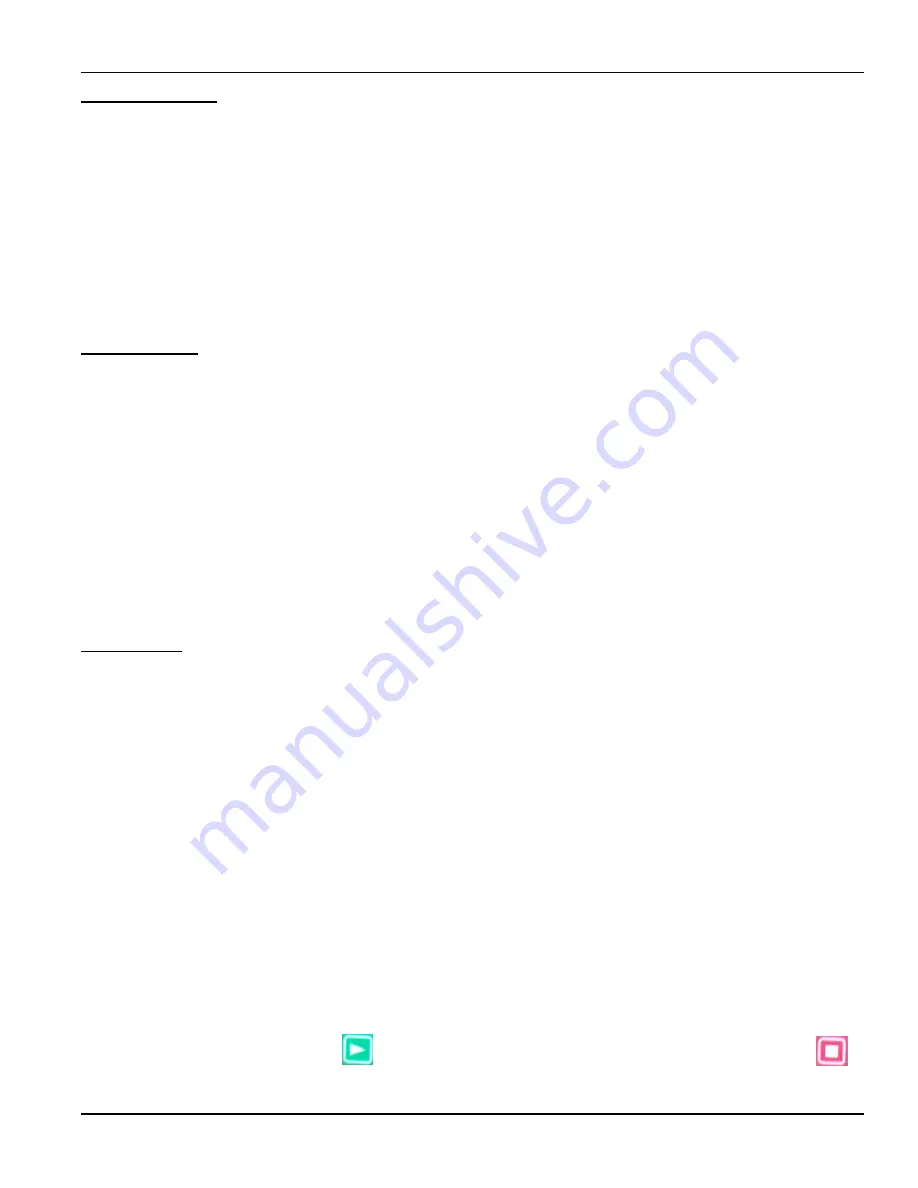
DIGISPENSE 3020 CONTROLLER MODULE
Page 3-9
7 April, 2011
IVEK Corp.
P03L011B
3.1.8 Acceleration
The Acceleration setting determines how quickly the pump piston reaches the dispense/load rate from a stopped position. It
is also used to determine deceleration; how quickly the piston slows down when heading towards stop. Increasing the
acceleration may help increase the shearing of certain fluids from the tip improving repeatability. However, with higher
accelerations, high viscosity fluids may be more susceptible to causing the Actuator Module motor to stall.
Advantages
Disadvantages
Decreased Acceleration
Lower probability of stalls
Less shear at tip
Lower probability of fluid cavitations
Slightly longer cycle time
Increased Acceleration
More shear at tip
Higher probability of stalls
Slightly shorter cycle time
Higher probability of fluid cavitations
3.1.9 Drawback
Drawback is provided in some operating modes (Dispense, Dispense MCV, Meter) to allow the fluid to move in the
opposite direction after a dispense to better separate the fluid at the tip. Often, high viscosity or “stringy” fluids are
susceptible to poor separation at the end of a dispense. Drawback provides a snapping motion in the fluid to attempt
to shear it off at the tip. There are three parameters available for configuration of Drawback: Drawback Volume,
Drawback Rate, and Drawback Dwell.
The Drawback Volume determines the amount of fluid to move backwards after a dispense. Typically, this is
configured for a small fraction of the dispense volume.
The Drawback Rate determines the rate of fluid movement during the backwards drawback.
The Drawback Dwell determines the amount of time the fluid movement pauses between the end of the cycle and the
beginning of the next cycle. Typically, this is left at the default value, but may be increased if it benefits the application.
3.1.10 Torque
The torque setting determines the peak current available to the motor. Increasing the torque decreases the
probability of stalling with high viscosity fluids. Decreasing the torque increases efficiency by decreasing steady state
heat loss in the motor when using low viscosity fluids.
Advantages
Disadvantages
Decreased Torque
Reduced heat loss in the motor
Higher probability of stalls
Increased Torque
Lower probability of stalls
Increased heat loss in the motor
3.2
STANDARD OPERATION
This Standard Operation section provides the information and instructions for the most common operation of the
system. Most of the screens and the less common information have been removed. If you are an advanced user or
need additional information please refer to Section 3.3 - Advanced Operation.
The Controller Module provides the controls for producing fluid flow via a positive displacement pumping mechanism.
The systems utilize solid-state electronics, stepping motor drives, and precision machined ceramic pump heads.
These components combine to provide exceptional accuracy and precision, high reliability, and low maintenance.
Volume commands for the Controller Module use microliters. Rate commands are in microliters per second. Pumping
is started using the Start push-button
based on the screen being viewed. Push the Stop push-button
to
stop the operation before the respective volume setting is reached.