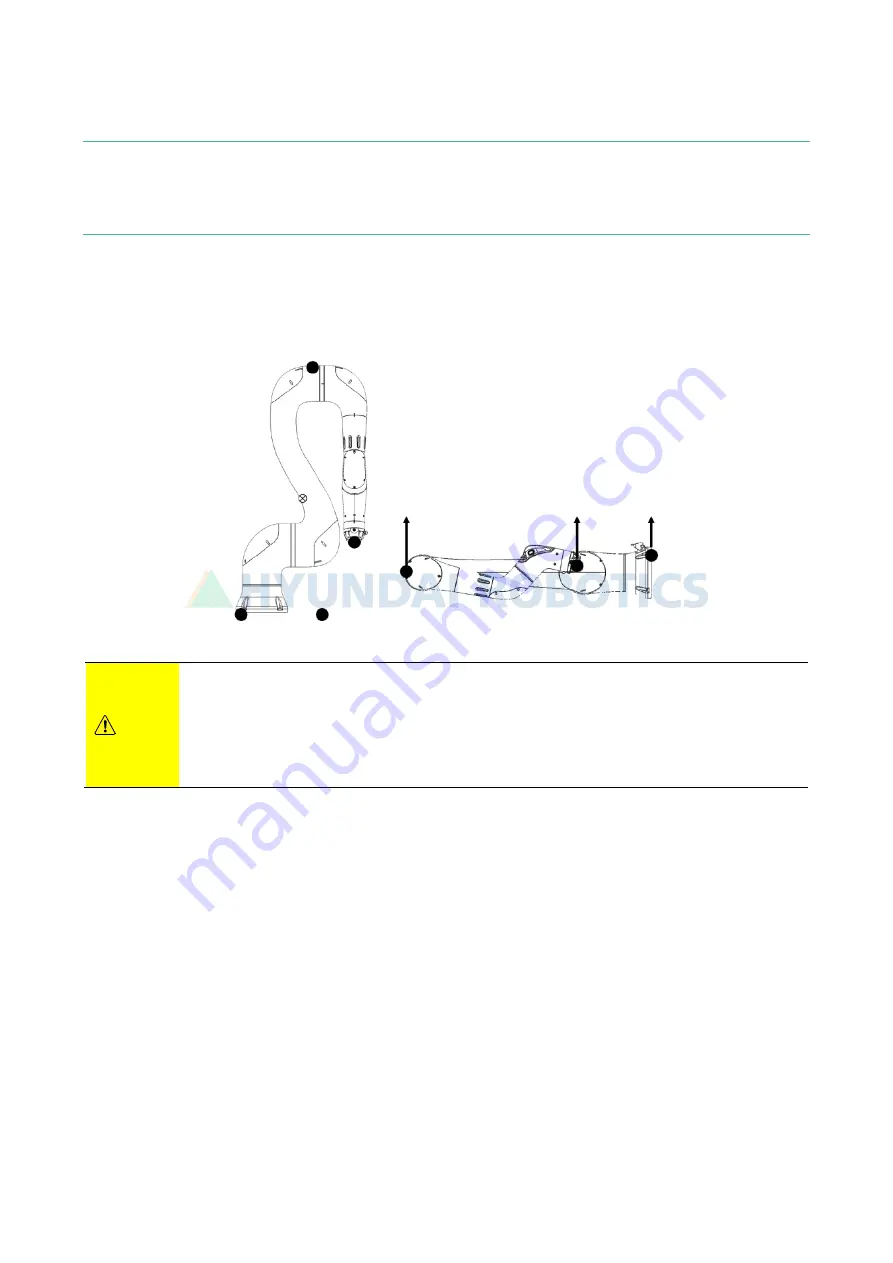
Hyundai Robotics
78
_Moving and storing | Moving method
Hyundai Robotics
5.
Moving and storing
This section describes the proper methods for moving and storing the collaborative robot.
5.1
Moving method
Check the weight and precautions for the collaborative robot, move it by the proper method, paying attention to
safety.
To move the collaborative robot manually, set it at the posture adequate for moving, and two or more workers lift
it at the same time, and move it to the target location.
Figure 41 Manual moving
Caution
To move the collaborative robot manually, two or more workers should lift it at the same time,
and move it.
When two or more workers move it at the same time, connections may be damaged.
Therefore, take care not to damage them.
Putting down the collaborative robot at it is on a floor, the frame cover may be damaged.
To move the collaborative robot by means of a crane, set the robot at the posture adequate for lifting, connect it to
the crane with sling belts, lift it, and move it to the target location.
Holding points