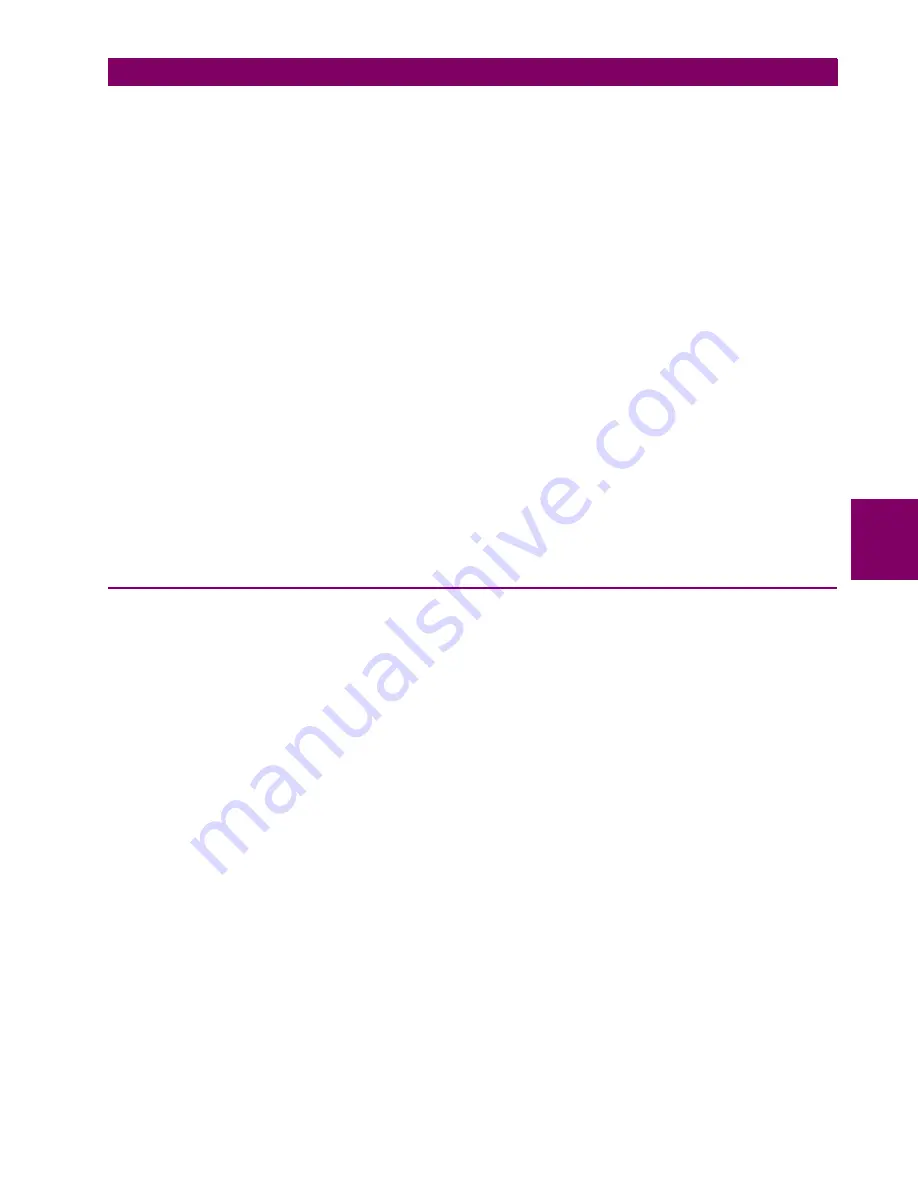
GE Multilin
M60 Motor Protection System
5-5
5 SETTINGS
5.1 OVERVIEW
5
•
PICKUP setting:
For simple elements, this setting is used to program the level of the measured parameter above or
below which the pickup state is established. In more complex elements, a set of settings may be provided to define the
range of the measured parameters which will cause the element to pickup.
•
PICKUP DELAY setting:
This setting sets a time-delay-on-pickup, or on-delay, for the duration between the pickup
and operate output states.
•
RESET DELAY setting:
This setting is used to set a time-delay-on-dropout, or off-delay, for the duration between the
Operate output state and the return to logic 0 after the input transits outside the defined pickup range.
•
BLOCK setting:
The default output operand state of all comparators is a logic 0 or “flag not set”. The comparator
remains in this default state until a logic 1 is asserted at the RUN input, allowing the test to be performed. If the RUN
input changes to logic 0 at any time, the comparator returns to the default state. The RUN input is used to supervise
the comparator. The BLOCK input is used as one of the inputs to RUN control.
•
TARGET setting:
This setting is used to define the operation of an element target message. When set to
“
Disabled
”
,
no target message or illumination of a faceplate LED indicator is issued upon operation of the element. When set to
“Self-Reset”, the target message and LED indication follow the operate state of the element, and self-resets once the
operate element condition clears. When set to “Latched”, the target message and LED indication will remain visible
after the element output returns to logic 0 until a RESET command is received by the relay.
•
EVENTS setting:
This setting is used to control whether the pickup, dropout or operate states are recorded by the
event recorder. When set to “Disabled”, element pickup, dropout or operate are not recorded as events. When set to
“Enabled”, events are created for:
(Element) PKP (pickup)
(Element) DPO (dropout)
(Element) OP (operate)
The DPO event is created when the measure and decide comparator output transits from the pickup state (logic 1) to
the dropout state (logic 0). This could happen when the element is in the operate state if the reset delay time is not 0.
5.1.3 INTRODUCTION TO AC SOURCES
a) BACKGROUND
The M60 may be used on systems with breaker-and-a-half or ring bus configurations. In these applications, each of the two
three-phase sets of individual phase currents (one associated with each breaker) can be used as an input to a breaker fail-
ure element. The sum of both breaker phase currents and 3I_0 residual currents may be required for the circuit relaying
and metering functions. For a three-winding transformer application, it may be required to calculate watts and vars for each
of three windings, using voltage from different sets of VTs. These requirements can be satisfied with a single UR, equipped
with sufficient CT and VT input channels, by selecting the parameter to measure. A mechanism is provided to specify the
AC parameter (or group of parameters) used as the input to protection/control comparators and some metering elements.
Selection of the parameter(s) to measure is partially performed by the design of a measuring element or protection/control
comparator by identifying the type of parameter (fundamental frequency phasor, harmonic phasor, symmetrical component,
total waveform RMS magnitude, phase-phase or phase-ground voltage, etc.) to measure. The user completes the process
by selecting the instrument transformer input channels to use and some of the parameters calculated from these channels.
The input parameters available include the summation of currents from multiple input channels. For the summed currents of
phase, 3I_0, and ground current, current from CTs with different ratios are adjusted to a single ratio before summation.
A mechanism called a
source
configures the routing of CT and VT input channels to measurement sub-systems. Sources,
in the context of UR series relays, refer to the logical grouping of current and voltage signals such that one source contains
all the signals required to measure the load or fault in a particular power apparatus. A given source may contain all or some
of the following signals: three-phase currents, single-phase ground current, three-phase voltages and an auxiliary voltage
from a single VT for checking for synchronism.
To illustrate the concept of sources, as applied to current inputs only, consider the breaker-and-a-half scheme below. In this
application, the current flows as shown by the arrows. Some current flows through the upper bus bar to some other location
or power equipment, and some current flows into transformer winding 1. The current into winding 1 is the phasor sum (or
difference) of the currents in CT1 and CT2 (whether the sum or difference is used depends on the relative polarity of the CT
connections). The same considerations apply to transformer winding 2. The protection elements require access to the net
current for transformer protection, but some elements may need access to the individual currents from CT1 and CT2.
Summary of Contents for M60 UR Series
Page 10: ...x M60 Motor Protection System GE Multilin TABLE OF CONTENTS ...
Page 128: ...4 30 M60 Motor Protection System GE Multilin 4 3 FACEPLATE INTERFACE 4 HUMAN INTERFACES 4 ...
Page 410: ...5 282 M60 Motor Protection System GE Multilin 5 10 TESTING 5 SETTINGS 5 ...
Page 440: ...6 30 M60 Motor Protection System GE Multilin 6 5 PRODUCT INFORMATION 6 ACTUAL VALUES 6 ...
Page 452: ...7 12 M60 Motor Protection System GE Multilin 7 2 TARGETS 7 COMMANDS AND TARGETS 7 ...
Page 462: ...9 8 M60 Motor Protection System GE Multilin 9 2 BATTERIES 9 MAINTENANCE 9 ...
Page 474: ...A 12 M60 Motor Protection System GE Multilin A 1 PARAMETER LISTS APPENDIX A A ...
Page 584: ...B 110 M60 Motor Protection System GE Multilin B 4 MEMORY MAPPING APPENDIX B B ...
Page 614: ...C 30 M60 Motor Protection System GE Multilin C 7 LOGICAL NODES APPENDIX C C ...
Page 630: ...E 10 M60 Motor Protection System GE Multilin E 1 IEC 60870 5 104 PROTOCOL APPENDIX E E ...
Page 642: ...F 12 M60 Motor Protection System GE Multilin F 2 DNP POINT LISTS APPENDIX F F ...
Page 644: ...G 2 M60 Motor Protection System GE Multilin G 1 RADIUS SERVER CONFIGURATION APPENDIX G G ...
Page 652: ...H 8 M60 Motor Protection System GE Multilin H 3 WARRANTY APPENDIX H H ...
Page 662: ...x M60 Motor Protection System GE Multilin INDEX ...