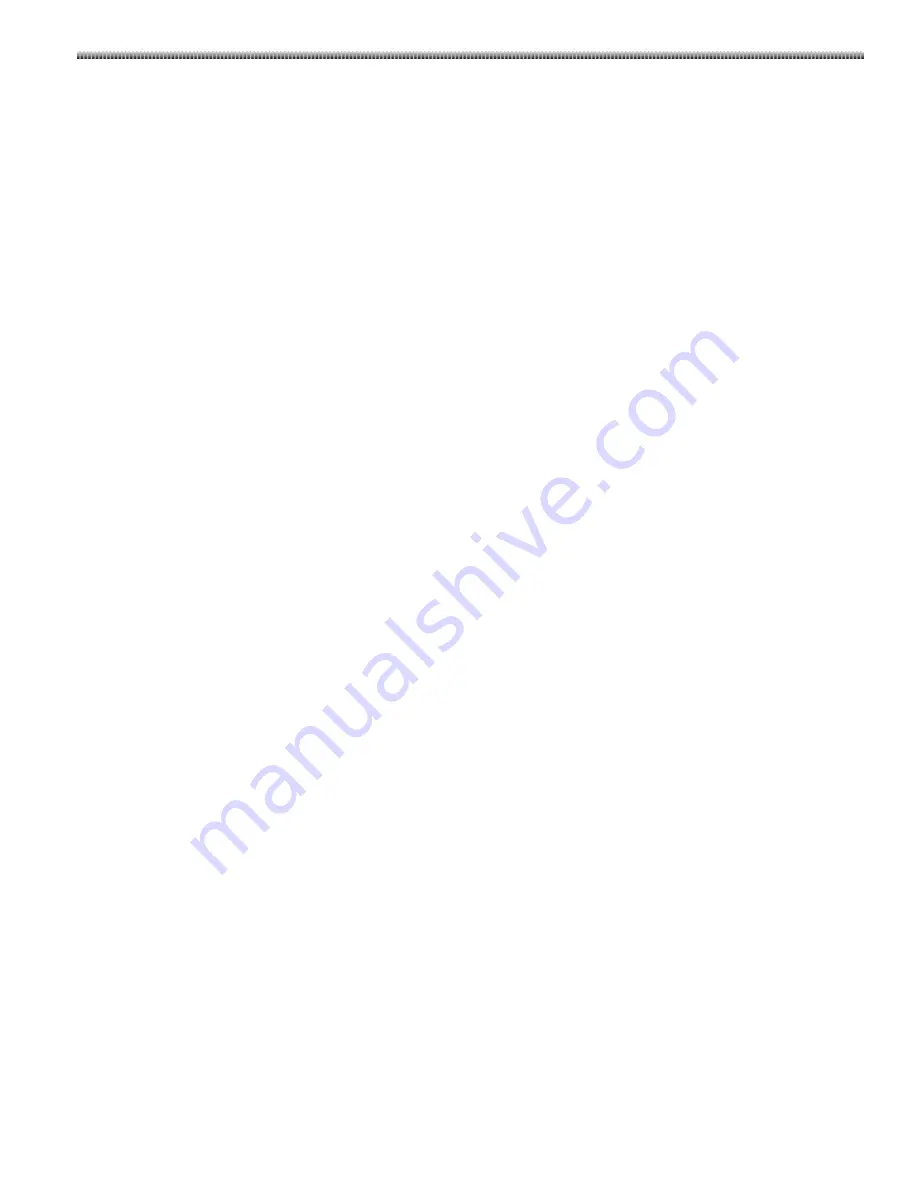
System Overview
2-51
-
Dual Source/Sink Outputs: ±400 mA Peak
The switch frequency is 40KHz for X-ray generator. So the SG3525 should provide 40KHz PWM signal.
Frequency is determined by adjusting the resistor connected with pin6 and capacitor connected with pin5.
At this pin5 80KHz swath wave should be observed in oscillograph.
The pin2 inputs variable voltage signal. Then this voltage signal enters the comparator through internal
amplifier and generators PWM signal.
PI ADJUSTOR
X-ray generator provides stable kV when exposure. It needs to use feedback control to stabilized the output
kV. PI adjustor is usually using at feedback control. There are 2 PI adjustors in kV control board, voltage PI
adjustor and current PI adjustor.
Voltage PI adjustor consists of amplifier U6-2 and resistor R28, R35, R50, R32, capacitor C27, C31,. Before
entering the PI adjustor the set kV value subtracts the feedback kV value to send out error signal. This signal
is sent to voltage PI adjustor.
Current PI adjustor consists of amplifier U6-1 and resistor R44, R46, R47, capacitor C29, C30. The output
signal from voltage PI adjustor subtracts the feedback current of inverter output to send out error signal.
This signal is sent to current PI adjustor. Then the PI adjustor carries out the voltage signal and enters PWM
generator SG3525.
IGBT DRIVER
KV control board consists of IGBT driver circuit. Usually the IGBT driver circuit must be insulated with control
circuit and it still needs several independent power for IGBT gate driver. Agilent IC HCPL-316J is a highly
Integrated power control device that incorporates all the necessary components for a complete, isolated
IGBT gate drive circuit with fault protection and feedback into one SO-16 package. TTL input logic levels
allow direct interface with a microcontroller, and an optically isolated power output stage drives IGBTs with
power ratings of up to 150 A and 1200 V. A high speed internal optical link minimizes the propagation delays
between the micro-controller and the IGBT while allowing the two systems to operate at very large common
mode voltage differences that are common in industrial motor drives and other power switching
applications. The feather is as follows.
-
Drive IGBTs up to IC = 150 A, VCE = 1200 V
-
Optically Isolated, FAULT Status Feedback
-
SO-16 Package
-
CMOS/TTL Compatible
-
500 ns Max. Switching Speeds
For the independent driver power supply kV control board consists of 4 channel independent power. Each
channel can provide DC+18V and DC–4.7V power for HCPL-316J. Those DC power is rectified from AC power.
The power interface connector is KJ7. It connected with driver power transformer.
PROTECT CIRCUIT
KV control board designed 6 protect circuits to protect the X-ray generator. KV lower protect circuit, kV
higher protect circuit, Over current protect circuit, IGBT error protect circuit. DC bus error protect circuit, kV
unbalance protect circuit.
According to generator design requirement the kV output value range is 40kV-110kV. This kV board set
protect circuit point is 25kV. That is if the kV value is lower than 25kV when X-ray generator is running the
exposure can be disable. The kV control board drawing shows the protect circuit. When kV feedback signal
KVT is higher than reference value in U10-1 the STOP signal is activated. At the same time led DS4 lightens.
This protect circuit is enable after a time of 6ms which made by resistor R74 and capacitor C47 after giving
the exposure command.
Summary of Contents for Brivo OEC 715
Page 2: ......
Page 19: ...Chapter1 Introduction and Safety...
Page 41: ...Introduction and Safety 23 46 54 20 18 26...
Page 55: ...Chapter2 System Overview...
Page 137: ...Chapter3 Installation...
Page 212: ...Chapter4 Calibration...
Page 275: ...Brivo OEC 715 785 865 Mobile C Arm X Ray Product Service Manual 4 64...
Page 284: ...Chapter5 Software...
Page 326: ...Software 5 43 2 Click on install to continue 3 Click Next to continue...
Page 335: ...Chapter6 Troubleshooting...
Page 408: ...Chapter7 Replacement...
Page 418: ...Replacement 7 11 166...
Page 488: ...Chapter8 Periodic Maintenance...
Page 502: ...Periodic Maintenance 8 15...
Page 505: ...Chapter9 Technical Reference...
Page 521: ...Technical Reference 9 17 Vertical configuration 1 5m Vertical configuration 1m...
Page 526: ...11 Appendix System Schematics...