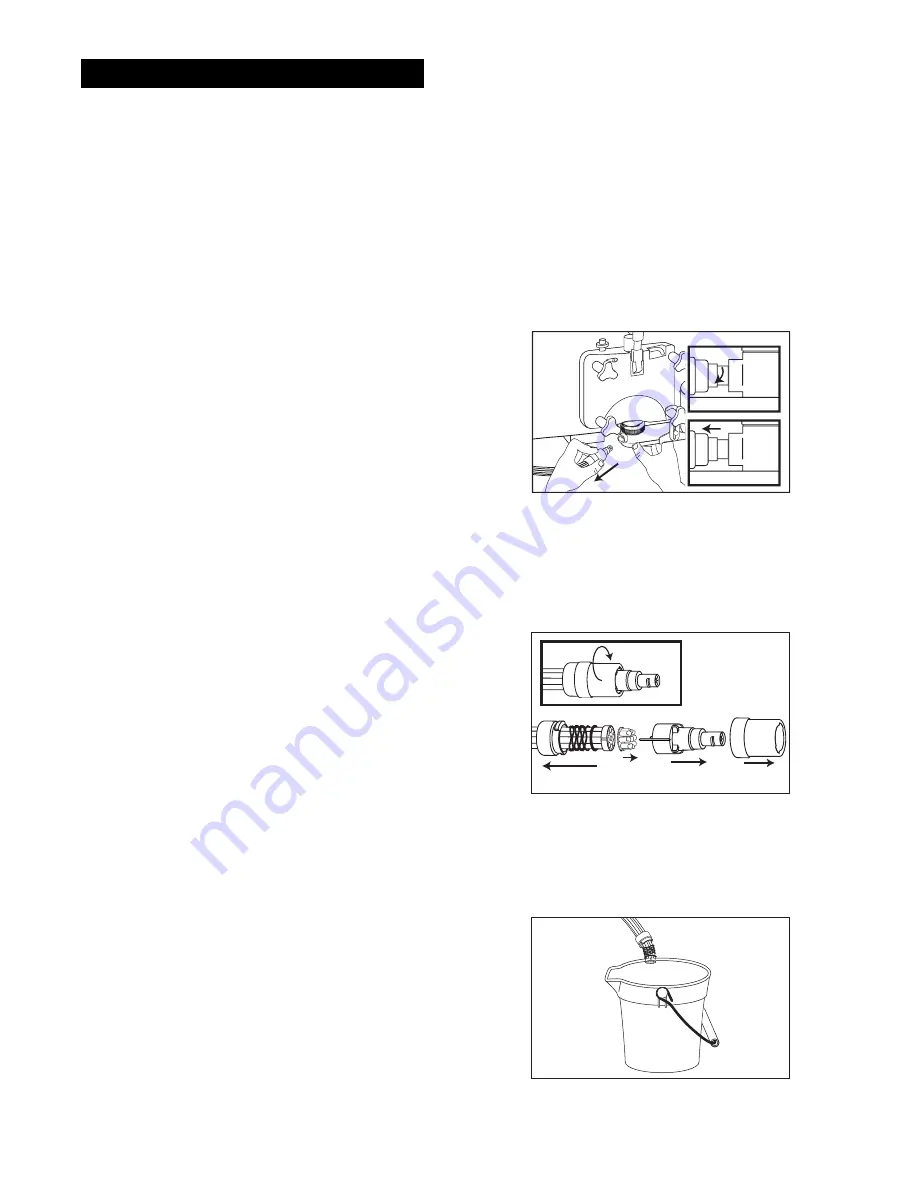
36
The following procedures are performed less
frequently than daily or as needed.
NOTE:
YOUR HANDS SHOULD BE CLEANED
AND SANITIZED BEFORE YOU PERFORM
THE FOLLOWING PROCEDURES.
NOTE:
THE FOLLOWING PROCEDURES
REQUIRE APPROVED, SERVICEABLE AND
SANITIZED TOOLS AND BRUSHES.
CONTACT YOUR LOCAL DISTRIBUTOR FOR
RECOMMENDED SUPPLIES.
NOTE:
USE AN APPROVED CLEANER AND
SANITIZER FOR THE FOLLOWING
PROCEDURES. REFER TO
MANUFACTURER’S INSTRUCTIONS FOR
PROPER PREPARATIONS OF THESE
CLEANING AGENTS.
NOTE:
INSPECT ALL WEAR ITEMS AND
REPLACE IF NECESSARY.
NOTE:
OPERATE UNIT UNDER NORMAL
AMBIENT TEMPERATURES BETWEEN 60
AND 80 DEGREES FAHRENHEIT. UNIT
SHOULD NEVER BE EXPOSED TO
FREEZING TEMPERATURES.
Clean-In-Place (CIP) Procedure
The Clean-In-Place procedure should be
performed every 30 days to ensure that the
syrup passageways are free of any product
crystallization. The medium used for this
process must be an approved sanitizing product
mixed according to the product manufacturer’s
instructions.
This Clean-In-Place procedure is detailed in
four phases:
(1) Prep
(2) Flush
(3) Clean
(4) Reassemble
To ensure maximum results, the following
instructions should be completed in sequence
as stated. This will expose the system and
parts to the sanitizing medium for about 130
minutes.
CIP - Phase 1: Prep
1. Mix approved detergent with warm water
according to manufacturer’s instructions.
2. Ensure the Sanitizer Tank is filled with fresh
approved sanitizer solution according to
manufacturer’s instructions (no more than 2
days old. Use hot water for best sanitizing
results.
3. Rotate the 9-Tube Assembly coupler until it
unlocks and remove it from the Blending
Head syrup line opening.
26050
4. Unlock the Coupler Body by rotating it from
the Coupler Base. Remove the Coupler
Body, Syrup Line Manifold, and Duckbill
Check Valve from the 9-Tube Assembly.
Place these parts in detergent water.
26170
5. Place the end of the 9-Tube Assembly into
a container to catch the expelled syrup and
sanitizer solution during the rest of the
Clean-In-Place procedure.
26172
SCHEDULED MAINTENANCE
Summary of Contents for TS 80BLD
Page 4: ...3 PAGE INTENTIONALLY LEFT BLANK...
Page 7: ...6 General System Overview 1 3 7 9 8 6 4 5 26001 12 2 10 11 Figure 1...
Page 12: ...11 PAGE INTENTIONALLY LEFT BLANK...
Page 21: ...20 Spare Parts Kit 10 12 13 2 6 5 11 7 16 3 4 1 14 9 15 8 26007 Figure 7...