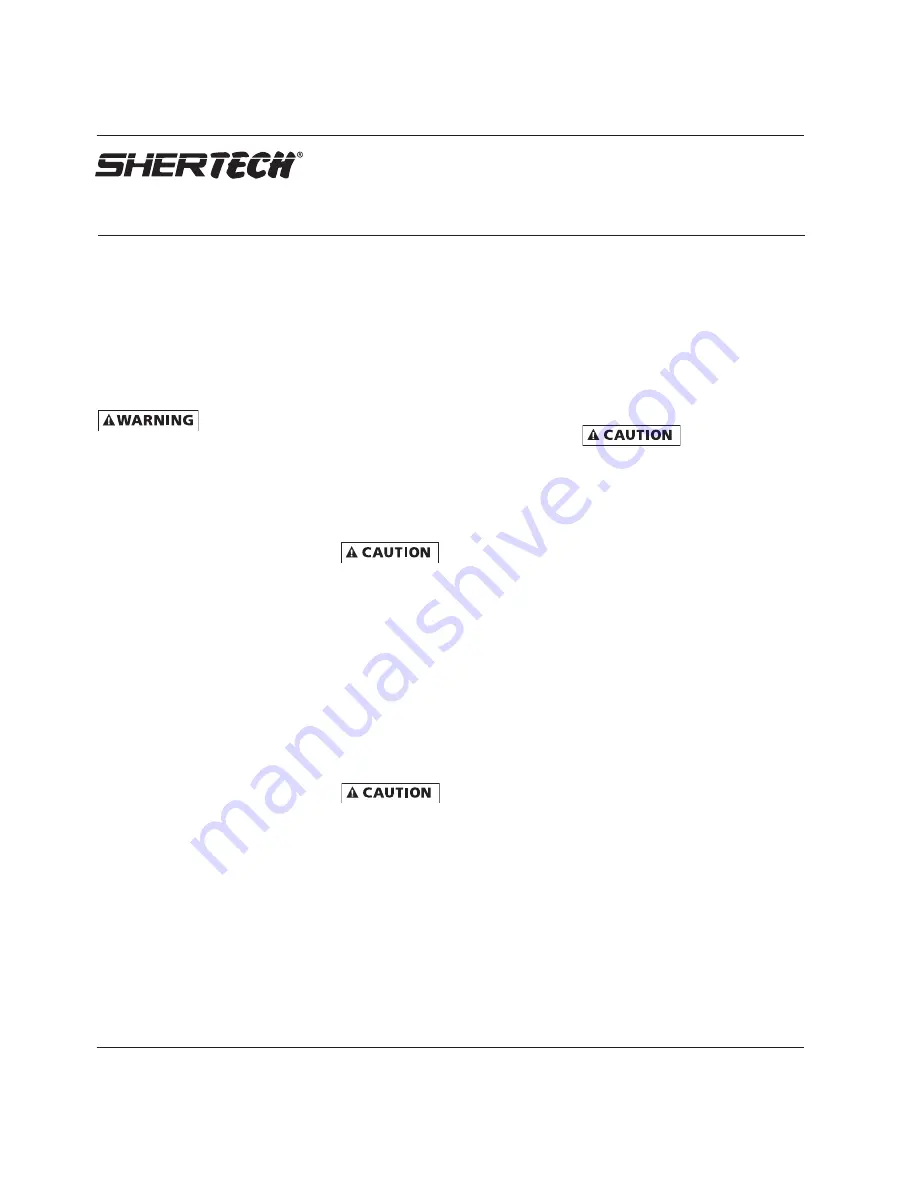
Operation (Continued)
3. On initial start-up, check power
consumption to be sure motor is not
overloaded.
NOTE:
Never shut off discharge or
restrict suction flow while unit is
operating.
Maintenance
Electric disconnect
should only be done by
a qualified electrician. Note: This pump can
be challenging to work on. Only qualified
repair technicians should be used. Improper
repair and/or assembly can cause damage to
pump/motor and also create an electric
shock hazard.
GENERAL
1. Pump should be drained if subjected
to freezing temperatures. A drain
plug (Ref. No. 10) is provided on the
pump casing.
2. Clean the suction line strainer at
regular intervals.
3. Periodically clean dirt accumulations
from open-type motors, especially
in and around vent openings,
preferably by vacuuming (avoids
imbedding dirt in windings).
Properly selected and installed elec-
tric motors are capable of operating
for years with minimal maintenance.
4. Pump motor (Ref. No. 1) is provided
with sealed ball bearings. Normal
relubrication of the bearings is not
required.
5. Periodically check that electrical
connections are tight.
6. Pump should be checked daily,
weekly, monthly, etc. for proper
operation. If anything has changed
since unit was new, unit should be
removed and repaired or replaced.
Only qualified electricians or
technicians should attempt to repair
this unit. Improper repair and/or
assembly can cause an electrical
shock hazard.
MECHANICAL SEAL
All Shertech pumps are furnished with a
precision mechanical seal (Ref. No. 4). This
seal is installed and checked at the factory
and should require no adjustment at the
time of the installation of the pump.
Running the pump without water will
result in rapid seal failure.
After the pump has been in service for a
long period of time, or if the pump has
seen severe service on abrasive materi-
als, it may be necessary to replace this
seal (the seal may leak). Leakage can be
detected by a dripping or flow of liquid
from the area around the motor shaft
sleeve (Ref. No. 5).
Precision lapped faces
on the mechanical seal
are easily damaged. Handle your replace-
ment seal carefully and read these instruc-
tions before attempting to replace the seal.
DISASSEMBLY OF PUMP
After the plumbing has been removed
from the intake and discharge ports, the
pump can be readily disassembled.
1. Remove the four 3/8" diameter bolts
(Ref. No. 3) that attach to front
cover (Ref. No. 9) of the body. Then
remove the cover and o-ring gasket
(Ref. No. 8).
Care should be taken
not to pinch or “shave”
the o-ring gasket (Ref. No. 8) between the
adapter and the casing.
2. The impeller (Ref. No. 7) floats on
the pump shaft sleeve (Ref. No. 5);
therefore it can be readily removed
(See Figure 4).
3. Loosen set screw (Ref. No. 11) on
pump shaft sleeve (Ref. No. 5). The
pump shaft sleeve is threaded on the
motor shaft. Turn the pump shaft
sleeve counterclockwise to remove
(See Figure 4).
NOTE:
It will be necessary to hold the
motor shaft. A screwdriver slot or two
flats for use with an open end 7/16"
wrench are provided at the rear of the
motor shaft (pry off cap for access). To
prevent motor shaft from turning,
either insert a larger screwdriver blade
into the slot, or use a 7/16" wrench
across the flats.
4. The seal (part of Ref. No. 4a) will
come off with the shaft sleeve (Ref.
No. 5) (See Figure 4).
The precision
carbon/ceramic faces on
the mechanical seal are easily damaged.
Handle your repair seal carefully. Do not
touch the carbon/ceramic faces.
5. Remove the pump body (Ref. No. 2)
and push out the seal seat (part of
Ref. No 4a) with a wooden dowel to
remove the seal seat (See Figure 5).
6. Clearance between the impeller
(Ref. No. 7), the body (Ref. No. 2)
and the cover (Ref. No. 9) is held to a
minimum for high pressure perform-
ance. Therefore, any wear in these
parts due to pumping abrasives, etc.,
would affect the pump perform-
ance. Replace parts when necessary.
7. If it becomes necessary to replace
the seal or seat, always replace them
with a complete seal and seat assem-
bly (Ref. No. 4a).
8. Inspect the pump to see if the collar
shown in Figure 7 is present. The
mechanical seal requires the use of
the collar to set the proper seal
working height. If the collar (Ref.
No. 4b) is not present, order item
#17681 when ordering the replace-
ment seal.
ASSEMBLY OF PUMP
IMPORTANT:
Be sure that shaft shoulder
does not damage carbon face.
1. Thoroughly clean all surfaces of
the seal seat cavity in adapter
(Ref. No. 2).
2. Using a clean cloth, wipe the shaft
Bronze and Cast Iron Models
Close-Coupled Turbine Pumps
Bronze and Cast Iron Models
Form L-4069 (4/06)
(
S
/N'
s
AFS-0001 through
AFS-0236
)
Shertech Operating Instructions, Performance,
Specifications and Parts Manual
142
Summary of Contents for P2131
Page 121: ... THIS PAGE INTENTIONALLY LEFT BLANK 115 ...
Page 130: ...SECTION A APPENDIX 124 ...
Page 131: ...A 1 Swagelok Fitting Installation Instructions 125 ...
Page 135: ...A 2 PLC Data Sheet 129 ...
Page 141: ...A 3 VERIFY Product Information 135 ...
Page 147: ...A 4 WRS Pump Information 141 ...
Page 158: ...A 5 Vacuum Leak Test Troubleshooting Guide 152 ...