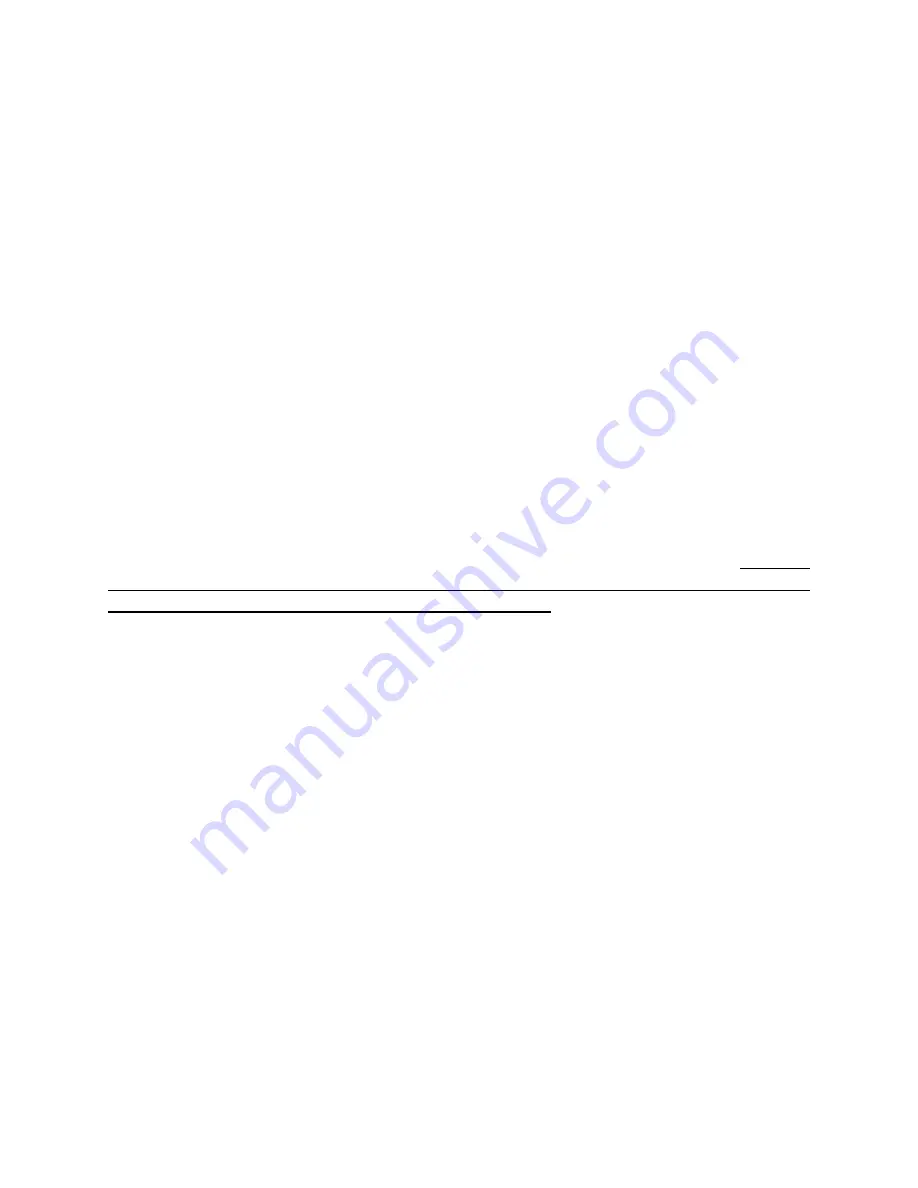
3.
Exposure
–
Steam
flowing
into
the
chamber
slows
and
the
temperature
sensor,
PLC,
and
heaters
begin
controlling
the
temperature
inside
the
chamber
so
that
it
stays
within
a
specified
range
during
the
entire
exposure
time
selected.
NOTE:
The
P2131
is
controlled
by
temperature,
not
by
pressure,
during
exposure.
4.
Drying
–
A
deep
vacuum
is
drawn
on
the
chamber
to
remove
the
steam
and
residual
moisture
from
the
sterilized
items.
5.
Venting
–
The
vacuum
is
released
by
bringing
in
outside
air
through
the
HEPA
filter
so
the
chamber
door
can
be
opened
by
the
operator.
2.5
Water
Supply
Quality
It
is
critical
to
the
long
‐
term
reliability
and
performance
of
the
P2131
sterilizer
that
only
potable
water
(i.e.,
water
safe
for
human
consumption)
should
be
used
as
the
feedwater
to
the
SWS.
The
feedwater
should
meet
FDA
bottled
water
criteria
for
total
coliform
(i.e.,
a
disinfectant
such
as
chlorine
should
be
present).
Reference
Appendix
A.6
for
suggested
maximum
values
of
contaminants
in
the
feed
water.
The
P2131
sterilizer
can
operate
for
14
days
or
100
cycles
with
only
10
gallons
of
water.
However,
the
FDA
requires
that
the
water
in
the
SMU
and
WRS
must
be
drained
and
refilled
every
14
days
or
100
cycles
(whichever
comes
first).
Reference
Section
3.4.
CAUTION
:
It
is
critical
to
use
and
maintain
the
SWS.
Reference
Sections
3.4
and
4.3.4.
If
a
pressurized
potable
water
system
is
available,
a
hose
can
be
connected
directly
to
the
inlet
of
the
SWS.
As
water
flows
through
the
SWS,
calcium,
magnesium,
and
other
contaminants
are
removed
from
the
water,
preventing
deposits
(i.e.,
scale
buildup)
on
the
heating
elements,
jacket
walls,
and
other
components.
This
deionized
water
will
also
prevent
premature
corrosion
of
the
metal
components.
If
a
pressurized
water
system
is
not
available,
the
SWS
is
equipped
with
a
manual
hand
pump,
suction
hose,
and
inlet
strainer.
This
will
allow
potable
water
to
be
manually
pumped
from
a
bucket
or
Jerry
can
through
the
SWS
and
into
the
WRS
for
use
in
the
SMU.
The
three
important
benefits
of
using
the
SWS
are:
1.
Eliminates
costly
sterilizer
downtime
and
maintenance
labor
to
replace
heating
elements
and
to
scrape
and
clean
the
boiler
surfaces.
2.
Improves
sterilizer
cycle
times
by
keeping
heatup
times
short
(1.6
mm
of
scale
buildup
on
the
heating
elements
causes
a
12%
loss
in
heating
efficiency).
3.
Improves
safety
by
eliminating
the
potential
for
sterilizer
rupture
due
to
localized
hot
spots
or
premature
corrosion
that
cause
weakening
of
the
aluminum.
7
Summary of Contents for P2131
Page 121: ... THIS PAGE INTENTIONALLY LEFT BLANK 115 ...
Page 130: ...SECTION A APPENDIX 124 ...
Page 131: ...A 1 Swagelok Fitting Installation Instructions 125 ...
Page 135: ...A 2 PLC Data Sheet 129 ...
Page 141: ...A 3 VERIFY Product Information 135 ...
Page 147: ...A 4 WRS Pump Information 141 ...
Page 158: ...A 5 Vacuum Leak Test Troubleshooting Guide 152 ...