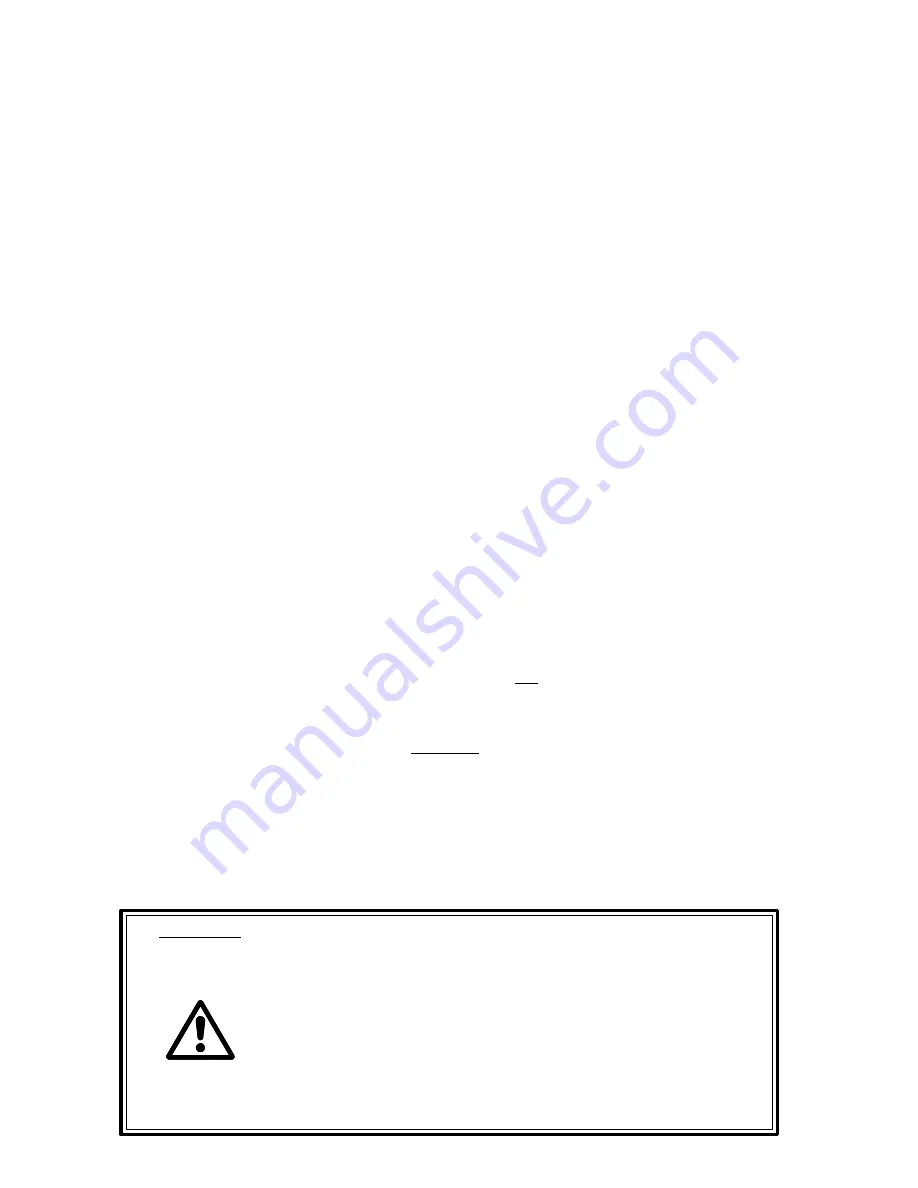
105
This error comes up in the following cases:
> A comment has more than 43 characters.
> A program has been defined with more than 5 characters.
> A block number has more than 4 characters.
> Strange characters in memory.
106 ** Inside temperature limit exceeded.
108 ** Error in Z axis leadscrew error compensation parameters. The CNC initializes the RS232C serial line
parameters: P0=9600, P1=8, P2=0, P3=1, P605(5)=1, P605(6)=1, P605(7)=1.
110 ** Error in X axis leadscrew error compensation parameters. The CNC initializes the RS232C serial line
parameters: P0=9600, P1=8, P2=0, P3=1, P605(5)=1, P605(6)=1, P605(7)=1.
111 *
FAGOR LAN line error. Hardware installed incorrectly.
112 *
FAGOR LAN error. It comes up in the following instances:
> When the configuration of the LAN nodes is incorrect.
> The LAN configuration has been changed. One of the nodes is no longer present (active).
When this error occurs, access the LAN mode, editing or monitoring, before executing a program block.
113 *
FAGOR LAN error. A node is not ready to work in the LAN. For example:
> The PLC64 program is not compiled.
>A G52 type block has been sent to an 82CNC while it was in execution.
114 *
FAGOR LAN error. An incorrect command has been sent out to a node.
115 *
Watch-dog error in the periodic module.
This error occurs when the periodic module takes longer than 5 milliseconds.
116 *
Watch-dog error in the main module.
This error occurs when the main module takes longer than half the time indicated in machine parameter
"P729".
117 *
The internal CNC information requested by activating marks M1901 thru M1949 is not available.
118 *
An attempt has been made to modify an unavailable internal CNC variable by means of marks M1950
thru M1964.
119
Error when writing machine parameters, the decoded M function table and the leadscrew error compen-
sation tables into the EEPROM memory.
This error may occur when after locking the machine parameters, the decoded M function table and the
leadscrew error compensation tables, one tries to save this information into the EEPROM memory.
120
Checksum error when recovering (restoring) the machine parameters, the decoded M function table and
leadscrew error compensation tables from the EEPROM memory.
Atention:
The ERRORS indicated with "*" behave as follows:
They stop the axis feed and the spindle rotation by cancelling
the Enable signals and the analog outputs of the CNC.
They interrupt the execution of the part-program of the CNC if
it was being executed.
The ERRORS indicated with "**" besides behaving as those with an
"*", they activate the INTERNAL EMERGENCY OUTPUT.
Summary of Contents for 8025 T CNC
Page 1: ...CNC 8025 T TS New Features Ref 0107 in...
Page 9: ...FAGOR 8025 8030 CNC Models T TG TS OPERATING MANUAL Ref 9701 in...
Page 14: ...COMPARISON TABLE FOR LATHE MODEL FAGOR 8025 8030 CNCs...
Page 20: ...Introduction 1 INTRODUCTION...
Page 91: ...ERROR CODES...
Page 98: ...FAGOR 8025 8030 CNC Models T TG TS PROGRAMMING MANUAL Ref 9701 in...
Page 103: ...COMPARISON TABLE FOR LATHE MODEL FAGOR 8025 8030 CNCs...
Page 109: ...Introduction 1 INTRODUCTION...
Page 167: ...8025 8030 CNC PROGRAMMING MANUAL 53 Compensated path Programmed path C P P P C P P P C P P P...
Page 168: ...54 8025 8030 CNC PROGRAMMING MANUAL C P P P C P P P C P P P C P P P...
Page 170: ...56 8025 8030 CNC PROGRAMMING MANUAL Compensated path C P P P Programmed path C P P P...
Page 171: ...8025 8030 CNC PROGRAMMING MANUAL 57 Compensated path Programmed path C P P P C P P P...
Page 172: ...58 8025 8030 CNC PROGRAMMING MANUAL Programmed path Compensated path C P P P C P P P...
Page 174: ...60 8025 8030 CNC PROGRAMMING MANUAL Compensated path Programmed path C P P P C P P P C P P P...
Page 175: ...8025 8030 CNC PROGRAMMING MANUAL 61 C P P P P P C P P P C P P P C P...
Page 194: ...80 8025 8030 CNC PROGRAMMING MANUAL...
Page 199: ...8025 8030 CNC PROGRAMMING MANUAL 85...
Page 269: ...8025 8030 CNC PROGRAMMING MANUAL 155 Subroutines flow chart...
Page 303: ...ERROR CODES...