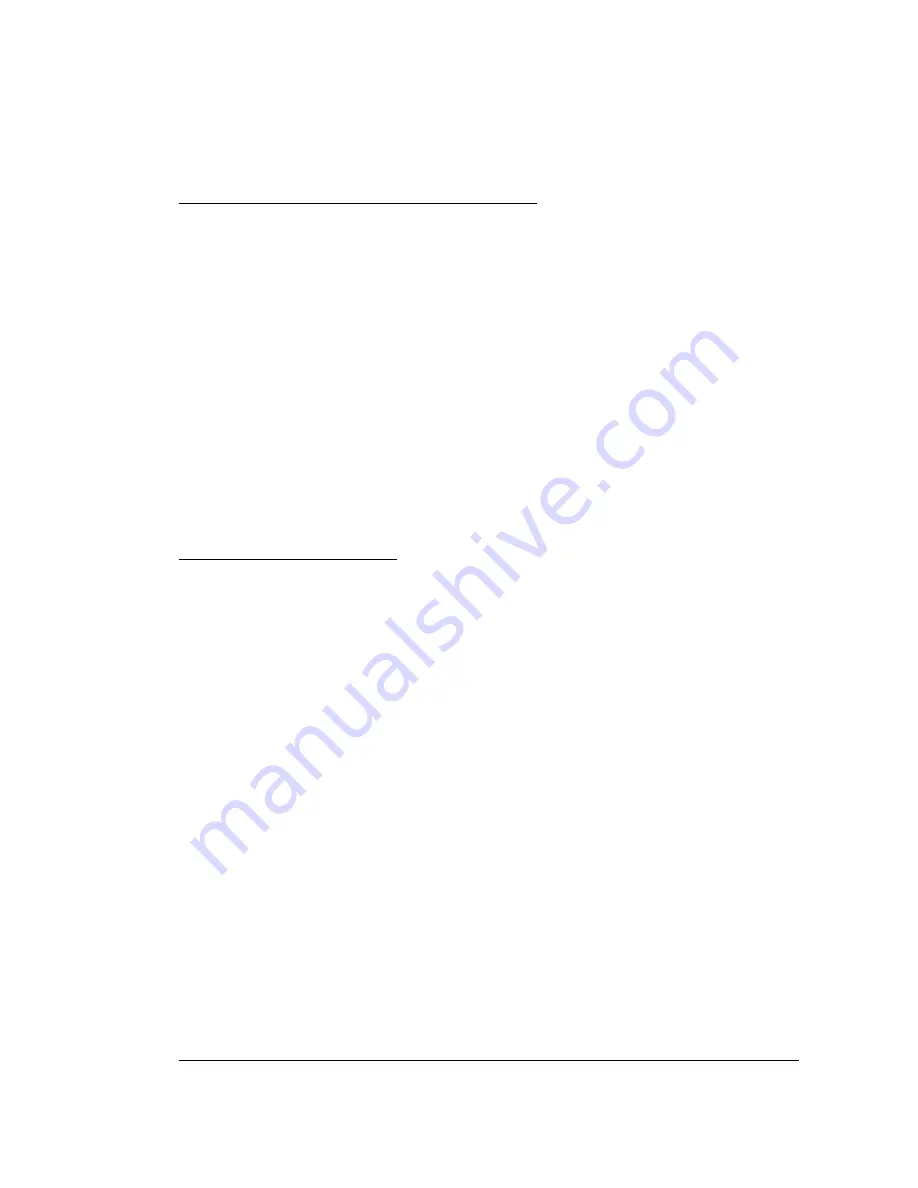
8025/8030 CNC PROGRAMMING MANUAL
93
6.27.4. Preparation of a digitizing operation and later execution at the machine.
CONCEPTION OF THE SYSTEM. THE PROBE.
The probe can be fastened to the toolholder of the milling machine or machining center,
as if it were a tool, converting the machine tool into an automatic digitizing system.
The tip (interchangeable) of the needle of the probe is provided with a ball which is
threaded to the probe and follows the surface of the pattern during digitizing. Each probe
involves a family of tips with different ball radii for multiple applications.
The diameter of the ball of the needle or tip should be the same as the tool used in
subsequent machining.
The corrections of radii for other tools are also possible but another treatment of
the digitized program is required (G41, G42, G43).
The different probe needles have variable weights. In fact, in the probe system, needles
must have a maximum weight of 200 gm approximately to avoid possible errors of
interpretation of contact.
CALIBRATING THE PROBE
For this, we use the N01 cycle with which we determine the offset values for the probe,
which will be entered by the CNC in the corresponding corrector, which we have chosen
previously. (T00 by default.) The offset values are the error which may exist in the axes
of the main plane between the axis of the toolholder and the center of the measurement
probe ball.
In order to execute this cycle it is necessary to machine a hole beforehand, inside which
we will carry out the probings.
Once the hole has been made, the diameter and X,Y,Z coordinates of which we know (this
is due to that fact that we have chosen the place previously and moved to it with the CNC
jog controls) we change the tool for the probe and move in Z until we are inside the hole.
Next, we execute the N01 probe calibration cycle. Previously the programming format is
completed and the tool corrector is chosen where we want offset I,K to appear. T00
corrector is taken by default. All these operations can be done in TEACH-IN.
On exiting from the cycle the control automatically updates the I,K offset of the table and
the probe goes back to the starting point. Next we complete the rest of the information on
the table:
R: Radius of the ball
L: Length of the probe (depends on the zero part). If zero part is on the surface of
part, L will be zero also.
Summary of Contents for 8025 T CNC
Page 1: ...CNC 8025 T TS New Features Ref 0107 in...
Page 9: ...FAGOR 8025 8030 CNC Models T TG TS OPERATING MANUAL Ref 9701 in...
Page 14: ...COMPARISON TABLE FOR LATHE MODEL FAGOR 8025 8030 CNCs...
Page 20: ...Introduction 1 INTRODUCTION...
Page 91: ...ERROR CODES...
Page 98: ...FAGOR 8025 8030 CNC Models T TG TS PROGRAMMING MANUAL Ref 9701 in...
Page 103: ...COMPARISON TABLE FOR LATHE MODEL FAGOR 8025 8030 CNCs...
Page 109: ...Introduction 1 INTRODUCTION...
Page 167: ...8025 8030 CNC PROGRAMMING MANUAL 53 Compensated path Programmed path C P P P C P P P C P P P...
Page 168: ...54 8025 8030 CNC PROGRAMMING MANUAL C P P P C P P P C P P P C P P P...
Page 170: ...56 8025 8030 CNC PROGRAMMING MANUAL Compensated path C P P P Programmed path C P P P...
Page 171: ...8025 8030 CNC PROGRAMMING MANUAL 57 Compensated path Programmed path C P P P C P P P...
Page 172: ...58 8025 8030 CNC PROGRAMMING MANUAL Programmed path Compensated path C P P P C P P P...
Page 174: ...60 8025 8030 CNC PROGRAMMING MANUAL Compensated path Programmed path C P P P C P P P C P P P...
Page 175: ...8025 8030 CNC PROGRAMMING MANUAL 61 C P P P P P C P P P C P P P C P...
Page 194: ...80 8025 8030 CNC PROGRAMMING MANUAL...
Page 199: ...8025 8030 CNC PROGRAMMING MANUAL 85...
Page 269: ...8025 8030 CNC PROGRAMMING MANUAL 155 Subroutines flow chart...
Page 303: ...ERROR CODES...