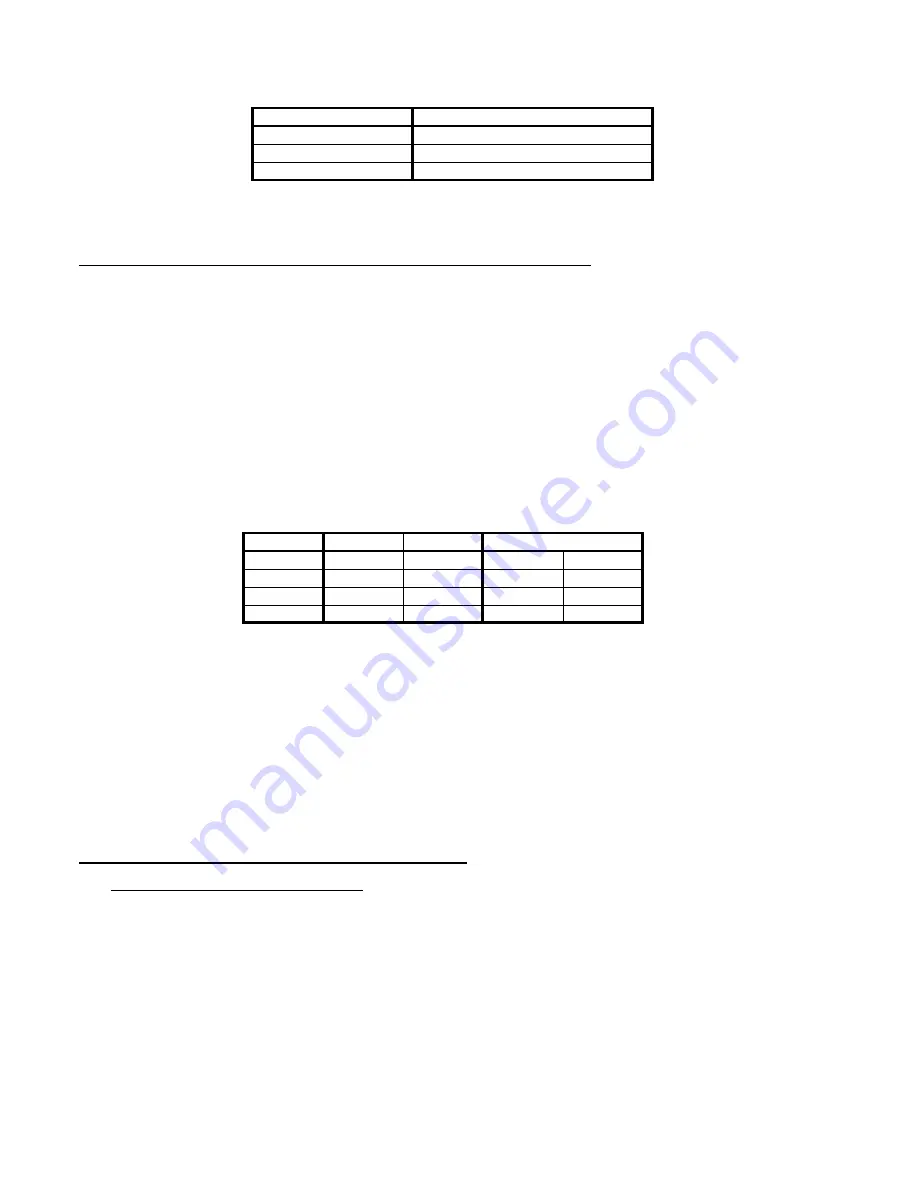
- 6 -
P501
P622(2)
P622(1)
Resolution
1
0
0
0.001 mm
0.0001"
2
0
1
0.002 mm
0.0002"
5
1
0
0.005 mm
0.0005"
10
1
1
0.010 mm
0.0010"
This way and after applying the multiplying factor, one obtains the axis moving units. These units correspond to the
units used for the display format
Example:
Handwheel Resolution : 250 lines per turn
When attempting to "crank" an axis faster than its maximum feedrate (machine parameters "P110, P310"), the CNC will
limit the actual axis feedrate to that parameter value ignoring the rest of the pulses supplied by the handwheel, thus
preventing a Following Error message from being issued.
5.1 MACHINE PARAMETERS FOR THE HANDWHEELS:
P622(6) = 0
There
is no
electronic handwheel associated with the Z axis
P622(6) = 1
There
is
electronic handwheel associated with the Z axis
P609(1) = 0
The electronic handwheel being used
is not
a FAGOR 100P model.
P609(1) = 1
The electronic handwheel being used
is
a FAGOR 100P model.
This parameter makes sense when using a single handwheel associated with the X axis. It indicates
whether or not it is a FAGOR 100P with axis selector button.
P500
Counting direction of the X axis handwheel (No / Yes)
P622(5)
Counting direction of the Z axis handwheel (0 / 1)
P602(1)
Feedback units of the X axis handwheel (0 = millimeters /1 = inches)
P622(3)
Feedback units of the Z axis handwheel (0 = millimeters /1 = inches)
P501
Square-wave feedback resolution of the X axis handwheel.
P622(1,2)
Square-wave feedback resolution of the Z axis handwheel.
P602(4)
Multiplying factor for X axis handwheel feedback pulses (0= x4 / 1= x2)
P622(4)
Multiplying factor for Z axis handwheel feedback pulses (0= x4 / 1= x2)
P621(2) = 0
Handwheel disabled for Manual Feedrate Override (MFO) switch positions other than the
handwheel positions.
P621(2) = 1
When the MFO is at a position other than those for the handwheel , the CNC takes it into account
and applies a "x1" multiplying factor.
Example: Having a Fagor electronic handwheel (25 lines per turn) set as follows:
P602(1)=0 Millimeters; P501=1 Resolution 0.001 mm.; P602(4)=0 x4 Multiplication factor
Depending on the position of the MFO switch (Manual Feedrate Override), the selected axis will move:
Position 1
1 x 25 x 4 =
0.100 mm per turn
Position 10
10 x 25 x 4 =
1.000 mm per turn
Position 100
100 x 25 x 4 = 10.000 mm per turn
5.2 USING ELECTRONIC HANDWHEELS
The machine uses one electronic handwheel
When using a single electronic handwheel, it must be connected to A6.
If the handwheel is a FAGOR 100P type, machine parameter "P609(1)" must be set to "1".
Once the desired handwheel position has been selected at the MFO switch, press one of the JOG keys of the axis
to be jogged. The selected axis appears highlighted.
When using a FAGOR handwheel with an axis selector button, the desired axis can also be selected as follows:
* Press the push-button on the rear of the handwheel. The CNC selects the first axis and it highlights it.
* By pressing the button again, the next axis is selected and so on, rolling over from the last axis to the first one.
* By keeping the button pressed for more than 2 seconds, the CNC de-selects the currently selected axis.
The selected axis will be jogged as the handwheel is turned, reversing directions when reversing the turning direction
of the handwheel.
MFO Switch position
Distance per turn
1
0.250 mm or 0.0250 inch
10
2.500 mm or 0.2500 inch
100
25.000 mm or 2.5000 inches
Summary of Contents for 8025 T CNC
Page 1: ...CNC 8025 T TS New Features Ref 0107 in...
Page 9: ...FAGOR 8025 8030 CNC Models T TG TS OPERATING MANUAL Ref 9701 in...
Page 14: ...COMPARISON TABLE FOR LATHE MODEL FAGOR 8025 8030 CNCs...
Page 20: ...Introduction 1 INTRODUCTION...
Page 91: ...ERROR CODES...
Page 98: ...FAGOR 8025 8030 CNC Models T TG TS PROGRAMMING MANUAL Ref 9701 in...
Page 103: ...COMPARISON TABLE FOR LATHE MODEL FAGOR 8025 8030 CNCs...
Page 109: ...Introduction 1 INTRODUCTION...
Page 167: ...8025 8030 CNC PROGRAMMING MANUAL 53 Compensated path Programmed path C P P P C P P P C P P P...
Page 168: ...54 8025 8030 CNC PROGRAMMING MANUAL C P P P C P P P C P P P C P P P...
Page 170: ...56 8025 8030 CNC PROGRAMMING MANUAL Compensated path C P P P Programmed path C P P P...
Page 171: ...8025 8030 CNC PROGRAMMING MANUAL 57 Compensated path Programmed path C P P P C P P P...
Page 172: ...58 8025 8030 CNC PROGRAMMING MANUAL Programmed path Compensated path C P P P C P P P...
Page 174: ...60 8025 8030 CNC PROGRAMMING MANUAL Compensated path Programmed path C P P P C P P P C P P P...
Page 175: ...8025 8030 CNC PROGRAMMING MANUAL 61 C P P P P P C P P P C P P P C P...
Page 194: ...80 8025 8030 CNC PROGRAMMING MANUAL...
Page 199: ...8025 8030 CNC PROGRAMMING MANUAL 85...
Page 269: ...8025 8030 CNC PROGRAMMING MANUAL 155 Subroutines flow chart...
Page 303: ...ERROR CODES...