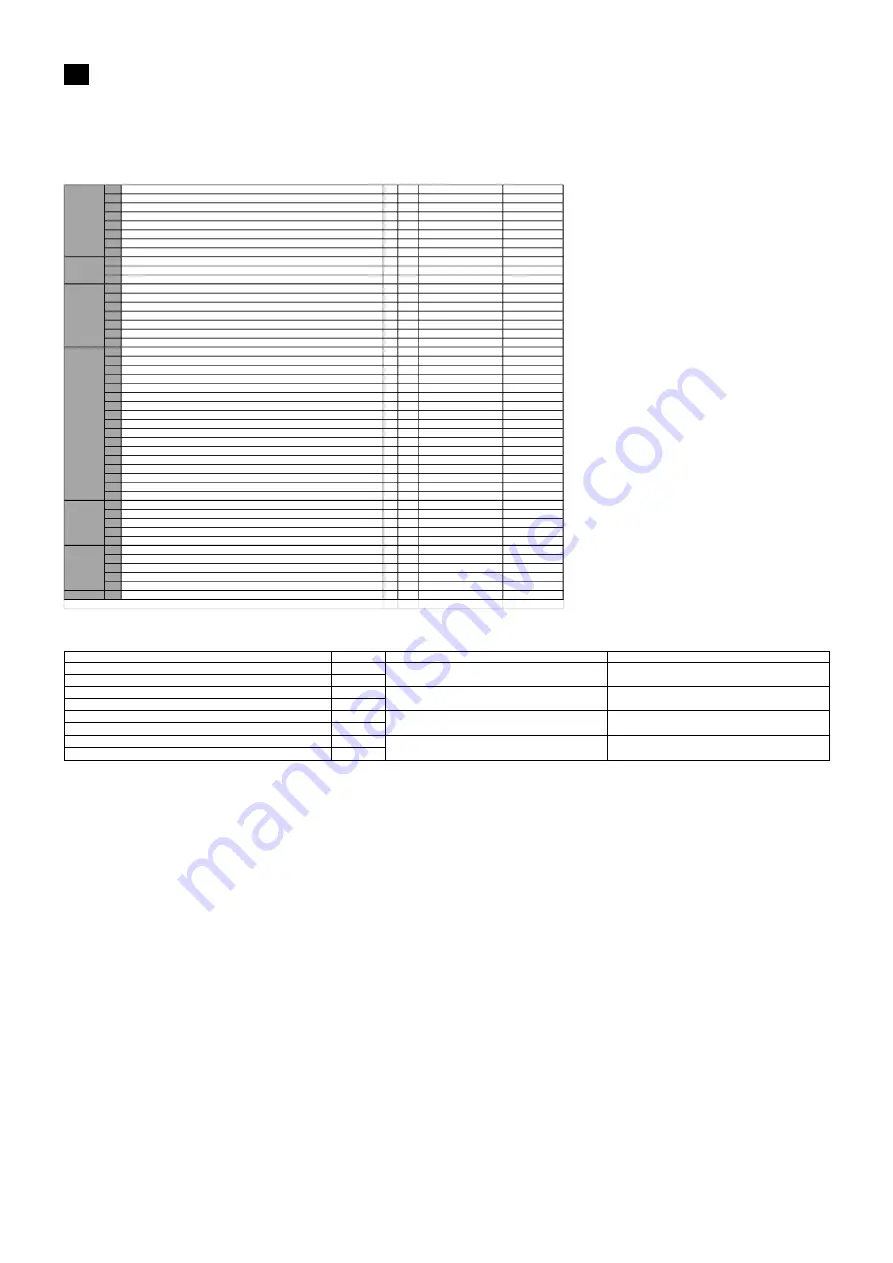
9
EN
SUMMARY (1.1)
PLATES.................................................................................
pag. 10
TECHNICAL DATA........................................................................
pag. 9
TRANSPORT AND SET UP..................................................
pag. 10
DECLARATION OF VIBRATION EMISSION ...............................
pag. 9
BATTERY..............................................................................
pag. 10
USE OF THE MACHINE................................................................
pag. 9
USE………............................................................................
pag. 10
DESCRIPTION OF THE TRUCK...................................................
pag. 9
MAINTENANCE....................................................................
pag. 11
SAFETY DEVICES........................................................................
pag. 9
TROUBLE SHOOTING.........................................................
pag .12
TECHNICAL DATA (3.42)
1.1
MANUFACTURER
PR INDUSTRIAL
PR INDUSTRIAL
1.2
MODEL
RX 10/16 EVO Li-Ion
RX 10/09 EVO Li-Ion
1.3
DRIVE
ELECTRIC
ELECTRIC
1.4
OPERATOR TYPE
PEDESTRIAN
PEDESTRIAN
1.5
LOAD CAPACITY
Q
kg
1000
1000
1.6
LOAD CENTRE DISTANCE
c
mm
600
600
1.8
LOAD DISTANCE, CENTRE OF DRIVE AXLE TO FORK
x
mm
786
786
1.9
WHEEL BASE
y
mm
1165
1165
2.1
SERVICE WEIGHT
kg
371
345
2.2
AXLE LOAD LADED, FRONT/REAR
kg
434/937
411/934
2.3
AXLE LOAD UNLADEN, FRONT/REAR
kg
269/102
246/99
3.1
TYRES *
G+P/P
G+P/P
3.2
TYRE SIZE, FRONT (Ø x width)
186x50
186x50
3.3
TYRE SIZE, REAR (Ø x width)
82x70
82x70
3.4
SIDE WHEELS (Ø x width)
125x45
125x45
3.5
WHEELS, NUMBER (x=DRIVEN) FRONT/REAR
1x+1/2
1x+1/2
3.6
TREAD, FRONT
b
10
mm
505
505
3.7
TREAD, REAR
b
11
mm
410
410
4.2
HEIGHT, MAST LOWERED
h
1
mm
1970
1270
4.3
FREE LIFT
h
2
mm
1510
810
4.4
LIFT
h
3
mm
1510
810
4.5
HEIGHT, MAST EXTENDED
h
4
mm
1970
1270
4.6
INITIAL LIFT
h
5
mm
-
-
4.9
HEIGHT OF TILLER IN DRIVE POSITION MIN/MAX
h
14
mm
968/1338
968/1338
4.15
HEIGHT, LOWERED
h
13
mm
90
90
4.19
OVERALL LENGTH
l
1
mm
1675
1675
4.20
LENGHT TO FACE OF FORKS
l
2
mm
522
522
4.21
OVERALL WIDTH
b
1
mm
794
794
4.22
FORK DIMENSIONS
s/e/l
mm
60/150/1153
60/150/1153
4.24
FORK-CARRIAGE WIDTH
b
3
mm
650
650
4.25
DISTANCE BETWEEN FORK ARMS
b
5
mm
560
560
4.26
DISTANCE BETWEEN LEGS
b
4
mm
-
-
4.32
GROUND CLEARANCE, CENTRE OF WHEEL BASE
m
2
mm
30
30
4.34
AISLE WIDTH FOR PALLETS 800x1200 LENGHTWISE
A
st
mm
2120
2120
4.35
TURNING RADIUS
W
a
mm
1344
1344
5.1
TRAVEL SPEED, LADEN/UNLADEN
km/h
3,7/4,3
3,7/4,3
5.2
LIFT SPEED, LADEN/UNLADEN
m/s
0,12/0,21
0,12/0,21
5.3
LOWERING SPEED, LADEN/UNLADEN
m/s
0,25/0,21
0,25/0,21
5.8
MAX GRADEABILITY, LADEN/UNLADEN
%
10/15
10/15
5.10
SERVICE BRAKE
ELECTRIC
ELECTRIC
6.1
DRIVE MOTOR POWER
kW
0,35
0,35
6.2
LIFT MOTOR POWER
kW
2,2
2,2
6.4
BATTERY VOLTAGE, NOMINAL CAPACITY C5
V/Ah
24/50
24/50
6.5
BATTERY WEIGHT
kg
13
13
6.6
ENERGY CONSUMPTION ACC. TO VDI CYCLE
kWh/h
0,45
0,45
8.4
SOUND LEVEL AT DRIVER'S EAR
dB(A)
63
63
*G=Rubber, P=Polyurethane, N=Nylon
D
E
S
C
R
IP
T
IO
N
W
EI
G
H
T
S
T
Y
R
E
S
/C
H
A
S
S
IS
D
IM
E
N
S
IO
N
S
P
E
R
F
O
R
M
A
N
_C
E
D
A
T
A
E
L
E
C
T
R
IC
M
O
T
O
R
S
DECLARATION OF VIBRATION EMISSION (33.2)
Declared vibration emission values in compliance with EN 12096
Description
Value
European Norm (EN)
Test surface
Measured vibration emission value, a (m/s
2
)
0.71
EN ISO 20643 (Hand-Arm)
Industrial smooth concrete floor
Uncertainty, K (m/s
2
)
0.68
Measured vibration emission value, a (m/s
2
)
2.3
EN ISO 20643 (Hand-Arm)
On test track according to EN 13059
Uncertainty, K (m/s
2
)
0.6
Measured vibration emission value, a (m/s
2
)
0.77
EN 13059 (Whole body)
Industrial smooth concrete floor
Uncertainty, K (m/s
2
)
0.39
Measured vibration emission value, a (m/s
2
)
1.02
EN 13059 (Whole body)
On test track according to EN 13059
Uncertainty, K (m/s
2
)
0.08
Values determined in compliance with EN ISO 20643 and EN 13059.
USE OF THE MACHINE (4.1)
This machine has been designed to lift and transport loads on perfectly even floors. An identification plate can be found on the chassis indicating the lifting capacity that must never be
exceeded both for the safety of the personnel and not to damage the vehicle.Please observe the safety, use and maintenance regulations to the letter.Any mounting of extra equipment on the
machine must be authorised by the manufacturers.
DESCRIPTION OF THE TRUCK (5.17) (see fig.1)
This machine is an electric fork lift truck with steering bar drive and is perfect for storing and transporting loads on perfectly even surfaces. The controls are easy to see and use. The machine
complies with all current EEC safety and comfort regulations. The drawing shows its main specifications: 1) STEERING BAR 2) MOTOR WHEEL 3) HYDRAULIC OUTLET 4) FORKS MANUAL
RELEASE DEVICE 5) LIFTING FORK 6) RECTIFIER 7) CHASSIS 8) LIFTING CYLINDER 9) MAIN SWITCH 10) FORK CONTROL ELECTRONIC BOARD (EVO) 11) ELECTRONIC CARD
12) STABILISING WHEEL 13) COVERS 14) PARACHUTE VALVE 15) BATTERY 16) ELECTRIC BRAKE 17) LOADING ROLLERS 18) HAND GUARD.
SAFETY DEVICES (6.12) (see fig.1)
1) MASTER SWITCH (ref.9); 2) ELECTRIC BRAKE (ref.16); 3) FLOW LIMITING VALVE (ref.14); 4) MAXIMUM PRESSURE VALVE; 5) BUMPERS: they protect the driving wheel (ref. 2), the
lateral stabilizing wheels (ref. 12) and the front loading rollers (ref. 17) from bumps; in case of accidents, therefore, the feet and the load are protected; 6) DEAD MAN'S HANDLE (ref.2/fig.3):
this is a safety switch located on the steering bar and protects the driver from collisions when reversing; 7) HAND GUARD (ref.18); 8) FORKS MANUAL RELEASE DEVICE (RIF. 4).
Structure (7.10)
The lifting mast, the legs and the hood form a very rigid welded structure (ref. 6). The forks are precision guided by 4 rollers that run up the whole mast. The drive wheel, a pivoted wheel and
two rollers give the truck great stability on 4 points of support. The covers (REF. 13) can be easily opened to allow access to all the units for maintenance.
Drive (8.4)
The drive unit moves the driving wheel by means on conical and cylindrical gears. Movement can be inverted by using the throttle valves located on the steering bar (ref.1/fig.3).
Steering bar (9.12+X60) (Rif.1/Fig.1)
The truck can be driven by a person. The steering angle is 175°. The steering bar operates directly on the driving wheel, therefore, to change direction turn it in the required direction. To move
the truck (see fig.2) keep the steering bar in its central position (pos.B), while to stop it move it to its upper position (pos.A) or in its lower position (pos.C). When released the steering bar
returns automatically to its upper position (pos.A) and acts as a parking brake. In “tortoise” mode, when the steering wheel is in the upper position (pos. A) or in the lower position (pos. C), if
you press the “tortoise” pushbutton (ref. 8, fig. 3) and act on the start regulator (ref. 1, fig. 3), the carriage will move at a reduced speed.
Brakes (10.7)
Service braking is provided by the engine, when releasing the accelerator. The electromagnetic brake acts as a parking brake and emergency brake. Emergency braking is carried out by
moving the tiller to the upper position (pos.A) or to the lower position (pos.C) (see fig.2). If the electrical system is off, the electromagnetic brake acts as a parking brake.
Hydraulic circuit (11.12)
In order to lift and lower the forks, operate the dedicated tiller controls (ref.4,5/fig.3):
BASIC: operating the button, lifting and lowering are directly activated in on/off mode.
EVO: lifting and lowering speed can be adjusted proportionally to the control rocker switch rotation angle through an electronic controller (ref.10/fig.1).
The energy necessary for effective work is supplied by the battery (ref.15/fig.1). In the event of an electric failure or battery discharging when the forks are lifted, it is possible to lower them to
move the truck away acting on the manual release device (RIF.4/FIG.1) on the power pack.
Two safety valves are installed in the hydraulic circuit:
a) Hose burst valve stops the load from falling suddenly in case the hydraulic system fails and is contained in the lift cylinder
b) Maximum pressure valve, this is contained in the motor pump and protects the mechanical and hydraulic system from overloading.
Summary of Contents for RX 10 Li-Ion
Page 1: ......
Page 4: ......
Page 5: ...S O C 1 0 0 1 0 0 0 1 1 1 V 2 5 6V I 1 0 0A L i f t i n g 1 S OC 1 0 0 0 T i me 6 0mi n 1 0 0...
Page 6: ......
Page 52: ...44 21 2 26 1 22 1 23 1 25 1 27 1 24 1 OXI 49 NAI OXI 34 1...
Page 80: ...72 22 1 26 1 24 1 23 1 25 1 27 1 21 2 45 34 1...
Page 100: ...92 M ICRO C 21 2 26 1 SWITCH 24 1 22 1 23 1 25 1 27 1 NAVR EN CH 45 34 1...
Page 105: ......
Page 106: ......
Page 107: ......