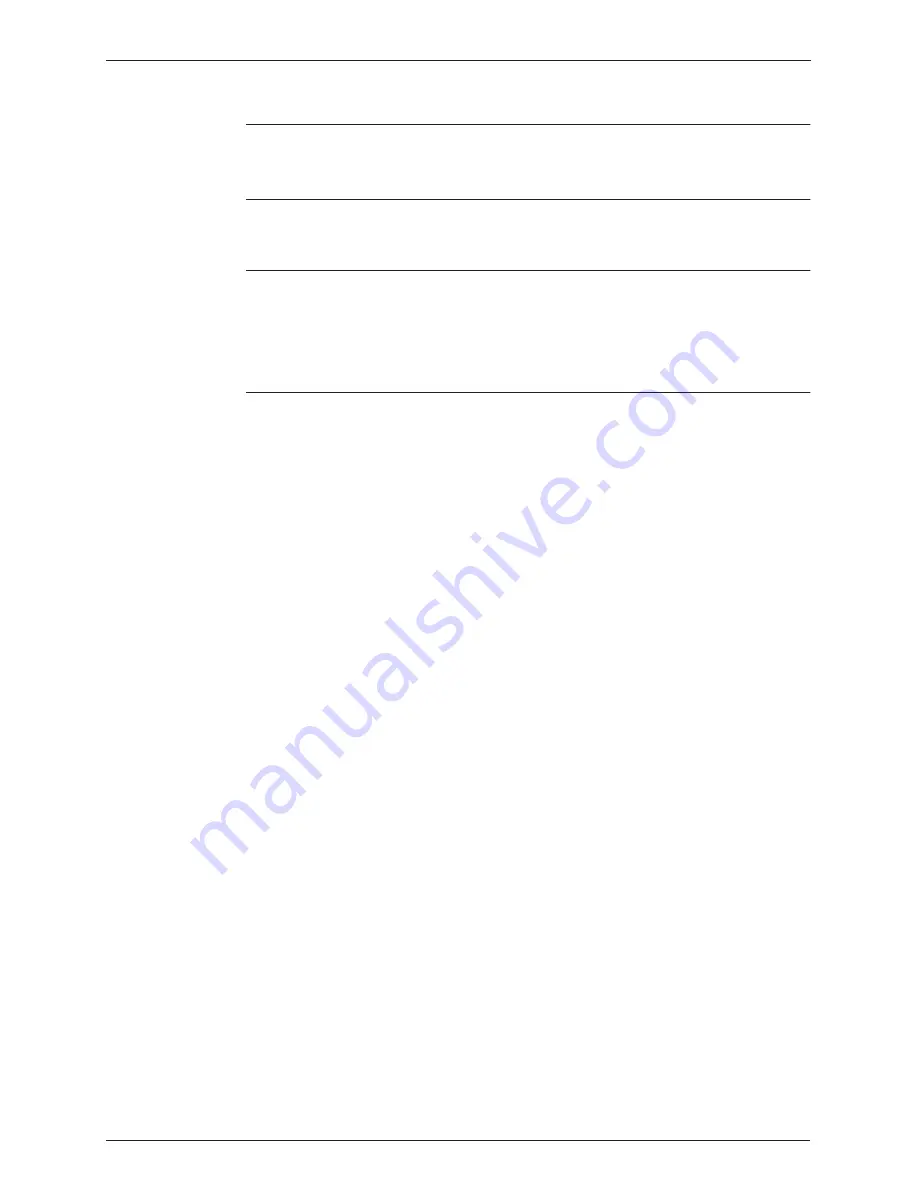
Troubleshooting for Outdoor Unit (50/60 class)
Si21-205
212
Troubleshooting
7.12 Output Over Current Detection
Remote
Controller
Display
L5
Method of
Malfunction
Detection
An output over-current is detected by checking the current that flows in the inverter DC section.
Malfunction
Decision
Conditions
A position signal error occurs while the compressor is running.
A speed error occurs while the compressor is running.
An output over-current input is fed from the output over-current detection circuit to the
microcomputer.
The system will be shut down if the error occurs 16 times.
Clearing condition: Continuous run for about 5 minutes (normal)
Supposed
Causes
Over-current due to defective power transistor
Over-current due to wrong internal wiring
Over-current due to abnormal supply voltage
Over-current due to defective PCB
Error detection due to defective PCB
Over-current due to closed stop valve
Over-current due to compressor failure
Over-current due to poor installation condition
Summary of Contents for Sky Air B-Series R-410A
Page 7: ...Si21 205 vi Table of Contents ...
Page 15: ...Models Si21 205 4 Model Name and Power Supply ...
Page 16: ...Si21 205 Functions 5 Part 2 Functions 1 List of Functions 6 ...
Page 35: ...Wireless Remote Controller Si21 205 24 Remote Controller ...
Page 79: ...Settings Concerning Maintenance Si21 205 68 Field Setting Detail of PCB 2 ...
Page 83: ...Maintenance Mode Setting Si21 205 72 Field Setting ...
Page 239: ...Troubleshooting for Outdoor Unit 50 60 class Si21 205 228 Troubleshooting ...
Page 321: ...Outdoor Unit 50 60 class Si21 205 310 Removal Procedure ...