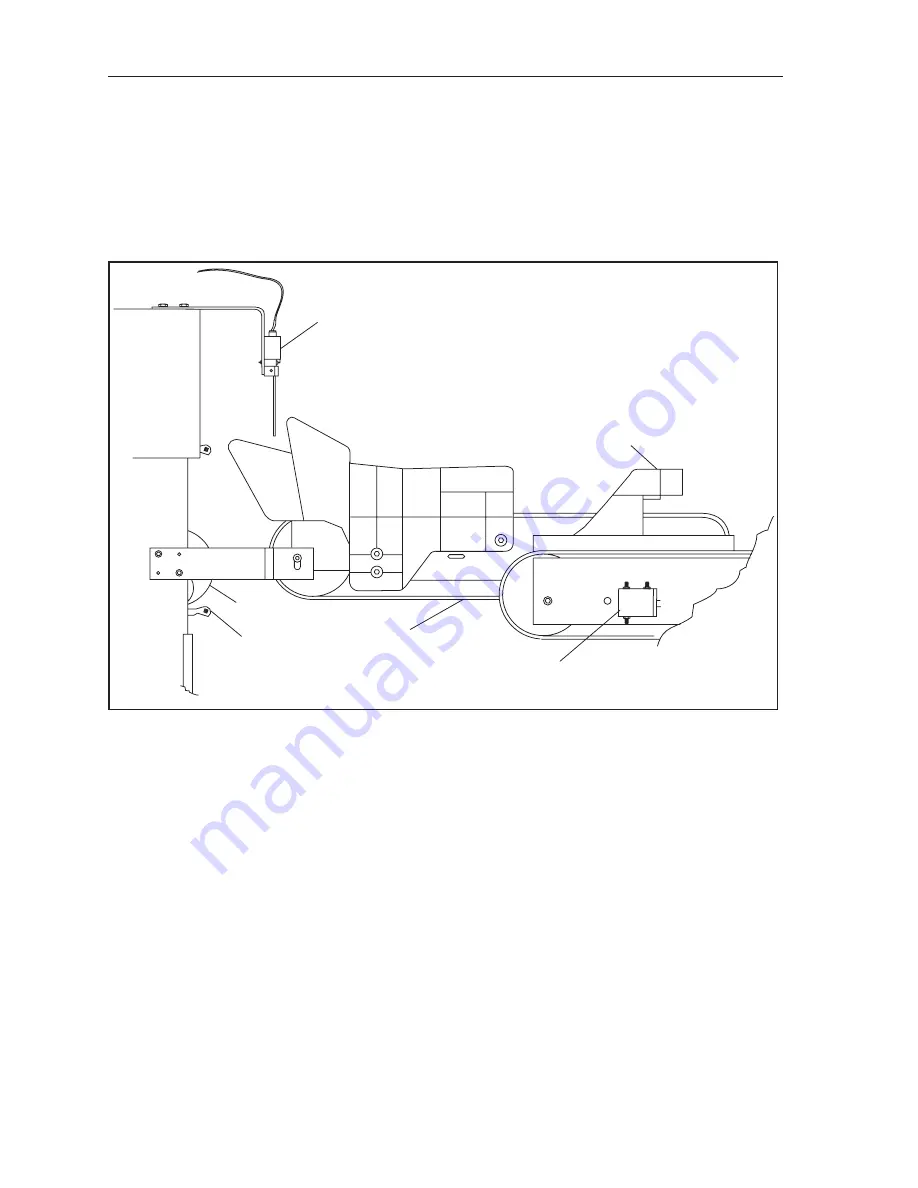
2-24
Section 2: Electronics, Switches, Solenoids and Motors
Section Rev. December 2016
Shark Solenoid
This solenoid is used to control the Shark Fin guide. Energizing the solenoid will cause the pin guide
to flip left to direct the pin onto the right side of the distributor. When the solenoid is de-energized, a
return spring pulls the guide back to it original position deflecting pins to the left distributor lanes. The
pins are deflected in a (L-R-L-L-R, L-R-L-L-R) pattern. The “R” designation is for the 10 pin or right
hand side of the pinsetter. The “L” designation is for the “7” pin or the left side of the pinsetter. The
electronics determined when to energize the solenoid based on the signal coming from the pin count
switch.
(1)
PIN COUNT
SWITCH
(5)
PIN SHOVEL
(6)
PIN
(3)
SHARK
SOLENOID
(4)
GREEN
BELTS
(2)
SHARK FIN
GUIDE
Figure 2-21. Shark Solenoid
(1) PIN COUNT SWITCH
(2) SHARK FIN GUIDE
(3) SHARK SOLENOID
(4) GREEN BELTS
(5) PIN SHOVEL
(6) PIN
Summary of Contents for GS-X Series
Page 1: ...Operations Service Manual GS X Pinsetter with Advanced CE Guarding March 2017 47 902748 000...
Page 4: ...2 Safety Section Section Rev February 2017 Intentionally Blank Page...
Page 15: ...Section Rev February 2017 Safety Section 13 GS Safetty Mirror Safety Mirror...
Page 36: ...1 2 Section 1 Operations Section Rev February 2009 Intentionally Blank Page...
Page 51: ...Section Rev February 2009 Section 1 Operations 1 17 Figure 1 14 Setting New Pins...
Page 94: ...3 2 Section 3 Nexgen Electronics Section Rev February 2017 Intentionally Blank Page...
Page 131: ...Section Rev February 2017 Section 3 Nexgen Electronics 3 39 Intentionally Blank...
Page 134: ...3 42 Section 3 Nexgen Electronics Section Rev February 2017 Intentionally Blank Page...
Page 136: ...3 44 Section 3 Nexgen Electronics Section Rev February 2017 Back of 11 x 17 Here...
Page 150: ...3 58 Section 3 Nexgen Electronics Section Rev February 2017 Intentionally Blank Page...
Page 152: ...4 2 Section 4 Pinsetter Cycles Section Rev February 2009 Intentionally Blank Page...
Page 158: ...4 8 Section 4 Pinsetter Cycles Section Rev February 2009 Figure 4 5 Pinsetter Cycles...
Page 176: ...5 2 Section 5 Adjustments Section Rev February 2017 Intentionally Blank Page...
Page 226: ...6 2 Section 6 Troubleshooting Section Rev February 2009 Intentionally Blank Page...
Page 246: ...6 22 Section 6 Troubleshooting Section Rev February 2009 Intentionally Blank...
Page 257: ...Section Rev February 2009 Section 7 Preventative Maintenance 7 11...
Page 284: ...7 38 Section 7 Preventative Maintenance Section Rev February 2009...
Page 286: ...8 2 Section 8 Servicing Section Rev February 2009 Intentionally Blank Page...