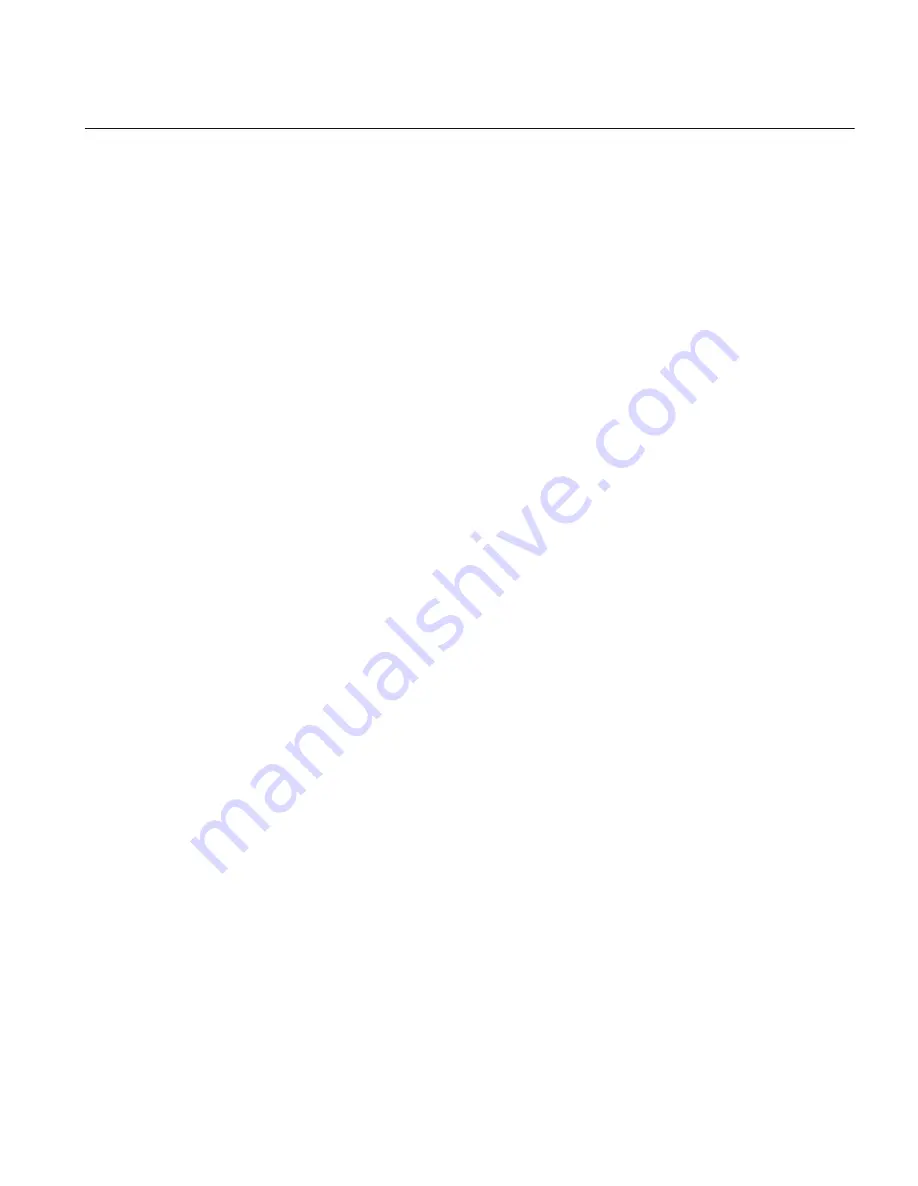
overload protection provides information and makes temporary overloading of
transformers possible.
The permissible load level of a power transformer is highly dependent on the cooling
system of the transformer. There are two main principles:
•
OA: The air is naturally circulated to the coolers without fans and the oil is
naturally circulated without pumps.
•
FOA: The coolers have fans to force air for cooling and pumps to force the
circulation of the transformer oil.
The protection can have two sets of parameters, one for non-forced cooling and one for
forced cooling. Both the permissive steady state loading level as well as the thermal
time constant is influenced by the cooling system of the transformer. The two
parameters sets can be activated by the binary input signal COOLING. This can be
used for transformers where forced cooling can be taken out of operation, for example
at fan or pump faults.
The thermal overload protection estimates the internal heat content of the transformer
(temperature) continuously. This estimation is made by using a thermal model of the
transformer which is based on current measurement.
If the heat content of the protected transformer reaches a set alarm level a signal can be
given to the operator. Two alarm levels are available. This enables preventive actions
in the power system to be taken before dangerous temperatures are reached. If the
temperature continues to increase to the trip value, the protection initiates a trip of the
protected transformer.
After tripping by the thermal overload protection, the transformer will cool down over
time. There will be a time gap before the heat content (temperature) reaches such a
level so that the transformer can be taken into service again. Therefore, the function
will continue to estimate the heat content using a set cooling time constant. Energizing
of the transformer can be blocked until the heat content has reached a set level.
8.8.3
Setting guideline
M13250-3 v8
The parameters for the thermal overload protection, two time constants (TRPTTR, 49)
are set via the local HMI or Protection and Control IED Manager (PCM600).
The following settings can be done for the thermal overload protection:
Operation
:
Disabled
/
Enabled
Operation
: Sets the mode of operation.
Disabled
switches off the complete function.
1MRK 511 401-UUS A
Section 8
Current protection
Bay control REC670 2.2 ANSI
203
Application manual
Summary of Contents for Relion REC670
Page 1: ...RELION 670 SERIES Bay control REC670 Version 2 2 ANSI Application manual ...
Page 2: ......
Page 26: ...20 ...
Page 42: ...36 ...
Page 96: ...90 ...
Page 274: ...268 ...
Page 292: ...286 ...
Page 298: ...292 ...
Page 308: ...302 ...
Page 470: ...464 ...
Page 514: ...508 ...
Page 608: ...602 ...
Page 646: ...640 ...
Page 656: ...650 ...
Page 657: ...651 ...