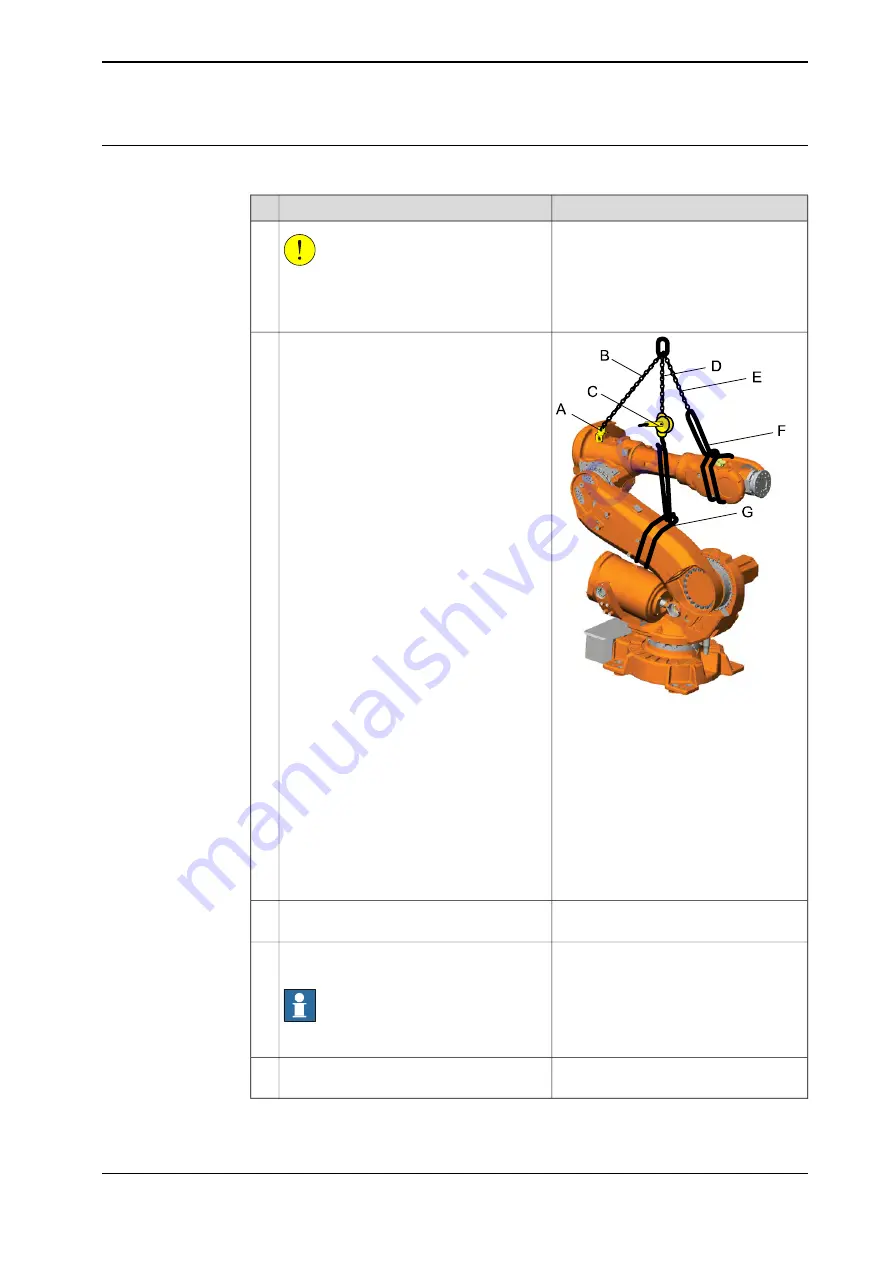
Refitting the armsystem to gearbox axis 2
Use this procedure to refit the armsystem to gearbox axis 2.
Note
Action
CAUTION
The upper and lower arms (incl. gearboxes
axes 2 and 3) weighs 455 kg. All lifting
equipment used must be sized accordingly!
1
xx0700000350
Fit the lifting tool on the upper and lower
arms and secure the robot in an overhead
crane.
2
Parts:
•
A: Lifting eye (armhouse)
•
B: Lifting chain
•
C: Hoisting block
•
D: Lifting chain
•
E: Lifting chain
•
F: Roundsling (put in a loop
around the wrist on the inside)
•
G: Roundsling (put in a loop
around the lower arm
For art. no. see:
•
Required equipment on page 406
Use a
crank
in the gearbox in order to find
the holes for the attahment screws.
3
Tightening torque: 300 Nm.
Secure the lower arm to gearbox axis 2 with
its
attachment screws
and
washers
.
Note
Use new attachment screws and washers.
4
See the figure in:
•
Location of gearbox axis 2 on
page 405
For art. no. see:
•
Required equipment on page 406
Apply Mercasol on all screw heads of the
attachment screws
after
tightening them.
5
Continues on next page
Product manual - IRB 6640 Foundry Prime
417
3HAC040586-001 Revision: N
© Copyright 2011-2018 ABB. All rights reserved.
4 Repair
4.7.2 Replacing gearbox axis 2
Continued
Summary of Contents for IRB 6640 Foundry Prime
Page 1: ...ROBOTICS Product manual IRB 6640 Foundry Prime ...
Page 18: ...This page is intentionally left blank ...
Page 118: ...This page is intentionally left blank ...
Page 438: ...This page is intentionally left blank ...
Page 448: ...This page is intentionally left blank ...
Page 456: ...This page is intentionally left blank ...
Page 486: ...This page is intentionally left blank ...
Page 488: ...This page is intentionally left blank ...
Page 495: ......