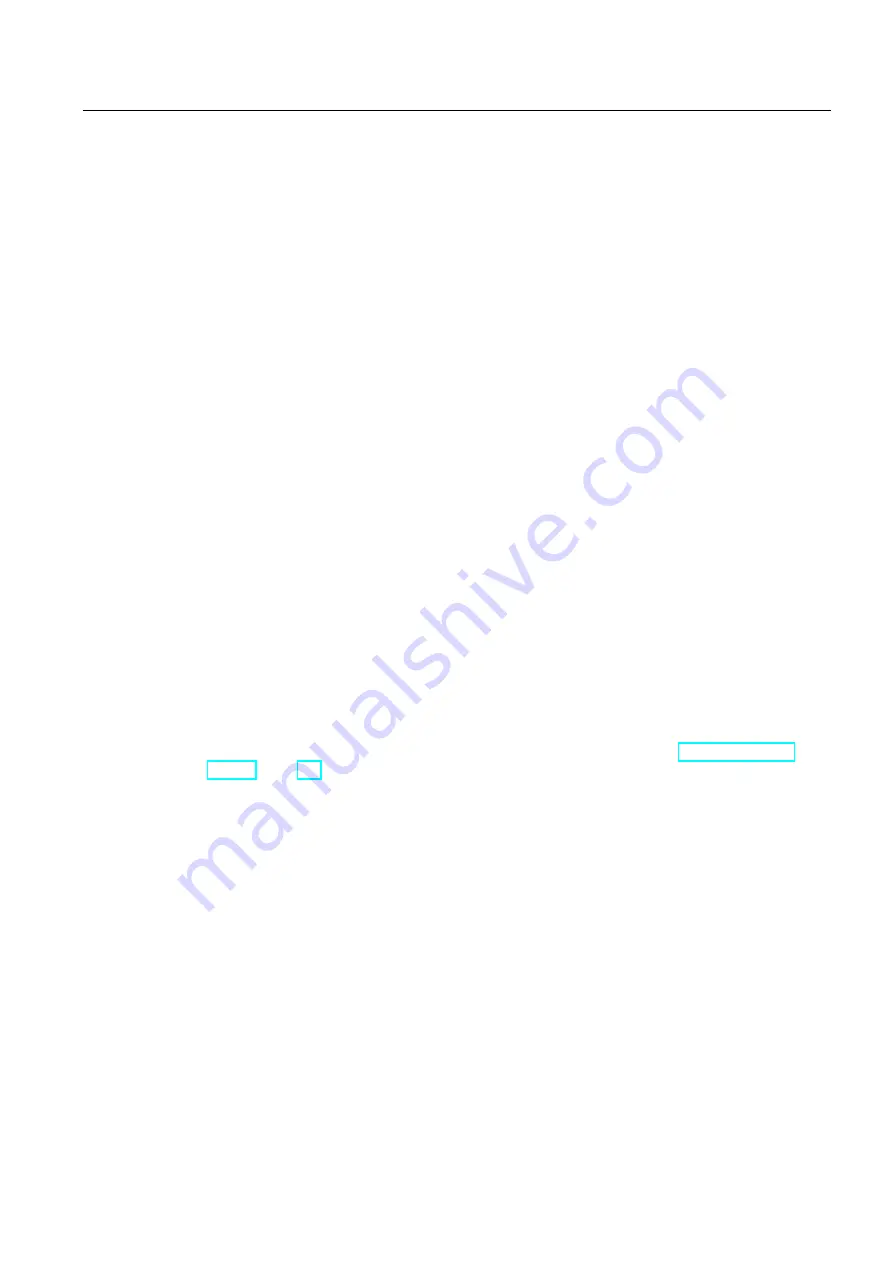
Configuring
6.1 Adding and configuring drives in the device configuration
S7-1500 Motion Control V13 Update 3
Function Manual, 07/2014, A5E03879256-AC
97
Adding and configuring a technology module
1.
Switch to the device view of the PLC.
2.
In the hardware catalog, open the folder "TM > Count > TM Count 2X24V".
3.
Drag the counter module to a free slot in the rack.
4.
Select the technology module in the device view.
5.
In the properties dialog, open the "General" tab and select there "Count 2x24V > Basic
Parameters > Channel X > Operating Mode" of the channel to be used.
6.
Select "Position detection for motion control" option for "Selection of the operating mode
for the channel".
7.
Under "Module parameters", adapt the parameters of the incremental encoder (steps per
revolution = increments per revolution).
8.
Under "Reaction to CPU STOP", select the item "Continue working".
Selecting the drive and encoder in the configuration of the technology object
1.
Add a new positioning axis/synchronous axis technology object, or open the configuration
of an existing positioning axis/synchronous axis.
2.
Open the configuration "Hardware interface > Drive".
3.
Select "Analog drive connection" from the "Drive type" drop-down list.
4.
Select the previously defined tag name of the analog output from the "Output" list.
5.
Open the configuration "Hardware interface > Encoder".
6.
Under "Select encoder coupling" select "Encoder on technology module (TM)".
7.
Select the channel of the incremental encoder from the "Technology module" list under
"local modules".
For information on how to add a technology object, refer to the section Add technology
Result
The analog drive connection and the encoder connection are configured.
The analog addresses and the addresses of the TM module are assigned to the process
image "PIP OB Servo".