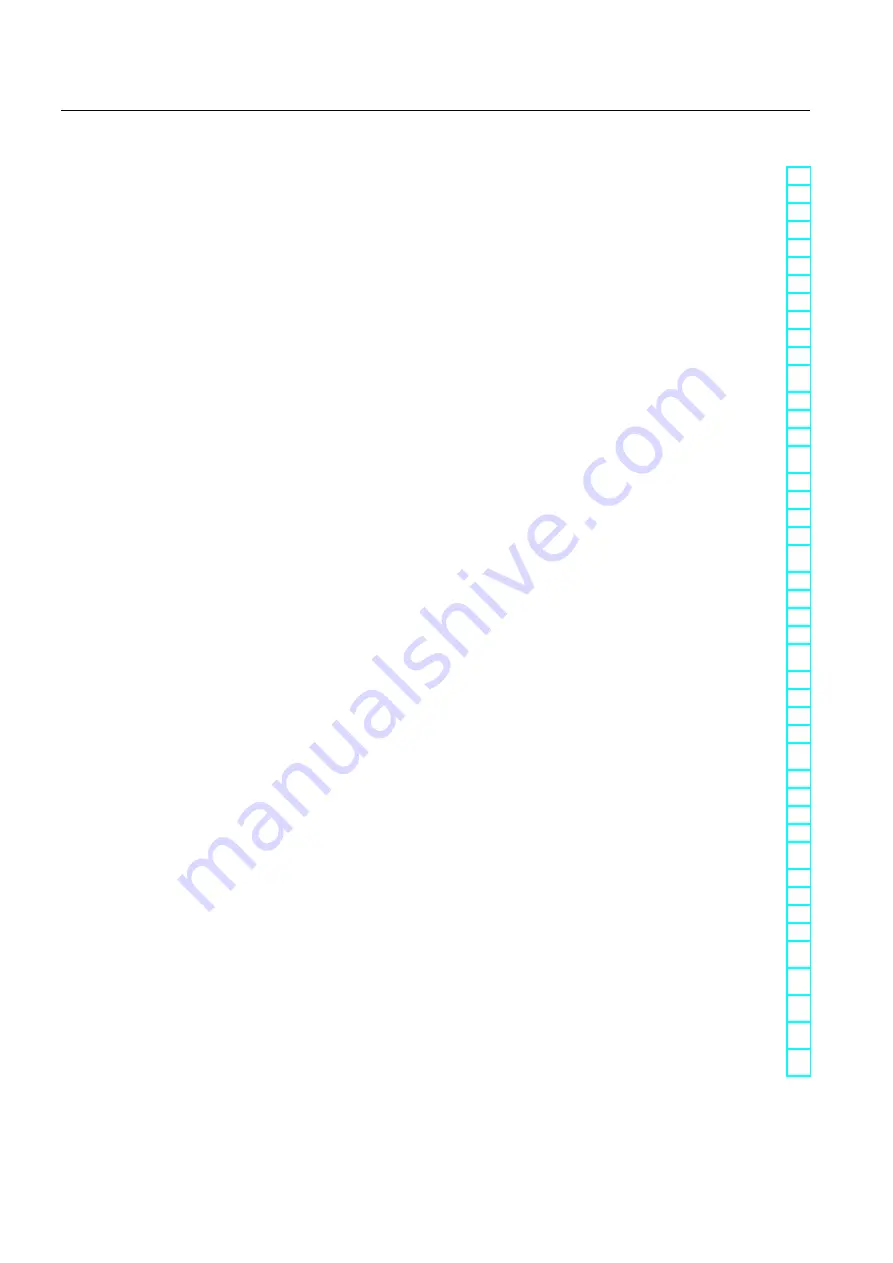
Table of contents
S7-1500 Motion Control V13 Update 3
6
Function Manual, 07/2014, A5E03879256-AC
3.14.4
Active homing with zero mark and proximity switch .............................................................. 43
3.14.5
Active homing with zero mark ................................................................................................ 46
3.14.6
Active homing with digital input .............................................................................................. 48
3.14.7
Passive homing with zero mark and proximity switch ............................................................ 50
3.14.8
Passive homing with zero mark ............................................................................................. 52
3.14.9
Passive homing with digital input ........................................................................................... 54
3.14.10
Direction reversal at the hardware limit switch (reversing cam) ............................................ 55
3.14.11
Direct homing ......................................................................................................................... 56
3.14.12
Absolute value adjustment ..................................................................................................... 56
3.14.13
Resetting the "Homed" status ................................................................................................ 57
3.14.14
Tags ....................................................................................................................................... 58
3.15
Control .................................................................................................................................... 59
3.15.1
Brief description ..................................................................................................................... 59
3.15.2
Control structure..................................................................................................................... 60
3.15.3
Tags ....................................................................................................................................... 61
3.16
Position-related monitoring .................................................................................................... 61
3.16.1
Brief description ..................................................................................................................... 61
3.16.2
Positioning monitoring ............................................................................................................ 62
3.16.3
Following error monitoring ..................................................................................................... 63
3.16.4
Tags ....................................................................................................................................... 64
3.17
Traversing range limitation ..................................................................................................... 65
3.17.1
Brief description ..................................................................................................................... 65
3.17.2
Hardware limit switches ......................................................................................................... 65
3.17.3
Software limit switch .............................................................................................................. 67
3.17.4
Tags ....................................................................................................................................... 68
3.18
Motion control and limits for dynamics ................................................................................... 69
3.18.1
Brief description ..................................................................................................................... 69
3.18.2
Velocity profile ........................................................................................................................ 70
3.18.3
Emergency stop deceleration ................................................................................................ 71
3.18.4
Tags ....................................................................................................................................... 72
3.19
Synchronous operation .......................................................................................................... 73
3.19.1
Brief description ..................................................................................................................... 73
3.19.2
Relative gearing ..................................................................................................................... 74
3.19.3
Master value coupling ............................................................................................................ 76
3.19.4
Tags ....................................................................................................................................... 77
3.20
Operational sequence ............................................................................................................ 78
3.20.1
Organization Blocks for Motion Control ................................................................................. 78
3.20.2
Process image partition "OB Servo PIP" ............................................................................... 80
3.20.3
Operational Sequence and Timeouts .................................................................................... 80
3.20.4
Operating modes ................................................................................................................... 83
4
Guidelines ................................................................................................................................................ 85
4.1
Guidelines on use of motion control....................................................................................... 85
5
Using versions ......................................................................................................................................... 86
5.1
Overview of versions .............................................................................................................. 86
5.2
Changing a technology version .............................................................................................. 89