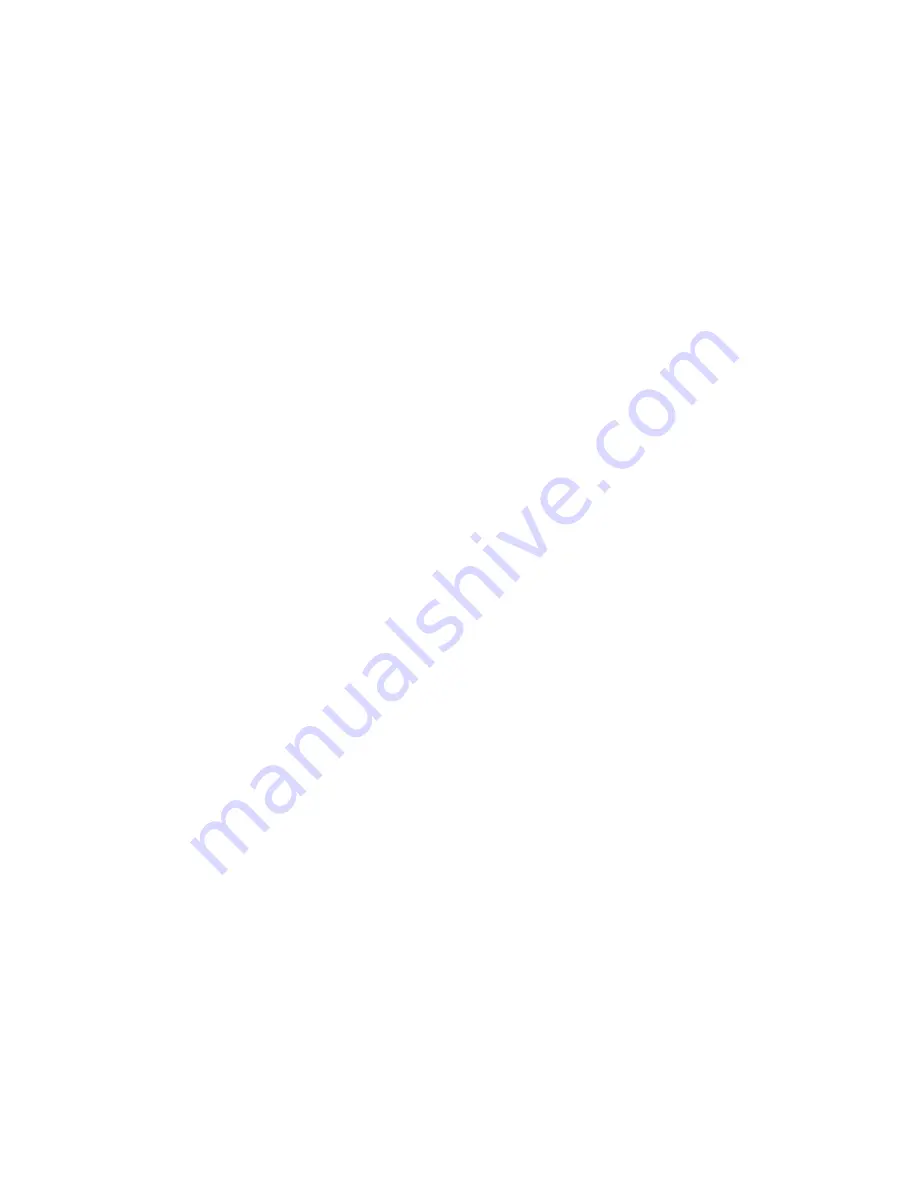
Procedure
1.
If there is also a stacker jam, the forms may have been pushed back into the
sensors. Correct the stacker jam, and ensure that the folding direction of the
forms is set correctly in the stacker and with the
Forms Set
switch. If you need
to clear the stacker jam, see “Clearing a forms jam in the Stacker” on page 234
for instructions.
2.
If this error occurs while doing an auto-load procedure, ensure that the first
sheet is folded over the second sheet. If the leading edge of the form is curled,
this would prevent it from feeding into the scuff rolls.
3.
If the forms are wrapping around the hot roll, the fuser oil feed rate may be set
too low. If they are consistently wrapping around the hot roll, you may need to
set the oil feed rate higher.
4.
Light-weight forms with heavy print density or large areas of solid area fill
may stick to the hot roll if the oil feed rate is too low or if the oiling system has
failed.
5.
Light-weight or slightly damp forms can cause wraps.
Related information:
“Clearing forms jams” on page 230
provides more specific instructions on clearing forms jams.
“Suggestions for preventing jams” on page 245
provides additional suggestions about preventing forms jams.
0093 Input loop paper jam
About this task
Symptom:
The printer is not maintaining the correct paper length on the input
loop. This error was detected by the feed loop sensors (Figure 99 on page 269),
which are located in the forms input area below the transfer station.
Possible causes and suggested recovery actions:
Procedure
1.
The input feed loop sensors and LEDs may be dirty. Check them for paper dust
and clean them if necessary (see “Cleaning the forms input area” on page 264).
2.
Check for paper jams in these areas:
v
At the base of the input area or at the urge unit motor
v
Around the guide roll at the base of the input area of the machine
v
Within the urge unit assembly area
3.
Check that both pinch rollers are properly contacting the drive roller on the
urge unit.
4.
Ensure that the forms are aligned correctly with any preprocessing devices and
ensure that nothing interferes with the paper path.
5.
If a buffer/flipper unit is installed (duplex mode), check that the buffer flipper
is positioned so that the forms are correctly aligned between Printer 1 and the
flipper and between the flipper and Printer 2.
Related information:
“Clearing forms jams” on page 230
provides more specific instructions on clearing forms jams.
“Suggestions for preventing jams” on page 245
provides additional suggestions about preventing forms jams.
Chapter 6. Taking care of problems
227
Содержание InfoPrint 4100 TD3
Страница 1: ...Operating the InfoPrint 4100 InfoPrint 4100 Models TS2 TD3 4 TS3 and TD5 6 S550 1298 02...
Страница 2: ......
Страница 3: ...Operating the InfoPrint 4100 InfoPrint 4100 Models TS2 TD3 4 TS3 and TD5 6 S550 1298 02...
Страница 8: ...vi Operating the InfoPrint 4100...
Страница 12: ...x Operating the InfoPrint 4100...
Страница 14: ...xii Operating the InfoPrint 4100...
Страница 60: ...46 Operating the InfoPrint 4100...
Страница 90: ...6 Open the lower tractor covers on the transfer station g5amc377 1 1 2 3 4 76 Operating the InfoPrint 4100...
Страница 97: ...2 Swing the roller 3 into the open position by pressing down on 1 and 2 Chapter 5 Working with forms 83...
Страница 107: ...4 Open the lower tractor covers on the transfer station ic3mc335 2 4 3 1 Chapter 5 Working with forms 93...
Страница 127: ...2 Swing the roller 3 into the open position by pressing down on 1 and 2 Chapter 5 Working with forms 113...
Страница 140: ...2 Swing the roller 3 into the open position by pressing down on 1 and 2 126 Operating the InfoPrint 4100...
Страница 268: ...254 Operating the InfoPrint 4100...
Страница 360: ...346 Operating the InfoPrint 4100...
Страница 407: ...Administrator panel Chapter 8 Help topics for the InfoPrint 4100 operator console 393...
Страница 408: ...394 Operating the InfoPrint 4100...
Страница 461: ......
Страница 462: ...Program Number 5765 G79 5765 G74 Printed in USA S550 1298 02...