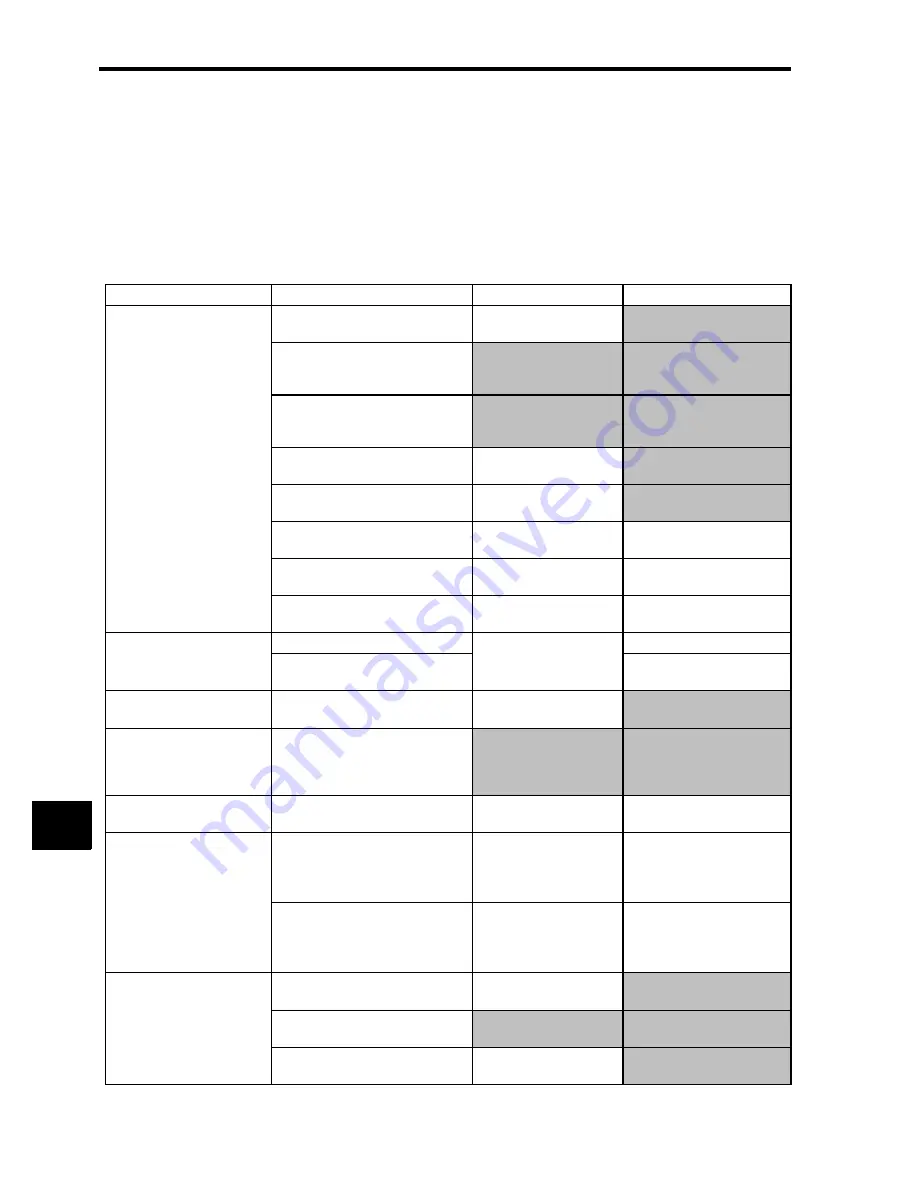
9 Troubleshooting
9-44
9
9.4 Error Diagnosis Due To Operating Status
Refer to the tables below to identify the cause of a problem which causes no alarm display and
take the remedy described.
Turn OFF the servo system power supply before commencing the shaded procedures.
Table 9.3 Troubleshooting Table with No Alarm Display
Symptom
Cause
Inspection
Remedy
Servomotor does not start.
Power not connected
Check voltage between
power supply terminals.
Correct the power circuit.
Loose connection
Check terminals of connec-
tors (CN1, CN2, CN4, and
CN6).
Tighten any loose parts.
Connectors (CN1, CN4, and CN6)
external wiring incorrect
Check connectors (CN1,
CN4, and CN6) external
wiring.
Refer to connection diagram
and correct wiring.
Servomotor or encoder wiring dis-
connected
−
Reconnect wiring.
Overloaded.
Run under no load.
Reduce load or replace with
larger capacity Servomotor.
Encoder type differs from parameter
setting.
Check the type of encoder
being used.
Set parameter Pn002.2 to the
encoder type being used.
POT and NOT inputs are turned OFF. Refer to
8.3
.
Turn POT and NOT input sig-
nals ON.
Software limit reached
Refer to
5.3.3.
Operate the Servomotor within
software limits.
Servomotor does not run.
Move commands have not been sent.
Check using DeviceNet
communications or the
DeviceNet monitor.
Send the move commands.
Servo ON Command has not been
sent.
Send Servo ON Command.
Servomotor moves instanta-
neously, then stops.
Servomotor or encoder wiring incor-
rect.
−
Refer to
chapter 4
Connec-
tors
and correct wiring.
Servomotor speed unstable
Wiring connection to Servomotor is
defective.
Check connection of
phase-U, -V, and -W power
lines and encoder connec-
tors.
Tighten any loose terminals or
connectors.
Servomotor vibrates at ap-
proximately 200 to 400 Hz.
Speed loop gain value is too high.
−
Reduce Speed Loop Gain
(Pn100) preset value.
High rotation speed over-
shoot on starting and stop-
ping
Speed loop gain value is too high.
−
Reduce Speed Loop Gain
(Pn100) preset value.
Increase Speed Loop Integra-
tion Constant (Pn101).
Speed loop gain value too low com-
pared to position loop gain value.
−
Increase Speed Loop Gain
(Pn100) preset value.
Reduce Speed Loop Integra-
tion Constant (Pn101).
Servomotor overheated
Ambient temperature is too high.
Measure Servomotor ambi-
ent temperature.
Reduce ambient temperature to
40
°
C max.
Servomotor surface is dirty.
Visual check
Clean dust and oil from motor
surface.
Overloaded
Run under no load.
Reduce load or replace with
larger capacity Servomotor.
Содержание OMNUC W R88A-NCW152-DRT
Страница 1: ...Cat No I538 E3 1 DeviceNet Option Unit OMNUC W Series Model R88A NCW152 DRT...
Страница 53: ...4 Connectors 4 5 3 DeviceNet Network Configuration Restrictions 4 22 4...
Страница 97: ...5 Parameter Settings 5 3 8 Notch Signal Output Positioning 5 44 5...
Страница 211: ...8 Servo Driver Settings 8 5 3 Absolute Encoder Multi turn Limit Setting 8 24 8...
Страница 257: ...9 Troubleshooting 9 46 9...