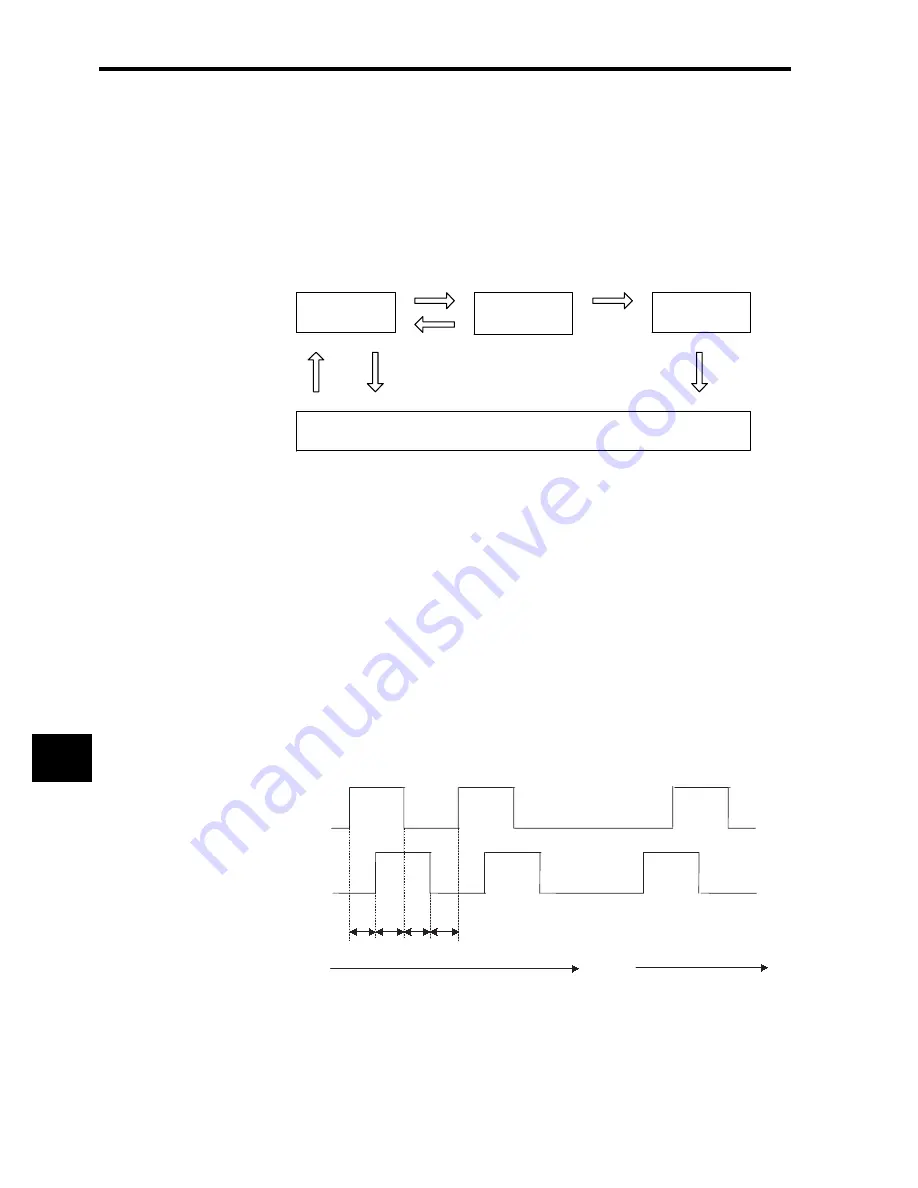
8 Servo Driver Settings
8.2.3 Fully-closed Control
8-10
8
8.2.3 Fully-closed Control
A fully-closed loop can be formed using the parameter settings on the W-series Servo
Driver. In previous Servo Drivers, a semi-closed method was used to control the motor, but
with this function even more precise control is achieved because control involves the detec-
tion of the position and speed of actual machine operation.
Parameters must be set when using fully-closed control. Refer to
Parameter Settings for the
Fully-closed System
on
page 8-11
.
Fully-closed System Specifications
This section describes the fully-closed system specifications of the W-series Servo Driver
when a DeviceNet Unit is mounted.
Fully-closed Encoder Pulse Output Form
5-V Differential line driver output (complies with EIA Standard RS–422A)
Fully-closed Encoder Pulse Signal Form
90
°
Phase difference 2-phase differential pulse: phase A, phase B
Maximum receivable frequency for Servo Driver: 1 Mbit/s
Controlled machine
Servomotor
Mechanism in-
cluding backlash
and friction
Speed and
position at the
machine end
Load torque
Torque
Power
Speed,
position
Detection
current
Current
Fully closed control
Phase A
Phase B
t1, t2, t3, t4
≥
0.2
µ
s
t1
t2
t3
t4
Reverse rotation
Forward rotation
Содержание OMNUC W R88A-NCW152-DRT
Страница 1: ...Cat No I538 E3 1 DeviceNet Option Unit OMNUC W Series Model R88A NCW152 DRT...
Страница 53: ...4 Connectors 4 5 3 DeviceNet Network Configuration Restrictions 4 22 4...
Страница 97: ...5 Parameter Settings 5 3 8 Notch Signal Output Positioning 5 44 5...
Страница 211: ...8 Servo Driver Settings 8 5 3 Absolute Encoder Multi turn Limit Setting 8 24 8...
Страница 257: ...9 Troubleshooting 9 46 9...