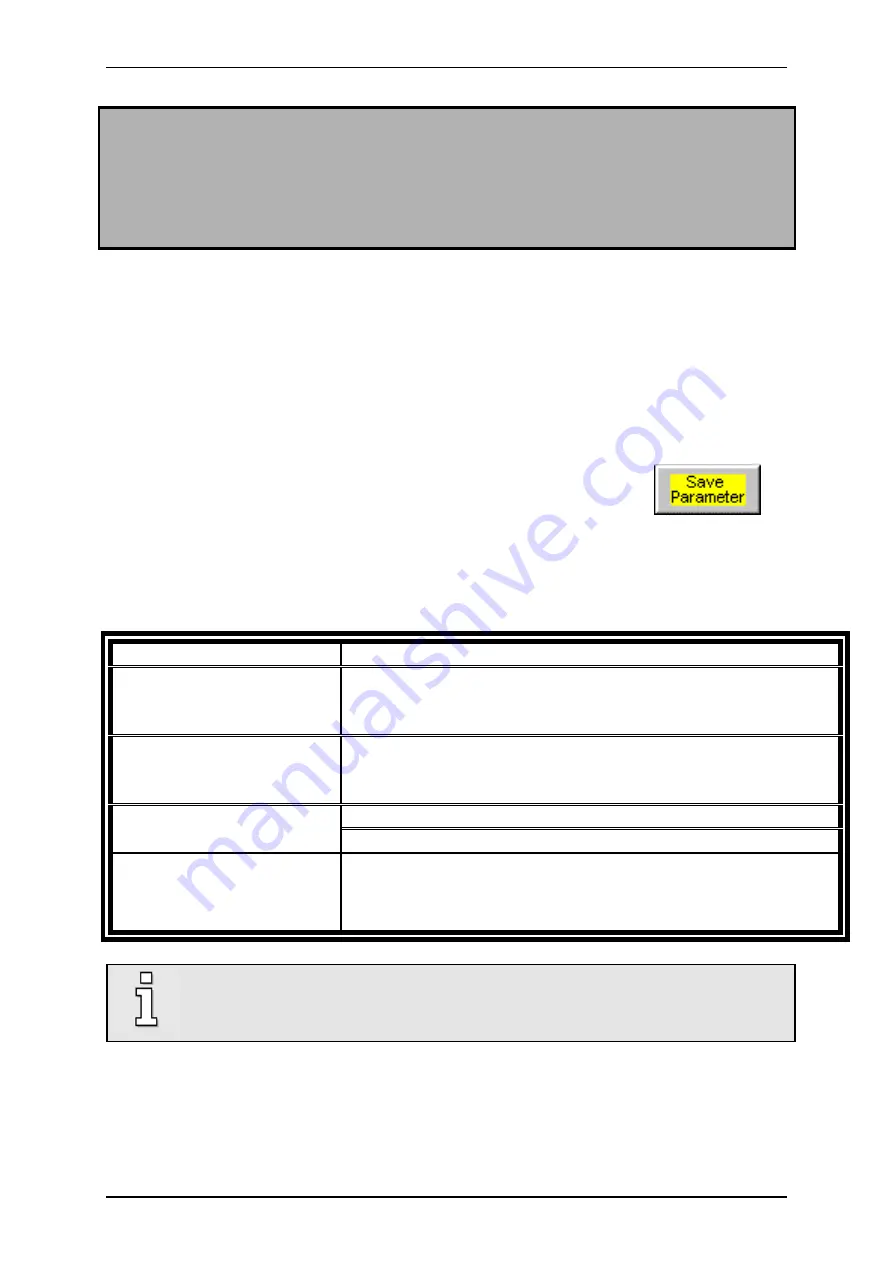
Page 51
Incorrect basic settings may destroy the servo positioning controller / motor and the
mechanical drive!
It has turned out to be useful to set the current limits and particularly the maximum current
of the controller to "small" values (e.g. to half of the rated current), as this prevents strain
on all components including the mechanical system if other drive parameters are
improperly configured.
To let the motor rotate in a speed-controlled manner, you have to configure the following points:
1)
Activate the speed control mode (see
chapter Speed-controlled mode
).
2)
Set the controller enable logic to "via digital input" (see
chapter Configuring the
).
3)
Activate the speed control via the analog input 0 (see
chapter 4.2 Setpoint
assignment through setpoint selectors
) and parametrize the desired analog speed range
(
chapter Analog inputs AIN0 and AIN1
).
If you cannot use the analog input, you can also assign the setpoints via the serial interface
(see
chapter 4.2 Setpoint assignment through setpoint selectors
).
4) Before you test the controller enabling process, you should save the
parameters in the drive. To do so, click the button shown here. You can
find the button on the upper menu bar of the main window.
5) Now briefly activate the controller enabling system.
After the control system has been enabled, the shaft has to start rotating. If the motor does not show
this behaviour, there is either an error or the DUET_FL servo positioning controller has been
parameterized incorrectly. The following table shows typical errors and how you can eliminate them:
Table 7: Error elimination: Speed control
Error
Remedy
The motor develops a holding
torque. It "blocks" in different
positions.
The number of pairs of poles and/or the phase sequence is incorrect. Set the
correct number of pairs of poles and/or interchange the motor phases. Perform
another automatic identification. (See
The motor shaft oscillates or runs
unevenly.
The parametrization of the angle encoder offset (see
chapter Speed-controlled
) and/or the controller parameters are incorrect. Perform another automatic
identification. (See
chapter Angle encoders
The shaft does not rotate.
No intermediate circuit voltage (DC bus voltage).
The limit switches are active.
The shaft does not rotate. The actual
value window still shows a speed
setpoint of "0".
The speed setpoint has not been configured correctly. Further information can be
found in
Setpoint assignment through setpoint selectors
When you are connecting the motor phases, please have mind that the servo motor
manufacturers configure the phase sequences differently. It might be necessary to
interchange the phases U and W.
User Manual DUET_FL „DUET_FL 48/10“
Version 1.1 Motor Power Company
Содержание DUET_FL 48/10
Страница 3: ...ber dieses Handbuch Page 3...
Страница 4: ...Page 4 User Manual DUET_FL DUET_FL 48 10 Version 1 1 Motor Power Company...
Страница 12: ...Page 12 List of Figures User Manual DUET_FL DUET_FL 48 10 Version 1 1 Motor Power Company...
Страница 15: ...Page 15 List of Tables User Manual DUET_FL DUET_FL 48 10 Version 1 1 Motor Power Company...
Страница 76: ...Page 76 User Manual DUET_FL DUET_FL 48 10 Version 1 1 Motor Power Company...
Страница 196: ...Page 196 User Manual DUET_FL DUET_FL 48 10 Version 1 1 Motor Power Company...