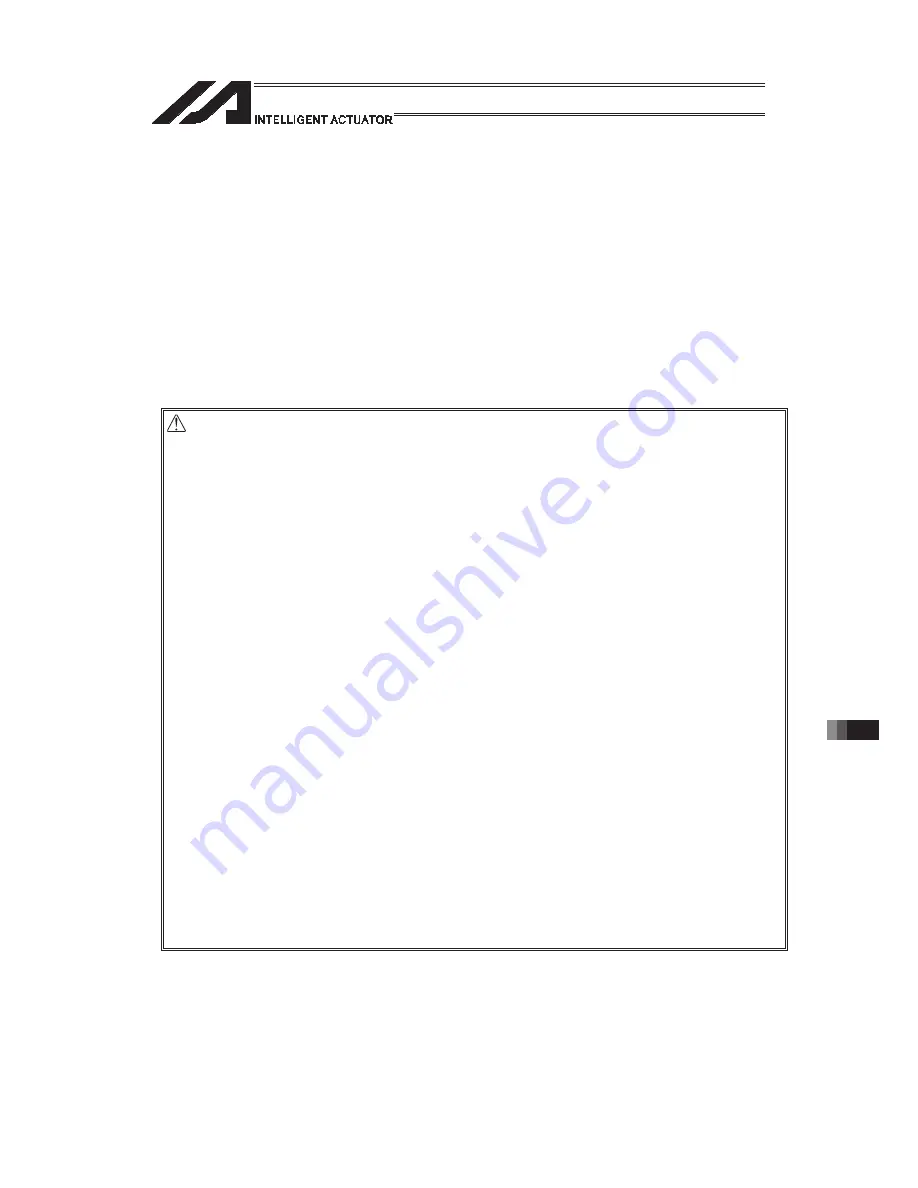
[27] Electronic Cam Control System
531
y
If the master axis is a main CPU control axis or pulse I/O board control axis, set the master
stroke length/stroke end position and master shaft synchronizing start position to the master
shaft position data. If the master shaft is the pulse input channel, set it directly to the variable for
operation settings. Set the slave shaft stroke length to the slave shaft position data.
y
If Stroke Type = Indicate master stroke end position, the master stroke length (1 cycle) on the
electronic cam table is [Master shaft stroke end position-Synchronizing start master shaft
position]. The relation between the master shaft position and the electronic cam table phase is
that the synchronizing start master shaft position is the phase 0, and the direction from the
synchronizing start master shaft position to the master shaft stroke end position is the phase
positive direction.
y
If Stroke Type = Indicate master shaft stroke length, the relation between the master shaft
position and the electronic cam table is that the synchronizing start master shaft position is the
phase 0, and if the stroke length is a positive value, the positive direction on the master axis
coordinate is the phase positive direction and, if the stroke length is a negative value, the
positive direction on the master shaft coordinate is the phase negative direction.
Caution
y
If there is a mistake in the synchronizing electronic cam operation settings specified in the
variables in Operand 2, Error No. 455 “Extension motion control board synchronizing electronic
cam operation setting error” would occur. The variable numbers with an error setting will be
shown on the error list in Info. 2 (in hexadecimal numbers).
y
Variable with an error occurred: Master axis number (Stored variable)
y
The specified master shaft number is inappropriate or invalid
y
The specified master shaft is a synchronized slave shaft or ZR unit shaft
(if the master shaft is a main CPU control shaft)
y
The specified master shaft is the shaft specified as the slave
(if the master shaft is a pulse I/O board control shaft)
y
The specified master shaft is on a different pulse I/O board or channel from that the slave
shaft is on (if the master shaft is a pulse I/O board control shaft or a pulse input channel)
y
Variable with an error occurred: stroke length/stroke end position storage position number
y
The specified position number is inappropriate or position data is invalid
y
If the master shaft type for the synchronizing electronic cam operation settings is the main CPU
control shaft, BASE Command settings would be effective to the master shaft number. Also,
GRP Command settings are invalid to the position data to store the stroke length and stroke
end position.
y
If the robot is equipped with multiple pulse I/O board, the electronic cam table which is stored
to the board that the slave shaft is connected to would be used.
y
If the slave shaft starts to move for a synchronizing process during the master shaft is in move,
the speed and acceleration/deceleration may get too high and may cause an error. Lower the
settings for the speed and acceleration of the master shaft during the slave synchronizing
movement starts.
y
During a movement following the electronic cam table, the speed and acceleration/deceleration
may get too high and may cause an error. Change the settings for the speed,
acceleration/deceleration and electronic cam table so they are set to the allowable speed and
acceleration/deceleration for the shaft.
Содержание PSEL
Страница 2: ......
Страница 10: ......
Страница 18: ...8 Part 1 Installation ...
Страница 37: ...27 Part 1 Installation 2 2 axis specification with battery ...
Страница 382: ...372 Appendix Micro cylinder RCL Series Current limiting value ratio Push force N ...
Страница 476: ...466 Appendix ...
Страница 480: ...470 ...
Страница 485: ...475 ...
Страница 487: ...INTELLIGENT ACTUATOR SEL Language Programming Manual Eighth Edition ...
Страница 488: ......
Страница 490: ......
Страница 494: ......
Страница 518: ...24 ...
Страница 526: ...32 ...
Страница 831: ... 11 Actuator Control Declaration 337 Example DFIF 1 170 ...
Страница 1060: ......
Страница 1061: ......