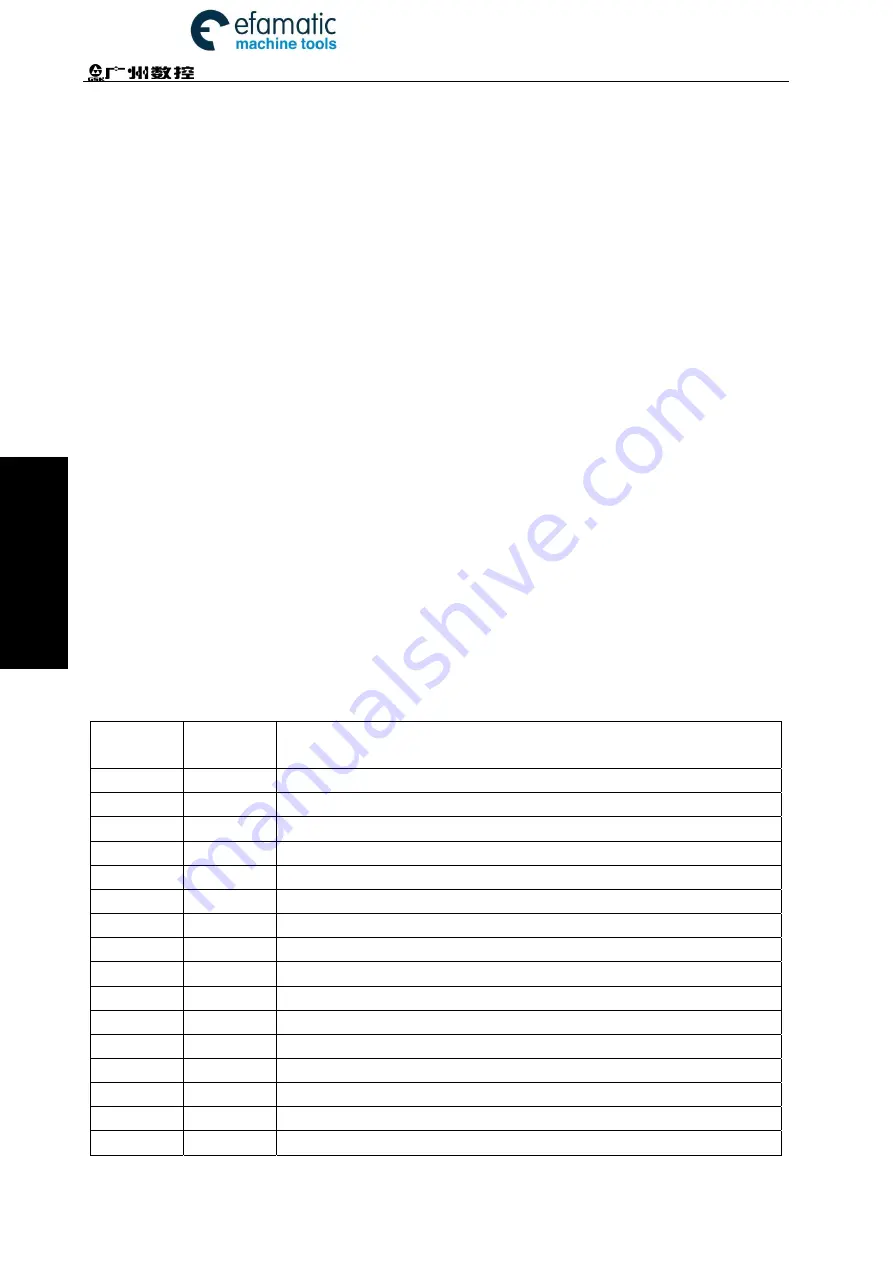
Official GSK Agents in South Africa
Tel: +27 11 626 2720, [email protected]
GSK218MC Series Machining Center CNC System PLC&Installation Connetion Manual
252
Appendix
4. The K008.1 is disabled when K008.2=0 (That is, do not use the tool clamping/releasing
equipment).
5. The precautions when K006.0 is set.
Install 2 stroke limit switches of each axis when K006.0 is set to 0.
For example:
install two stroke limit switches along with the X axis (+ limit switch
connect with the X0. 0; - one connects with the X0. 1).
when K006.0 is set to 1, the stroke limit switch of each axis is only installed one.
For example:
install one stroke limit switch along with the X axis (It must be
connected with the X0.0).
The other installation methods of each axis are identical.
6. The overall alarm interlocking are released when K005.2=1, the system is then entered
the debugging mode, which is only use for the system testing. Normally, the parameter
should be set to 0, otherwise, unexpected accident may occur.
7. The parameters such as the K010.1, K010.2, K010.3, K010.4, K010.5, K010.6, K010.7,
K011.1 and K011.2 are related with the tool magazine; refer to the use of the tool
magazine and maintenance at the part III.
8. The setting of the K008.4 (Whether the spindle is with the shifting equipment) is disabled
when K004.0 (Whether the spindle is used the I/O point control) =1; that is, the spindle is
without the shifting device.
Table four The definition of the PLC external alarm
PLC
alarm No.
Add. A
Alarm content
1200
A000.0
Abnormal air pressure detection
1201 A000.1
Abnormal
lubrication grease detection
1202 A000.2
Abnormal
lubrication motor detection
1203
A000.3
Abnormal cooling motor detection
1204
A000.4
Abnormal chip-removal motor detection
1205
A000.5
Abnormal pressure oil-pump motor detection
1207
A000.7
Abnormal machine tool illumination lamp detection
1208
A001.0
Abnormal machine control cabinet temperature detection
1209 A001.1
Abnormal
machine
body temperature detection
1210
A001.2
Abnormal machine vibration frequency detection
1211 A001.3
Abnormal
pressure
grease temperature detection
1212
A001.4
Excessive low grease pressure
1213
A001.5
Fail to ready for the machine tool
1214
A001.6
Spindle shifting abnormal, fail to rotate
1215
A001.7
Firstly perform the T code when executing the M06 code
1216
A002.0
Cutter releasing, fail to rotate the spindle