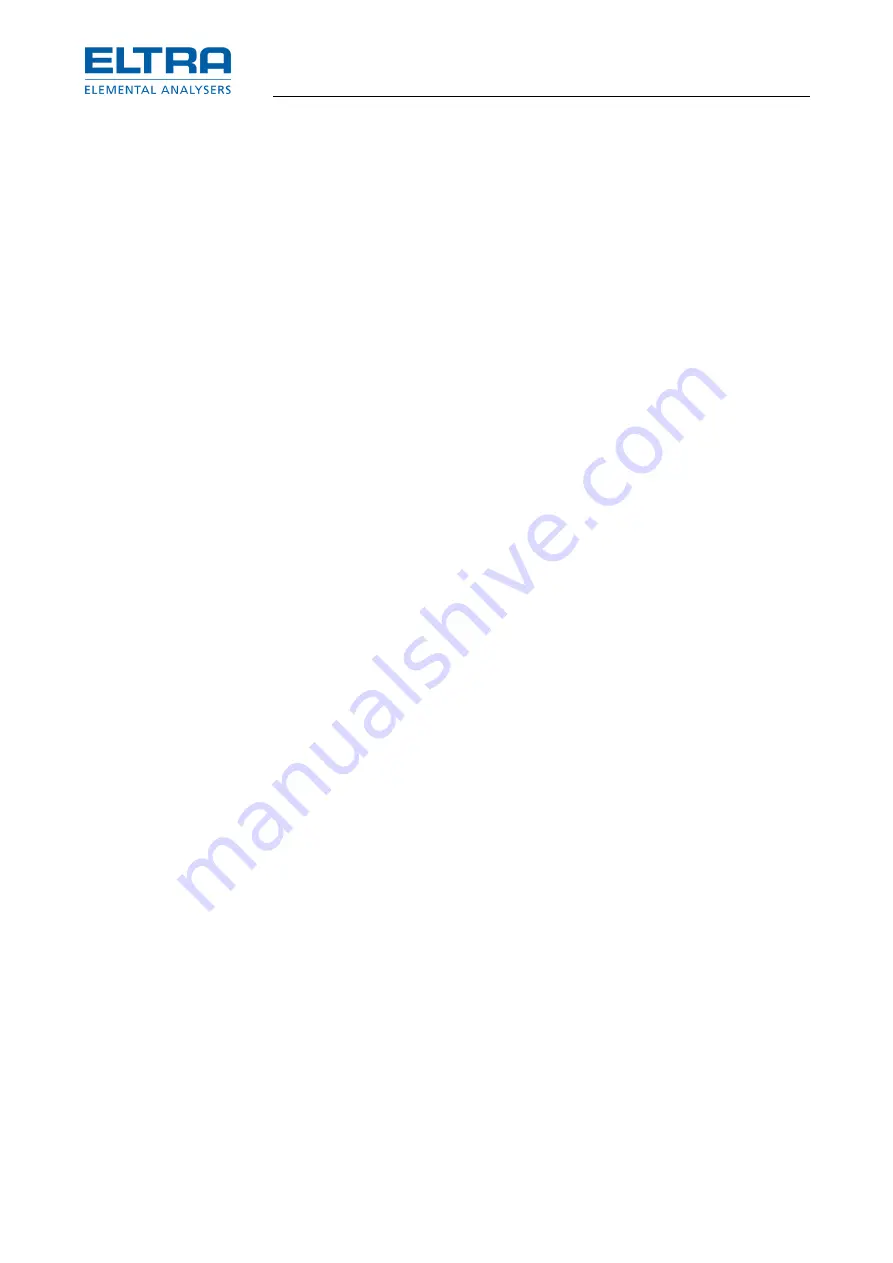
Faults
16
Push the tube (
1
) through the upper glass tube assembly (
2
), pass it through the tube (
3
) up to
the inside of the dust trap box (
4
).
This should be done when the glass tube has to be removed anyway, for replacing the
magnesium perchlorate (anhydrone). See also ope
ration manual, chapter “
Dust cleaning”.
Too low oxygen pressure:
Check the oxygen gauge (6). The reading should be 1.5 bar (22.5psi). If the pressure is too low,
it can be adjusted by pulling and turning clockwise the knob of the pressure regulator on the
rear panel of the analyzer. It is placed on the left hand side and the knob is accessible from
inside the analyzer. An adjustment is possible provided that there is sufficient pressure at the
input of this pressure regulator.
Outlet tap of the oxygen bottle is not properly open:
It is important to properly open the small tap at the outlet of the pressure regulator of the oxygen
bottle. If this outlet tap of the regulator is not properly open, you may have enough pressure at
the analyzer when there is no or little oxygen demand. But when the oxygen demand grows, for
example at the beginning of combustion in the
induction furnace when the sample needs a lot of oxygen to burn, the pressure may drop to a
very low level if not enough oxygen can be supplied to the analyzer at the moment of high
oxygen demand. The same problem will appear during furnace purging before or after the
analysis, depending on the actual settings in the software.
Contaminated or corroded solenoid valve:
In case of exceptional materials like ores, solenoid valves can be contaminated up to the extent
of failing. This depends mainly on the amount of sulfur and moisture in the sample. The most
affected valves are the outflow valve V1 and the bypass valve V4 in as well as the valves
switching from Induction to resistance furnace V11 and V12. See chapter “
Gas flow system
”.
The resistance furnace operation can only contaminate V11 and V12. The valves can be
cleaned.
Faulty oxygen regulator:
A faulty oxygen regulator can of course cause a similar problem when it does not keep the
pressure level at moments of higher oxygen consumption.
Bent plastic tube of oxygen supply:
When the plastic tube supplying oxygen from the bottle to the analyzer is bent, there will be the
same problem like described in the above two subjects. There will be too low oxygen pressure
in the analyzer, especially at moments of high oxygen consumption, like when burning samples
or purging the furnace.
Oxygen supply is interchanged with the compressed air supply:
In case of reported bad combustion, check for correct connection of oxygen and compressed air
supply. Compressed air in the induction furnace will provide combustion but a bad one, because
of only 20% of oxygen existing in the air. Therefore the peaks are low and long, consisting of
more than one peak, looking like mountains.
CAUTION
Oxygen to the compressed air inlet can lead to the explosion of the pneumatic
cylinder.
Blocked dust filter cartridge:
The dust filter cartridge is on the front panel so that contamination is visible for the operator. In
the gas flow circuit, this dust cartridge is connected after the metal filter and its following glass
tube with magnesium perchlorate, so that the carrier gas passing through the cartridge is
already filtered.
Содержание CS-2000
Страница 2: ...2 Copyright Copyright by Eltra GmbH Retsch Allee 1 5 D 42781 Haan Germany ...
Страница 6: ...Notes on service instructions 6 ...
Страница 72: ...Adjustments 72 Fig 57 Gas flow regulation The flow controller mainly consists of the following components ...
Страница 77: ...Adjustments 77 Fig 61 IRC 1 3 ...
Страница 107: ...Service 107 Fig 91 Tubes to squeeze ...
Страница 120: ...Miscellaneous 120 6 1 2 Left hand side Fig 106 Left hand side view ...
Страница 122: ...Miscellaneous 122 6 1 3 Right hand side Fig 107 Right hand side view ...
Страница 129: ...Miscellaneous 129 6 1 7 Infrared cell Fig 111 Infrared cell ...
Страница 139: ...Miscellaneous 139 Fig 119 Left hand side power wiring 6 2 3 Valve wiring ...
Страница 140: ...Miscellaneous 140 Fig 120 Valve wiring 6 2 4 Control signal wiring Fig 121 Control signal wiring ...
Страница 142: ...Miscellaneous 142 6 2 6 IR cell internal signals Fig 123 IR current supply new version ...
Страница 145: ...Miscellaneous 145 6 3 2 Gas flow for induction furnace when furnace is open ...
Страница 146: ...Miscellaneous 146 6 3 3 Gas flow for resistance furnace ...
Страница 147: ...Miscellaneous 147 6 3 4 Valve contolling ...
Страница 160: ...Copyright Copyright by Eltra GmbH Retsch Allee 1 5 D 42781 Haan Germany ...