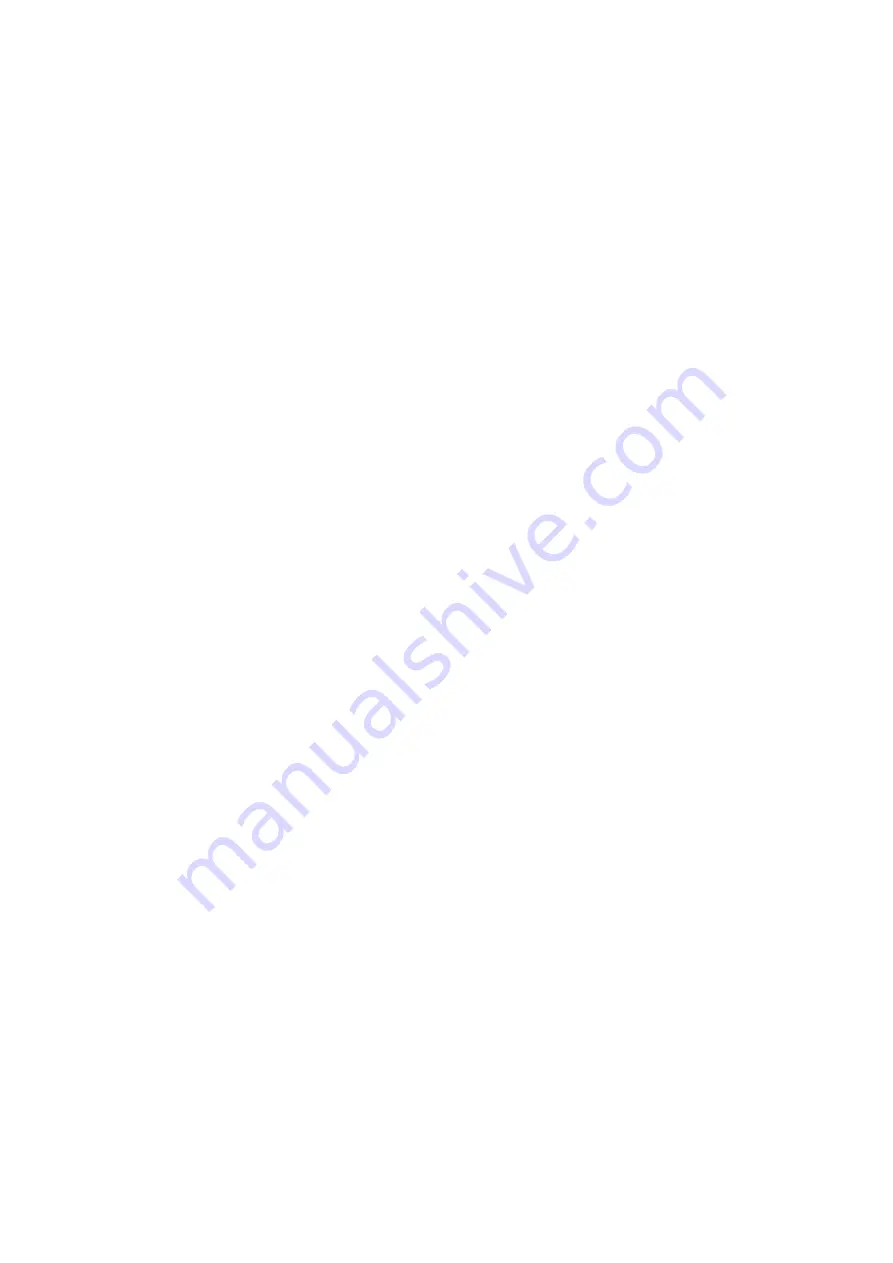
Inspection Preparation, Setup and Operation
37
During the calibration procedure please be aware the following important points:
•
For safety reasons, when performing a calibration, the FloormapX must be set at the slowest
speed setting.
•
The leakage field from non-calibration defects will vary dependent upon diameter, shape, and
volume as well as depth. It is essential that a range of defects detected in the inspection
surface are cross checked with ultrasonic testing or pit depth measurement. This ensures the
calibration is suitable for the type of corrosion present in the inspection surface.
•
All calibration procedures must be carried out on a MFL reference plate manufactured in
accordance with the appropriate Eddyfi drawing, of the same thickness as the floor plates to
be tested. The standard MFL reference plate thicknesses are 6mm, 8mm, 10mm, 12mm, 1/4in,
5/16in, 3/8in and 1/2in.
•
Once calibrated, the FloormapX calibration is only valid for that configuration. Therefore, if on
any single track there exists any variation in the inspection surface, plate, or coating thickness,
or if the scanner bridge height has changed then this must be considered. Another calibration
is required to inspect that variation.
NOTE
In some cases, the true thickness of the tank floor plates being inspected may not be the
identical thickness as the standard MFL reference plates.
Inspection Surface Thicknesses
Knowing the inspection surface thickness and selecting the correct reference plate for calibration is
vital to obtaining optimal results when using the FloormapX system. When the inspection surface is:
•
The same thickness as the reference plate used in calibration, then optimal results can be
achieved by the system. This is the ideal case.
•
Thicker than the reference plate used in calibration, the system will likely be under sensitive.
This reduces the detection capabilities of the system, and defects would likely be undersized.
This is worst case.
•
Thinner than the reference plate used in calibration, the system will likely be oversensitive. This
increases the chance of spurious defects, and defects would likely be oversized.
IMPORTANT
The reference plate must not be in contact with any other ferromagnetic material while the
calibration is being carried out.
When the coating is more than 0.5mm (20mils) on the tank floor, this must be simulated during the
calibration procedure by placing a piece of non-magnetic material, which maintains the same
thickness as the coating on the floor,
between the scanner and the reference plate.
IMPORTANT
For accurate sizing it is important that the reference plate matches the inspection surface as
closely as possible in terms of material composition, thickness, and coating.
3.4
In Tank Inspection Setup
1.
Erect suitable lighting within the storage tank. This can aid the FloormapX operator to identify
markings and hazards.
2.
Investigate the tank environment and find details on the condition and history of the storage
tank to be inspected. Details such as:
Содержание Floormap X
Страница 1: ...User s Manual Floormap X MFL Array Tank Floor Inspection Solution...
Страница 10: ...10 Chapter 1 Precautions and conventions...
Страница 16: ...General Precautions and Conventions 16 1 5 EU Declaration of Conformity...
Страница 19: ...19 Chapter 2 FloormapX System Overview...
Страница 35: ...35 Chapter 3 Inspection Preparation Setup and Operation...
Страница 43: ...43 Chapter 4 SIMS GO Data Acquisition Software...
Страница 69: ...69 Chapter 5 SIMS PRO...
Страница 98: ...98 Chapter 6 Troubleshooting and Maintenance...