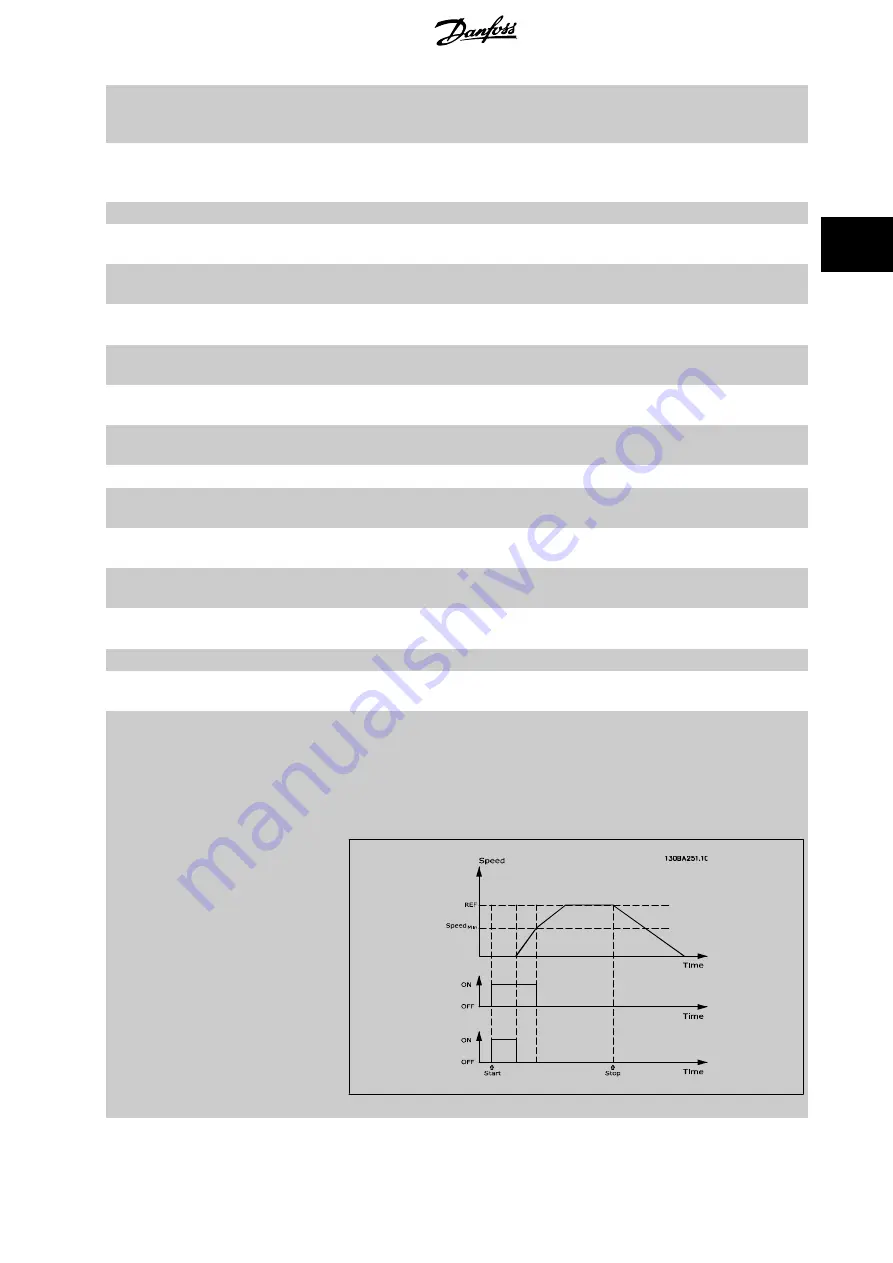
[84]
SL Digital Output E
See par. 13-52
SL Control Action
. The input will go high whenever the Smart Logic Action [42]
Set
dig. out. E high
is executed. The input will go low whenever the Smart Logic Action [36]
Set dig.
out. E low
is executed.
[85]
SL Digital Output F
See par. 13-52
SL Control Action
. The input will go high whenever the Smart Logic Action [43]
Set
dig. out. F high
is executed. The input will go low whenever the Smart Logic Action [37]
Set dig.
out. F low
is executed.
[160]
No alarm
The output is high when no alarm is present.
[161]
Running reverse
The output is high when the frequency converter is running counter clockwise (the logical product
of the status bits ‘running’ AND ‘reverse’).
[165]
Local reference active
The output is high when par. 3-13
Reference Site
= [2] Local or when par. 3-13
Reference Site
=
[0]
Linked to hand auto
at the same time as the LCP is in Hand on mode.
[166]
Remote reference active
The output is high when par. 3-13
Reference Site = Remote
[1] or
Linked to hand/auto
[0] while
the LCP is in [Auto on] mode.
[167]
Start command active
The output is high when there is an active Start command (i.e. via digital input bus connection or
[Hand on] or [Auto on], and no Stop or Start command is active.
[168]
Drive in hand mode
The output is high when the frequency converter is in Hand on mode (as indicated by the LED light
above [Hand on].
[169]
Drive in auto mode
The output is high when the frequency converter is in Hand on mode (as indicated by the LED light
above [Auto on].
[180]
Clock Fault
The clock function has been reset to default (2000-01-01) because of a power failure.
[181]
Preventive Maintenance
One or more of the Preventive Maintenance Events programmed in par. 23-10, Preventive Mainte-
nance Item, has passed the time for the specified action in par. 23-11, Maintenance Action.
[190]
No-Flow
A No-Flow situation or Minimum Speed situation has been detected if enabled in
Minimum Speed
Detection
. par. 22-21 and/or
No-Flow Detection
, par. 22-22.
[191]
Dry Pump
A Dry Pump condition has been detected. This function must be enabled in par. 22-26, Dry Pump
Function.
[192]
End of Curve
A pump running with max. speed for a period of time without reaching the set pressure has been
detected. To enable this function please see
par. 22-50 End of Curve Function
.
[193]
Sleep Mode
The frequency converter/system has turned into sleep mode. See
Sleep mode
, par. 22-4*.
[194]
Broken Belt
A Broken Belt condition has been detected. This function must be enabled in par. 22-60, Broken
Belt Detection.
[195]
Bypass Valve Control
The bypass valve control (Digital / Relay output in the frequency converter) is used for compressor
systems to unload the compressor during start-up by using a bypass valve. After the start command
is given the bypass valve will be open until the frequency converter reaches
Motor speed low lim-
it
, par. 4 -11) . After the limit has been reached the bypass valve will be closed, allowing the
compressor to operate normally. This procedure will not be activated again before a new start is
initiated and the frequency converter speed is zero during the receiving of start signal.
Start De-
lay
, par. 1-71 can be used in order to delay the motor start. The Bypass valve control principle:
ADAP-KOOL
®
Drive Programming Guide
3 Parameter Description
MG.11.N1.02 - VLT
®
is a registered Danfoss trademark
75
3
Содержание ADAP-KOOL Drive
Страница 14: ...2 How to Programme ADAP KOOL Drive Programming Guide 14 MG 11 N1 02 VLT is a registered Danfoss trademark 2...
Страница 201: ...ADAP KOOL Drive Programming Guide 3 Parameter Description MG 11 N1 02 VLT is a registered Danfoss trademark 201 3...
Страница 222: ...4 Parameter Lists ADAP KOOL Drive Programming Guide 222 MG 11 N1 02 VLT is a registered Danfoss trademark 4...