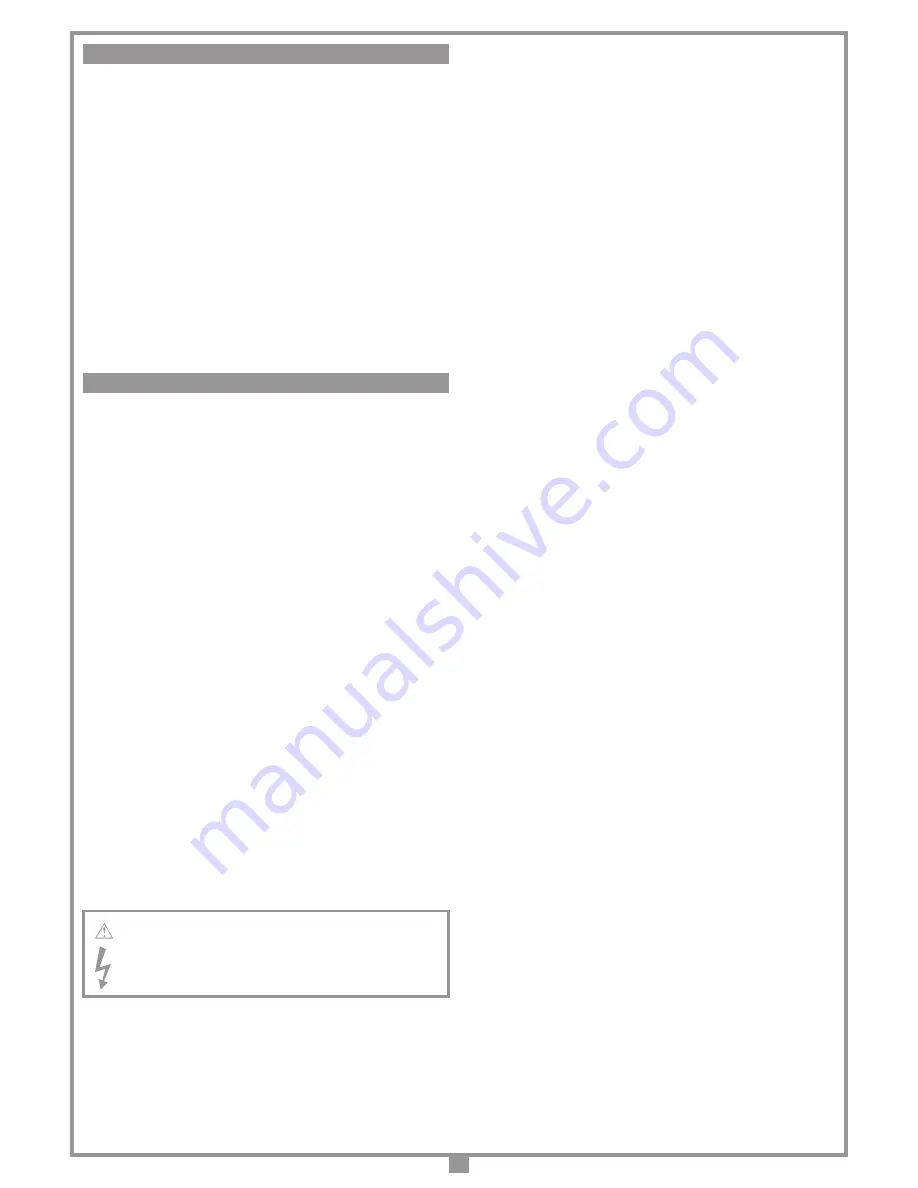
12
Electronic programmer for a direct current motor with an incorporated
radio receiver card, which allows the memorisation of
300 user codes
(see "Remote Control" on page 16).
The "rolling code" type decoder uses
433,92 MHz.
series transmitters.
The travel speed is electronically controlled, starting slowly and increasing
in speed; the speed is reduced as it nears the travel limit so as to enable
a controlled smooth stop (if deceleration hasn’t been excluded during
programming).
Programming is carried out using two buttons and allows you to configure
the system, set the length of the deceleration stage and set the work and
pause times.
The intervention of the anticrush/antidrag sensor during the closing and
opening stages causes travel direction inversion (if automatic reclosing
has been abilitated). If activated towards the end of the movement (almost
closed) it will act as a travel limit.
ELECTRICAL CONNECTION
• Open the "
Standard wiring diagram
". To make it easier to follow the
instructions the diagram has been placed on the inside of the last page
of this manual.
B1
Signal buzzer "
via radio
" mode
CN1
Secondary Faston connection
24 Vac
logic card power supply
CN2
Secondary Faston connection motor circuit power supply
V0: 0 Vac
,
V1: 22 Vac
,
V2: 30 Vac
CN3
Battery Faston connection
D1
Seven segment display
F1
1,6A
delayed action fuse (
230V
power supply protection)
F2
1A
rapid action fuse (
24V
circuit protection)
F3
10A
rapid action fuse (motor power supply protection)
J1
Enable transmitter memorisation via radio
L1
LED power on
L2
LED transmitter code programming
L3
LED manual operation mode
L4
LED inverting photocells activated
L5
LED opening travel limit
L6
LED closing travel limit
L7
LED blocking button activated
L8
LED stop photocell activated
M1
Memory module
P1
Programming button (PROG)
P2
Selection button (SEL)
P3
Transmitter code memorization button (MEMO)
P4
Transmitter code cancellation button (DEL)
R1
Radio frequency module,
433,92 MHz
for
S449
transmitters
LP
Flashing warning lights
LS
Indicator light
FCA
Opening travel limit
FCC
Closing travel limit
FTC-RX
Photocell receiver
FTC-Tx
Photocell transmitter
PS
Safety buffer pressure switch
SEL
Selector switch
TB
Blocking button
ANS400
External antenna
Before connecting the appliance make sure that the voltage and
frequency rated on the data plate conform to those of the mains
supply. A multiple pole trip switch with at least
3mm
between
the contacts must be installed between the unit and the mains
supply.
• Connect the control and security device wires.
• Connect the power supply cable to the device.
• Do not use cables with aluminium conductors; do not solder the ends of
cables which are to be inserted into the binding posts; use cables which
are marked "
T
min
85°C
" and are resistant to atmospheric agents.
• The terminal wires must be positioned in such a way that both the wire
and the insulating sheath are tightly fastened. Where possible use the
supplied cable clamp. The cable entry hole "
11
" (fig.3, pag.11) must be
sealed using a rubber cable clamp or similar.
ELECTRONIC PROGRAMMER
Terminal board connection
1-2
Common for all inputs and outputs
3
24 Vac 7W
in output, powering external devices
4-5
Common for all inputs and outputs
6
24 Vac 10W
in output warning lights
(intermittent or continuous activation)
7
TD
(contact N.O.) Dynamic button input "Open-Close"
8
TB
(contact N.C.) Blocking button input
(The opening of this contact interrupts the cycle until a new move-
ment command is given)
9-17
Common for all inputs and outputs
10
FCC
(contact N.C.) closing travel limit switch
11
FCA
(contact N.C.) opening travel limit switch
12
FTC_I
(contact N.C.) Safety and control devices in input
(these photocells invert the travel direction when an obstruction
is detected).
The opening of this contact will provoke a travel direction inversion
during closure due to the cutting in of the safety device
13
FTC
_S
(contact N.C.) Safety and control devices in input. (stop photo-
electric cells). The opening of this contact will block all movement, until
the obstruction has been removed and the pause time has elapsed,
due to the safety device cutting in, the door will then continue moving
in the closing direction (only with automatic reclosing enabled).
14
TC
(contact normally open) Closing button in input
15
TA
(contact normally open) Opening button in input
16
TAL
(contact normally open) limited opening button
18
Indicator light
24 Vac 3W
19-20
230Vac 60Hz
output powering the toroidal transformer
21-22 Power supply
230Vac 60 Hz
23-24
230Vac 40W
Courtesy light in output
25
Programmer earthing wire
26
Motor earth outputs (not used)
27
Mass for radio receiver antenna
28
Pole for radio receiver antenna (if an external antenna is fitted use
a coaxial type cable
RG58
with an impedance of
50Ω
)
NOTE: ALL UNUSED NC CONTACTS MUST BE JUMPED
Switch on the power and make sure that the red indicator LEDS are in the
following condition:
- L1
Power on LED
on
- L2
Transmitter code programming LED
off
- L3
Manual operation mode LED
off
- L4
Safety LED for the inverting photoelectric cells "
FTC_I
"
on
- L5
Opening direction travel limit LED "
FCA
"
on*
- L6
Closing direction travel limit LED "
FCC
"
on*
- L7
Safety LED for the blocking button "
TB
"
on
- L8
Safety LED for the stop photoelectric cells "
FTC_S
"
on
* The LEDs are "ON" if the relative security device is inactive (depends on
the position of the door). Check that the activation of the safety devices
switches the corresponding LEDS off.
If the
red power on LED doesn't light up
check the condition of the fuses
"
F1
" and "
F2
" and the power cable connection between binding posts
"
21
" and "
22
" (fig. 9).
If one or more of the
safety LEDS do not light up
check the contacts
of the relative security devices and check that the unused safety device
contacts have been bridged.
ELECTRONIC CARD DESCRIPTION
(
fig. 9
)