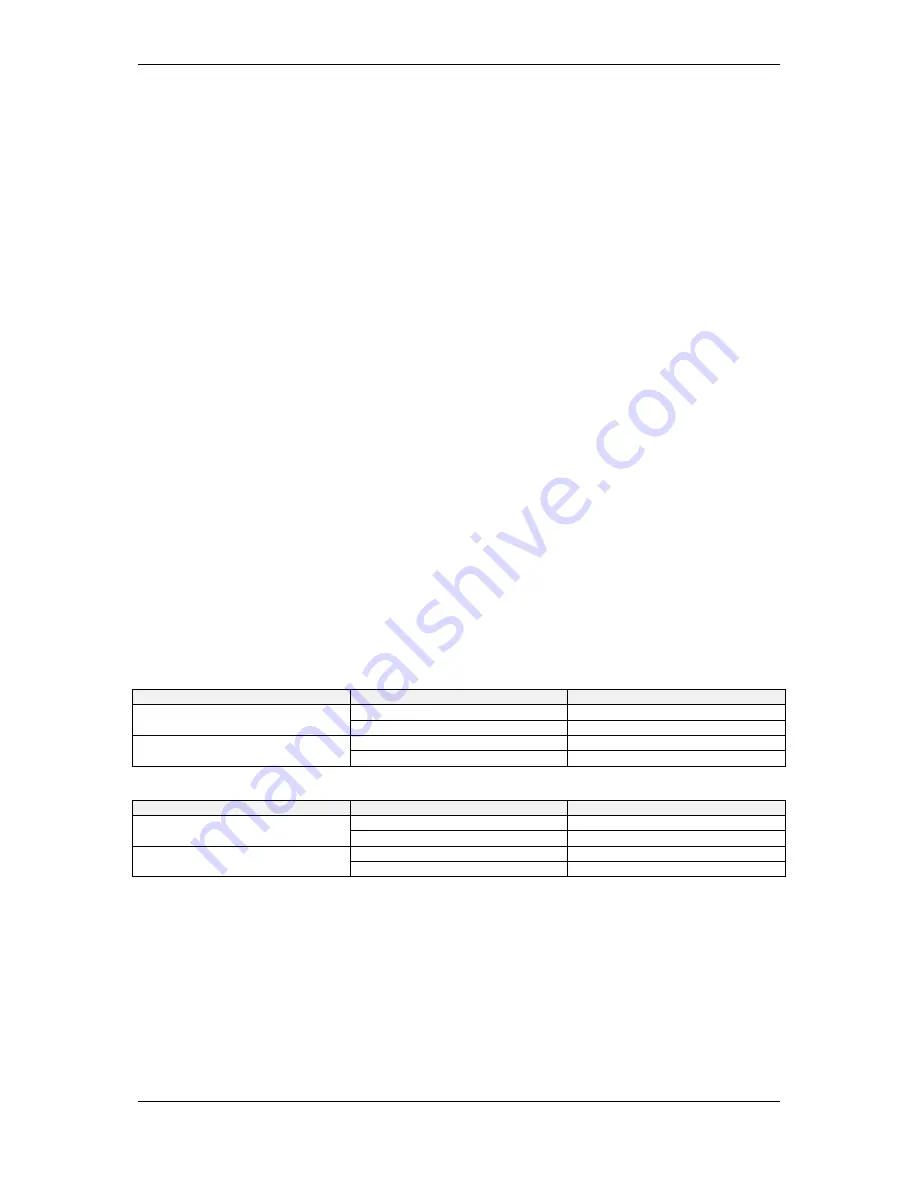
AMD2000 Series - Servo Drive - User Manual
32
DS619-0-00-0019 - Rev 0
ANCA Motion
local requirements based on cable size. Please refer to the relevant standards or legislation for
the region of operation.
Motor Thermal Protection
5.5.11.4
The AMD2000 does not contain its own protection for motor thermal overload. If protection
against motor thermal overload is necessary, the user must supply a thermal fuse according to
the maximum safe operating temperature of the motor being protected. Please refer to
6.11
Motor Thermal Switch
for various ways Motor Protection can be incorporate in the application.
Brake Resistor
5.5.11.5
The AMD 2000 drive does not have an internal protection mechanism for the internal
regeneration resistor, therefore calculating if the internal regeneration resistor is sufficient and if
an additional regeneration resistor is required is paramount. Failure to do this and provide
evidence of these calculations may result in burning out the resistor and voiding the warranty of
your drive.
Please refer to sections
12.5.14 Regenerative Braking
and
12.14 Brake/Regeneration Resistor
for additional information.
5.6
Power Cable Selection
The power and motor cables must be selected according to regional regulations as well as usage and EMC
requirements. Symmetrical shielded motor cables should be used.
The power supply cables must be rated for at least 300V AC.
The cables must be rated to withstand the expected temperature rise due to the current passing through them,
given the conductor diameter, conductor material and installation environment. Such a decision is governed by
local installation regulations.
To comply with EMC regulations, the cable length of the motor armature cable must not exceed 30m. The cable
must be shielded and the shield must be connected to earth at both ends with appropriate terminations. At the
drive end, the armature shield must be connected directly to the drive earth point. It is highly recommended that
an ANCA Motion shielding bracket be used. Cable sizes should follow the wire size recommendations below.
The supply cables must be capable of handling at least the following currents:
Drive
Input supply
Cable current capability, A
AMD2000 3A
1Φ
8
3Φ
5
AMD2000 9A
1Φ
24
3Φ
13
The minimum required wire gauge per phase (based on 75°C Copper wire) is shown below:
Drive
Input supply
Minimum
Φ
wire gauge, mm
2
AMD2000 3A
1Φ
2.0
3Φ
2.0
AMD2000 9A
1Φ
2.5
3Φ
2.0
Refer to
12.4 Electrical Specifications, 13.3 Cables
for further information.