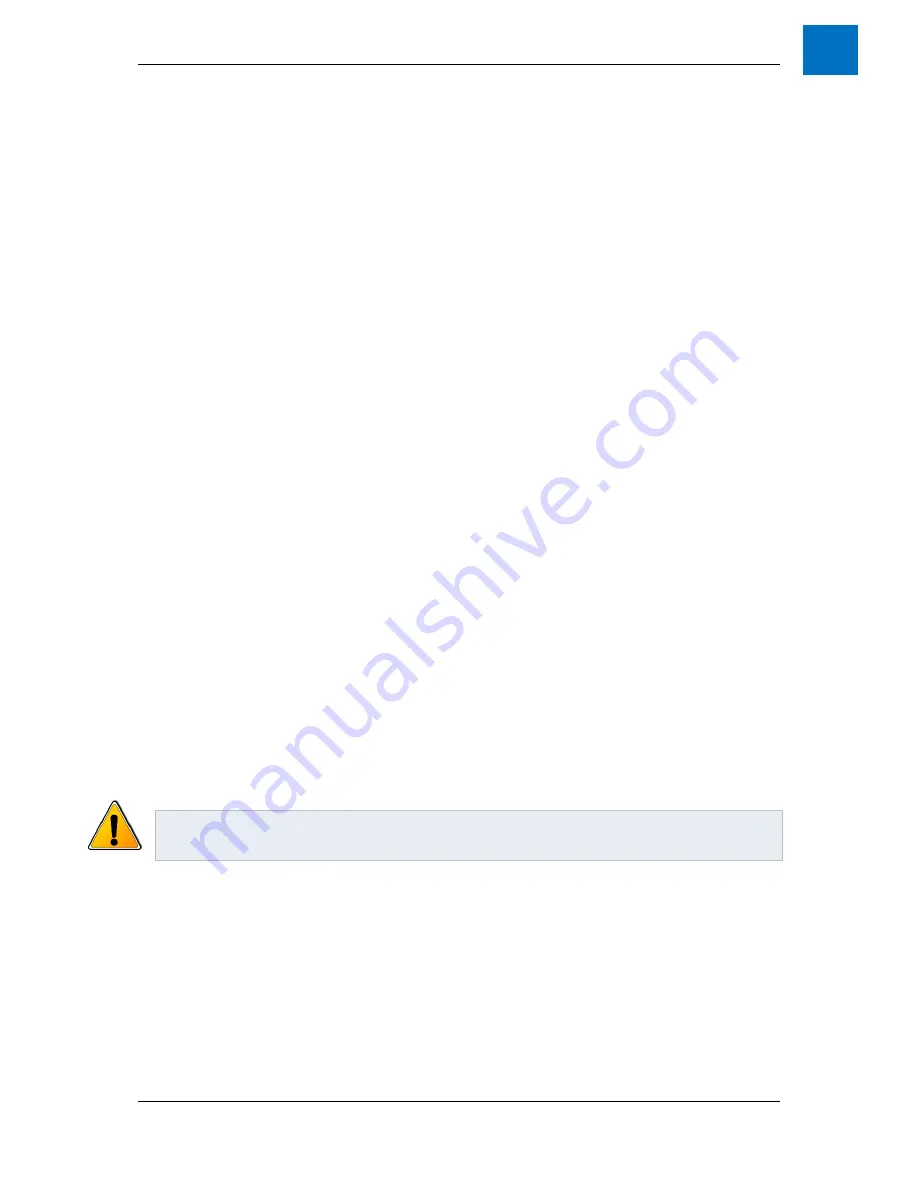
Feature Configuration
ANCA Motion
DS619-0-00-0019 - Rev 0
113
10
The fundamental frequency component of the torque response is below the minimum amplitude
threshold (0.1 Nm). The system may not have been stimulated correctly and hence the alignment
estimate may not be accurate.
E415: Acceleration Observer Torque Response Amplitude High
The fundamental frequency component of the torque response is above the maximum amplitude
threshold (2 Nm). The system may not have been stimulated correctly and hence the alignment
estimate may not be accurate.
E416: Acceleration Observer Torque Response Mean Squared Error
The difference between the predicted torque and the estimated (measured) torque is greater than the
threshold (1 Nm).
10.1.19
Higher Level Functions
Description
The AMD2000 allows the user to select different motion control approaches as Higher Level Functions. These
are described as follows;
1. Numerical Control (NC)
– this is the default function for the drive’s higher level motion control and can
be configured to use position, velocity, or torque control. The choice of set point command is made
using the Operation Modes discussed in section
10.1.23 Operating Modes
of this document. The
information concerning the movement profile and objectives is contained in the SoE profile data. This
choice of control requires an external entity or control unit for supplying the profile data.
2. Drive-Controlled Homing (DCH)
– A homing routine can be executed by the drive in standalone
operation (i.e. without an external control unit). The position feedback is connected to the drive via one
of the two available encoder channels. The home switch is connected to the drive. The home offset
and distance is calculated and retained by the drive.
3. Control Unit Controlled Homing (CUCH)
– A homing routine for the drive that requires control from an
external control unit (e.g. CNC software on a PC). The home offset and distance is calculated and
written to the drive by the control unit.
4. Drive Controlled Moves (DCM)
– The drive may be set to follow a sequence of pre-defined moves
stored in the drive and configurable by the user.
5. Drive Controlled Stroking (DCS)
– the drive undergoes a number of cyclic moves in order to aid tuning
procedures, and for other specific applications that might require such moves.
The AMD2000 defaults to using NC as its higher level function (for details of the Operation Modes settings, and
the nature of the servo controller
. The user may configure “procedure commands” to enable DCH, CUCH, DCM
or DCS. These alternative higher level functions take precedence over NC if they are asserted. Care must be
exercised as it is possible, in some cases, to assert more than one function at a time. Upon completion of such
procedure commands, however, the drive will return to NC automatically.
Warning:
Care must be exercised so that only one higher level function is being executed at any point in
time, otherwise unexpected behaviour may result.
Drive Controlled Homing
Drive Controlled Homing (DCH) is typically used when a control unit (i.e. CNC) is not present. To execute DCH,
the following conditions shall be valid:
Position feedback is connected to the drive via one of the two available encoder inputs.
The home switch is connected directly to the drive via one of its digital inputs.
The home offset displacement is to be calculated internal to the drive.