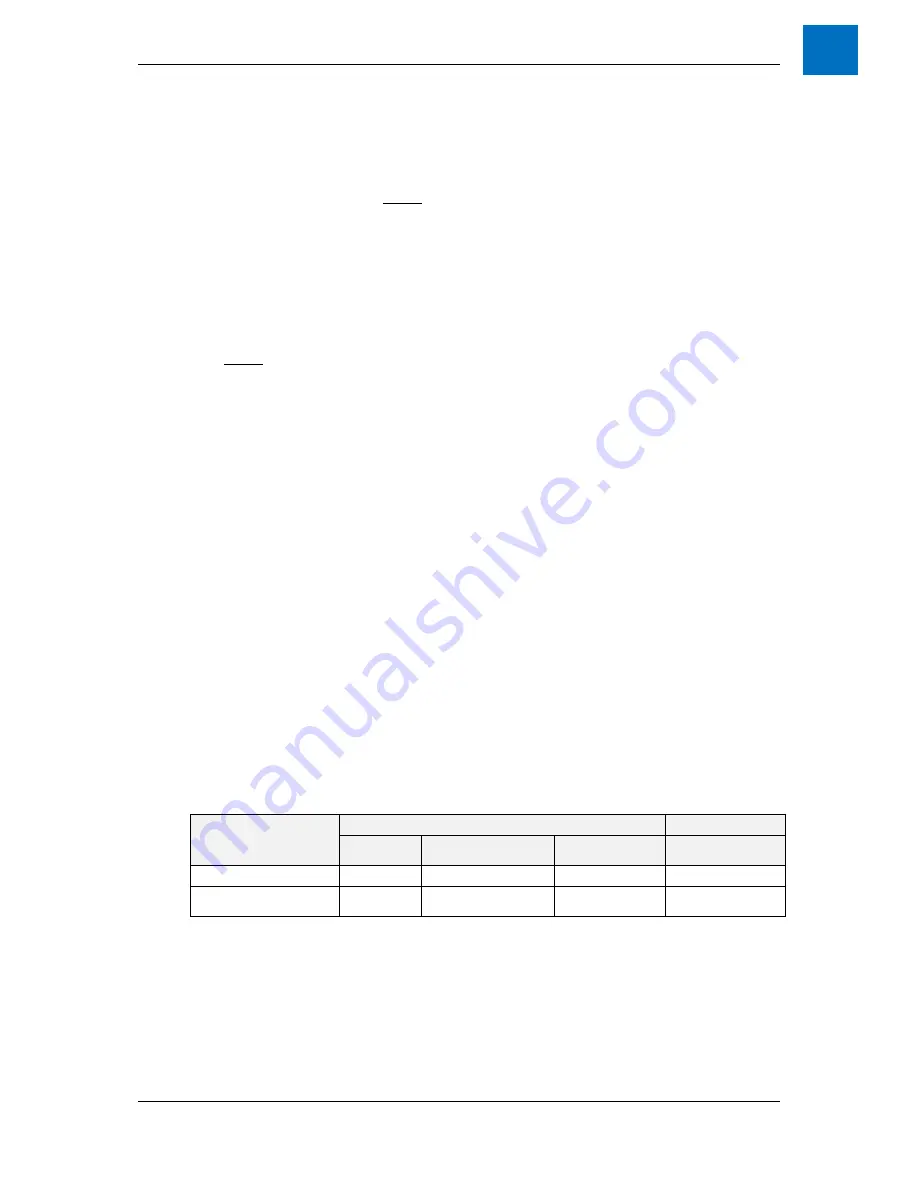
Feature Configuration
ANCA Motion
DS619-0-00-0019 - Rev 0
105
10
10.1.18
Field Orientation Initialisation
Description
A motor rotates due to the forces of attraction/repulsion between magnetic fields situated on the rotor and the
stator where these fields can be generated in a number of different ways. The torque applied to the rotor is a
resolved component of these forces acting
around
the motor shaft. It is proportional to the flux density of the
magnetic fields, as well as a number of other parameters. Where electrical windings are used to generate these
magnetic fields, the field’s flux density is proportional to the current flowing through the winding.
One mechanical revolution of the rotor is usually more than one complete cycle traversing all the winding phases.
That is to say, the sequence of electrical windings for each phase of electricity driving the motor is usually
repeated more than once around the circumference of the motor. Hence, if a single vector is used to collectively
represent the current for all these electrical phases, it must traverse a full 360 ‘electrical’ degrees a number of
times (depending on number of times the phase winding repeat) before completing one mechanical revolution. It
is possible to represent such a single current vector as two component parts; one “quadrature” current, and a
“direct” current. The “quadrature” component of the current vector is most closely associated with the magnetic
forces that act
around
the motor shaft, and reaches its highest value when the electrical angle between the stator
and rotor magnetic fields is near 90 degrees. For optimum torque delivery and motor efficiency, it is essential to
keep this “field angle” at 90 degrees. The algorithm for doing this task is called commutation.
For Permanent Magnet AC (PMAC) motors, successful commutation requires correct initialisation wherein the
rotor field angle is determined relative to a reference position on the stator. This initialisation has many names,
for example: commutation initialisation, field orientation initialisation, phase initialisation. In the AMD2000 drives
it is known as Field Orientation Initialisation (FOI).
It will be noted that in AMD2000 drives, the reference position is aligned with the back-EMF U-phase.
AMD2000 drives support several FOI techniques. These are called:
DQ A
lignment
Acceleration Observer
Analogue Commutation Track
Hall Effect Sensor
For the above FOI techniques;
DQ Alignment
and
Acceleration Observer
can always be used for motors with an incremental encoder
(The AMD2000 does not support absolute encoders at this time).
Analogue Commutation Track
is recommended for motors with incremental analogue encoders that
have commutation tracks, typically found on braked motors;
Hall Effect Sensor
is recommended for motors with Tamagawa (UVW wire saving encoders).
Table 10-1
below lists the possible FOI options for different encoders. It should be noted that to further improve
FOI accuracy for some techniques, post processing (
Alignment Off Index Pulse
) can be conducted for
incremental encoders that possess such an indexing pulse.
Table 10-1 Encoder Types and Possible FOI Algorithms
Encoder Type
FOI Techniques
Post Processing
DQ
Alignment
Analogue
Commutation Track
Acceleration
Observer
Alignment Off
Index Pulse
Incremental
Incremental with
analogue COM track