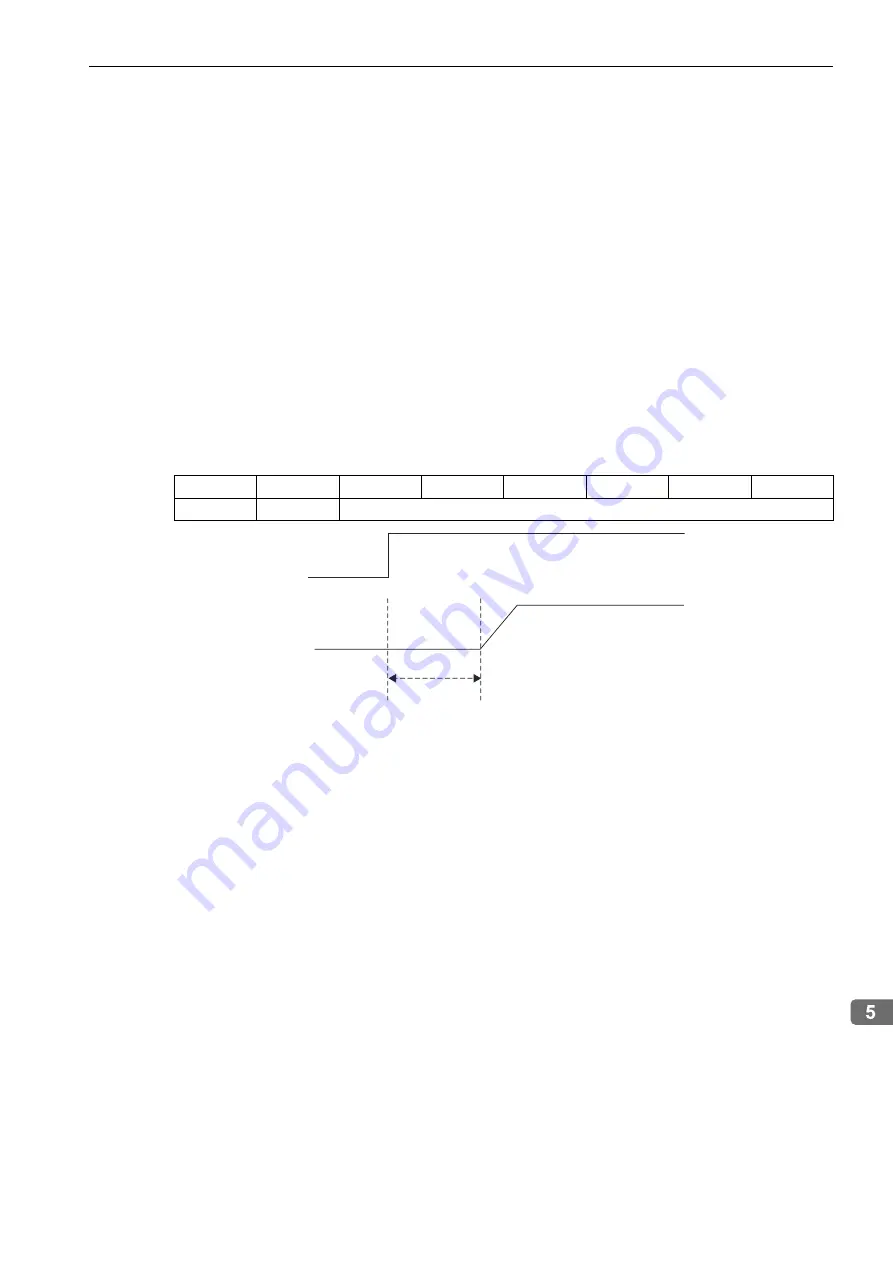
5.3 Tapping Operation
5-17
Spindle Axis
Operation
5.3.2
Spindle Axis Servo Drive-based Position Loop Tapping
To switch to a position loop and perform tapping, Servo Mode must be set to provide a constant excitation cur-
rent to maintain the speed linearity.
Set SVCMD_IO.SV_MOD to 1 in the VELCTRL or INTERPOLATE command.
When SV_MOD is set, 200 to 300 ms of delay is required to establish 100% of the required excitation current.
(Allocate this time with a timer on the host controller.)
Be careful, because any position references that are sent during this time will not function correctly and cause
vibration.
Additional Information
• Servo Mode establishes and maintains feed linearity and continuously provides excitation current, even
when the axis is stopped.
This preserves control loop response and increases constraint when the axis is stopped in the same way as a
servo.
• If SV_MOD is turned OFF, the excitation current is not supplied when the axis is stopped.
Also, the constraint when the axis is stopped is reduced.
The following figure shows the relationship between Servo Mode and the INTERPOLATE command.
SVCMD_IO.SV_MOD
Therefore, the INTERPOLATE command can be executed 200 to 300 ms after the mode is changed to Servo
Mode for tapping and other spindle axis feeding operations.
If tapping is continued, SV_MOD will not turn ON or OFF, producing a constant reference.
For a position loop for a spindle axis, you can send the MECHATROLINK-III INTERPOLATE command to
smoothly change from speed control to position loop control as long as Servo Mode is set and the constant
torque range is not exceeded.
Bit 31
Bit 30
Bit 29
Bit 28
Bit 27
Bit 26
Bit 25
Bit 24
WND_CHG
SV_MOD
Reserved.
200 to 300 ms
SVCMD_IO.SV_MOD
INTERPOLATE