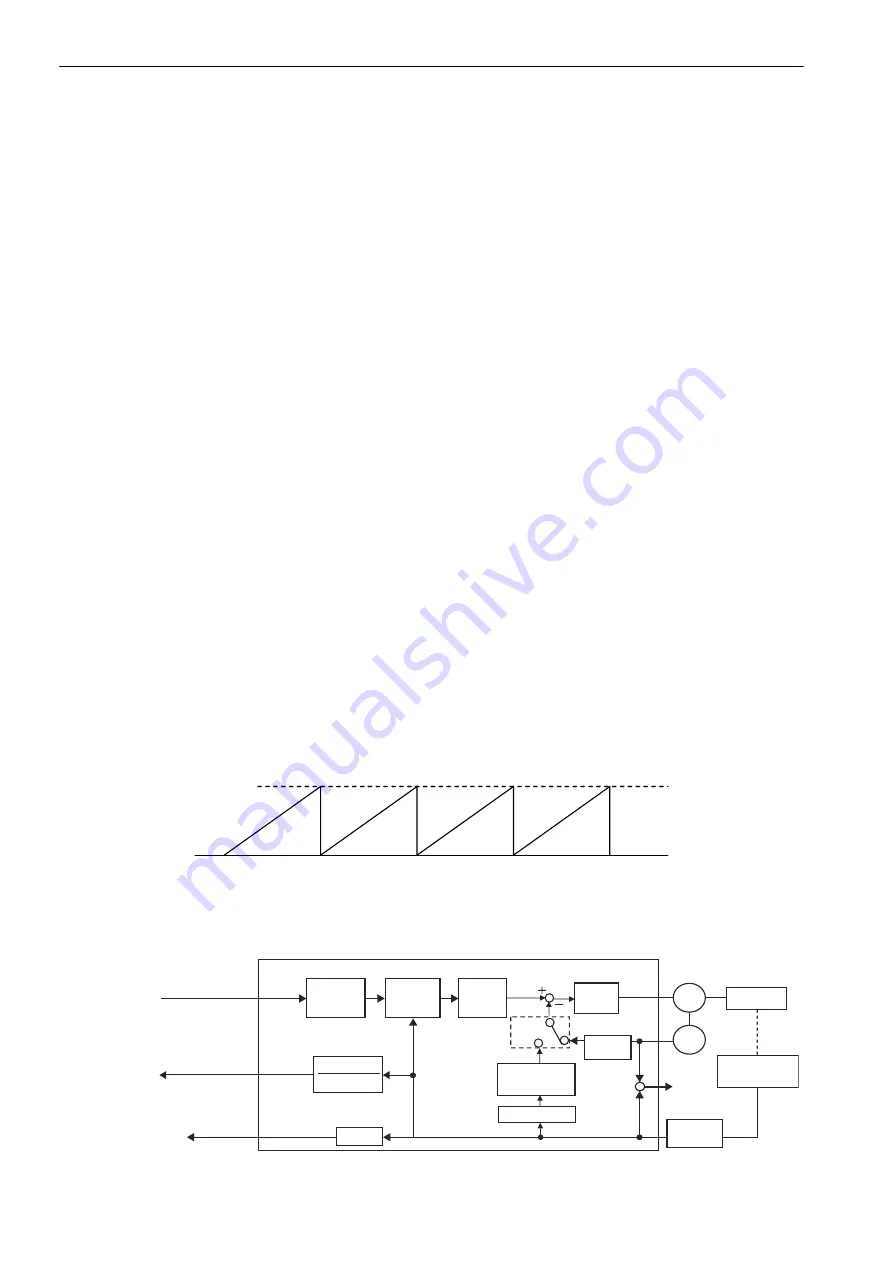
6 Additional Functions
6.1.1 Infinite-length Encoders
6-2
6.1
C-S Axis Control
C axis control is required for some lathing.
There are two types of C axes: simple C axes and high-precision C axes.
Simple C axes have a reference unit of 0.001 degrees, while high-precision C axes require even higher preci-
sion.
C axes require their own external encoder, for which a serial encoder is normally used.
Generally, an encoder for fully-closed loop control is used.
Motor encoder:
18 bits
External encoder:
1,200 slits, 256x (capable of 12,000 revolutions)
1,200 slits, 4,096x (capable of 5,400 revolutions)
To perform C-S control, you can use a Heidenhain sine-wave output (1 V) encoder for fully-closed loop con-
trol.
The motor encoder, external encoder, and fully-closed specifications must be set in parameters to support C-S
axes when the power supply is turned ON.
6.1.1
Infinite-length Encoders
Make the following settings for counter control when the power supply is turned ON.
• APSO = 0
• TPOS = 0
• POS in CNC = 0
• Poscount = 0
Position management is performed with these current values as a base.
Make the following settings for position management in normal operation.
360,000 reference units for 1,200 slits and 256x multiplier = 307,200
Δ
POS = APOS (i+1) - APOS (i)
POS (i+1) = POS (i) +
Δ
POS
if POS (i+1)
≥
307,200 POS (I + 1) = POS (I + 1) -307,200 Poscount = + 1
if POS (I+1) < 0
POS (i+1) = 307,200 + POS (I + 1) Poscount = - 1
Note: APOS can be counted as 2*n.
Make the following settings for reference unit conversion and reverse conversion.
Reference unit conversion: Convert the reference number of pulses of 0 to 360,000 to 0 to 307,200.
Reference unit reverse conversion: Convert the feedback number of pulses of 0 to 307,200 to 0 to 360,000.
To perform speed control with fully-closed loop control, it also needs to be set in a parameter.
(1) Using an Infinite-length Encoder in Position Control
Note: Either an incremental encoder or absolute encoder can be used, but for an absolute encoder, you must set Pn002.2 to
1 and use the encoder as an incremental encoder.
N
N
N
N
A.d10
ENC
1
Pn22A
External
encoder
Serial
conversion
Alarm
detection
Speed conversion
Unit conversion
Pn20A
Speed
conversion
Dividing
Electronic gear
Speed
feedback
Machine
Motor
Speed
loop
Position
loop
Error
counter
Electronic
gear
Encoder divided
pulse output
MECHATROLINK
monitoring data
MECHATROLINK
motion command
SERVOPACK